WATER CURTAIN
being part of the fire protection system
WATER CURTAIN
being part of the fire protection system
The water curtain system is strategically installed on the ship at the final stage of the evacuation route leading to the lifeboats, acting as a critical safety measure to protect the crew during emergency evacuations. This system creates a continuous barrier of water, effectively shielding evacuees from extreme heat, open flames, and hazardous smoke, which are common risks during onboard fires.
By significantly reducing radiant heat exposure and limiting the spread of flames, the water curtain enhances survivability and ensures that the evacuation path remains accessible for a longer period. Additionally, it helps to control smoke movement, improving visibility and reducing the risk of inhalation injuries, which is essential for maintaining order and efficiency during an emergency escape.
Integrated into the ship’s fire protection system, the water curtain is designed to operate automatically or be manually activated when needed, ensuring immediate response in critical situations. Its deployment is carefully engineered to work seamlessly with other fire suppression and safety measures, creating a comprehensive defense against fire hazards.
This system serves as a key operational component in ensuring the effectiveness of emergency evacuation procedures, significantly improving the probability of a successful evacuation even under severe fire conditions. By enhancing protection in the most vulnerable stage of escape, the water curtain contributes to overall maritime safety and ensures compliance with stringent fire safety regulations.
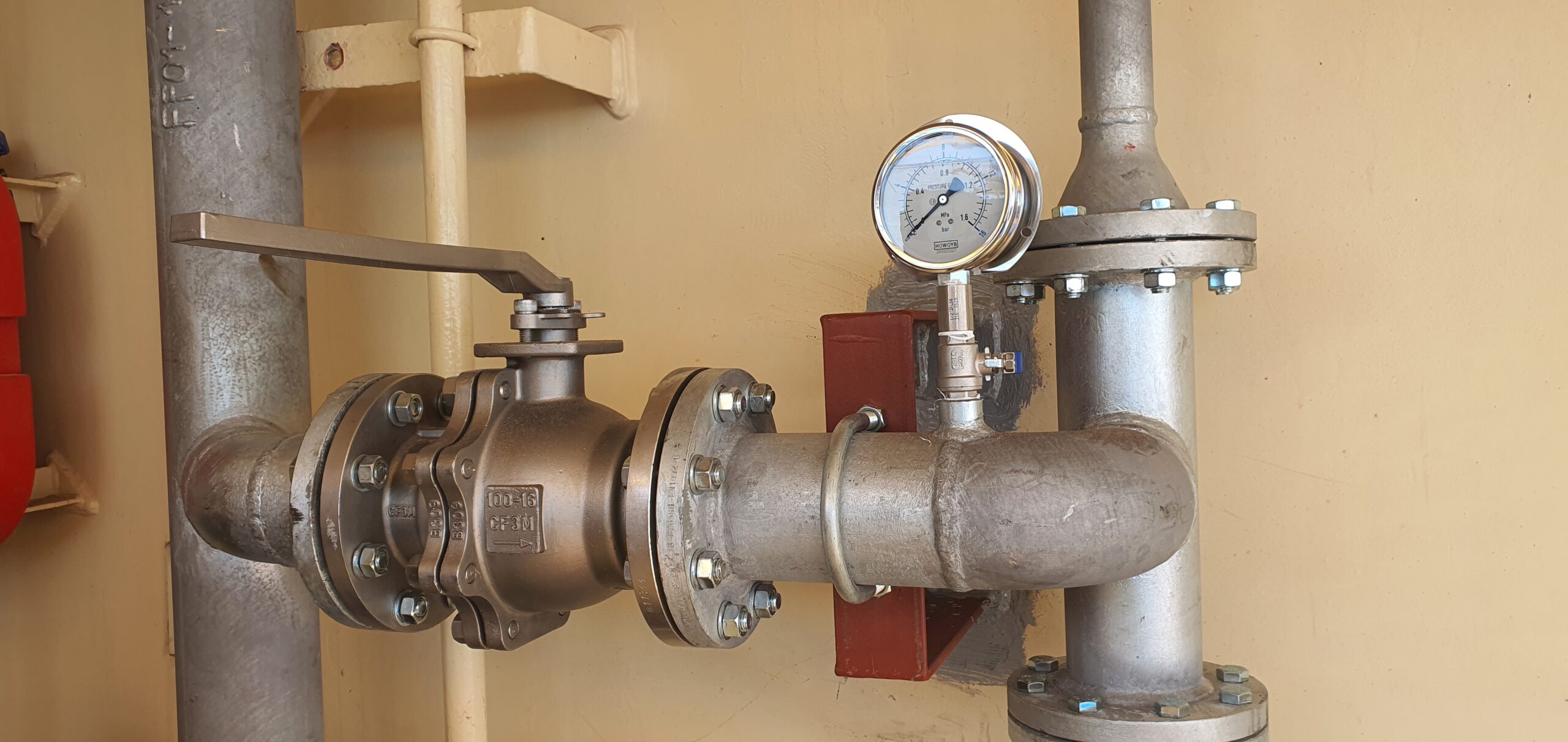

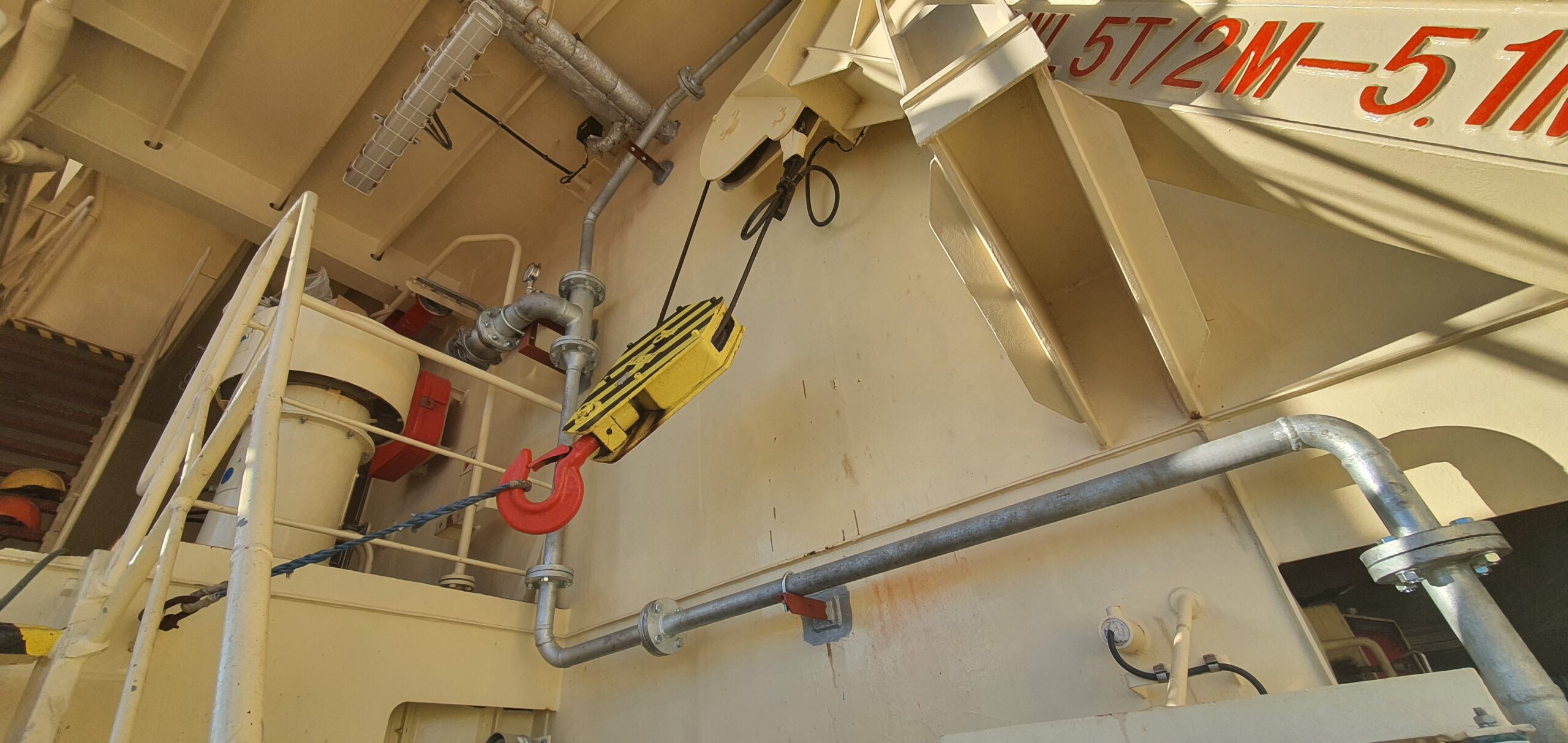
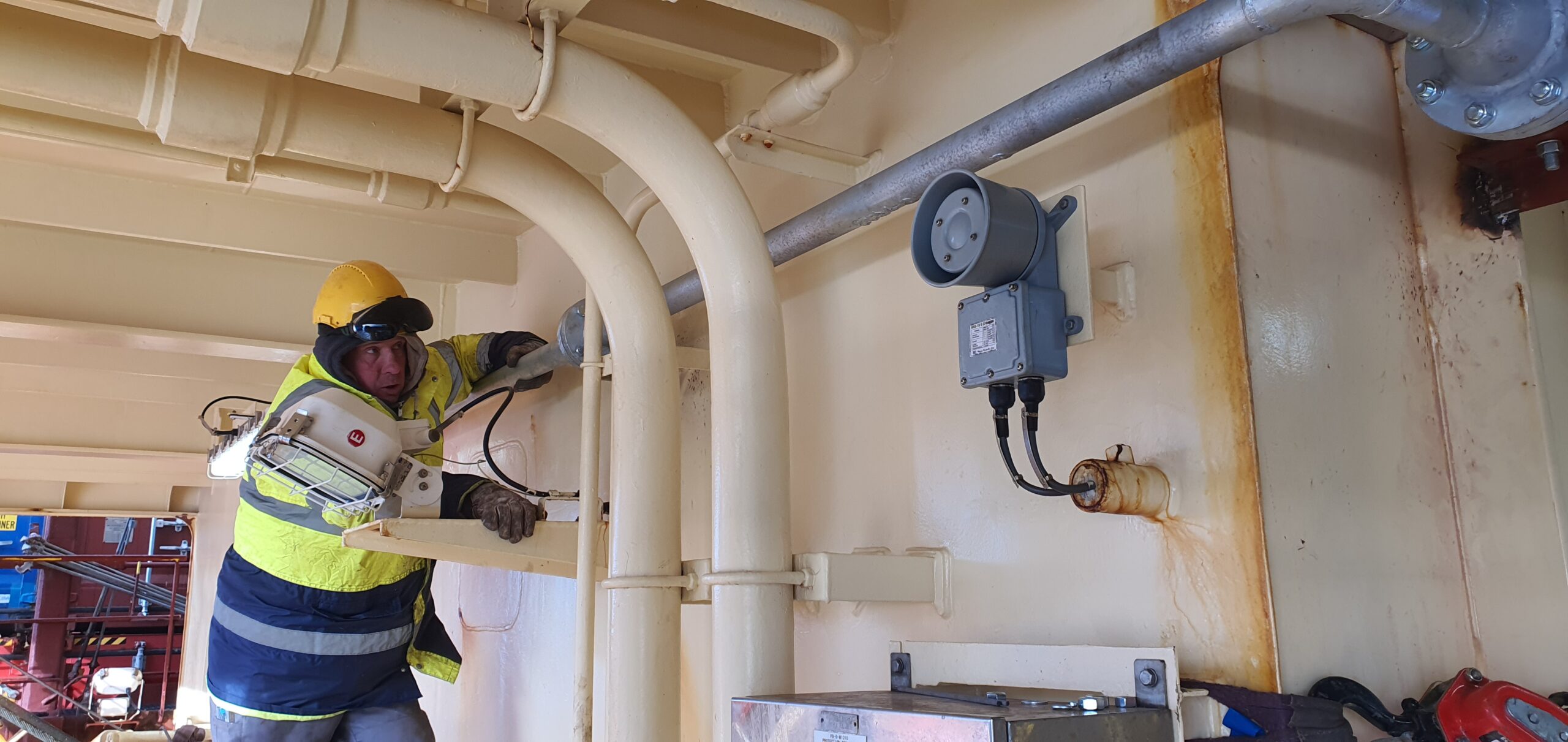
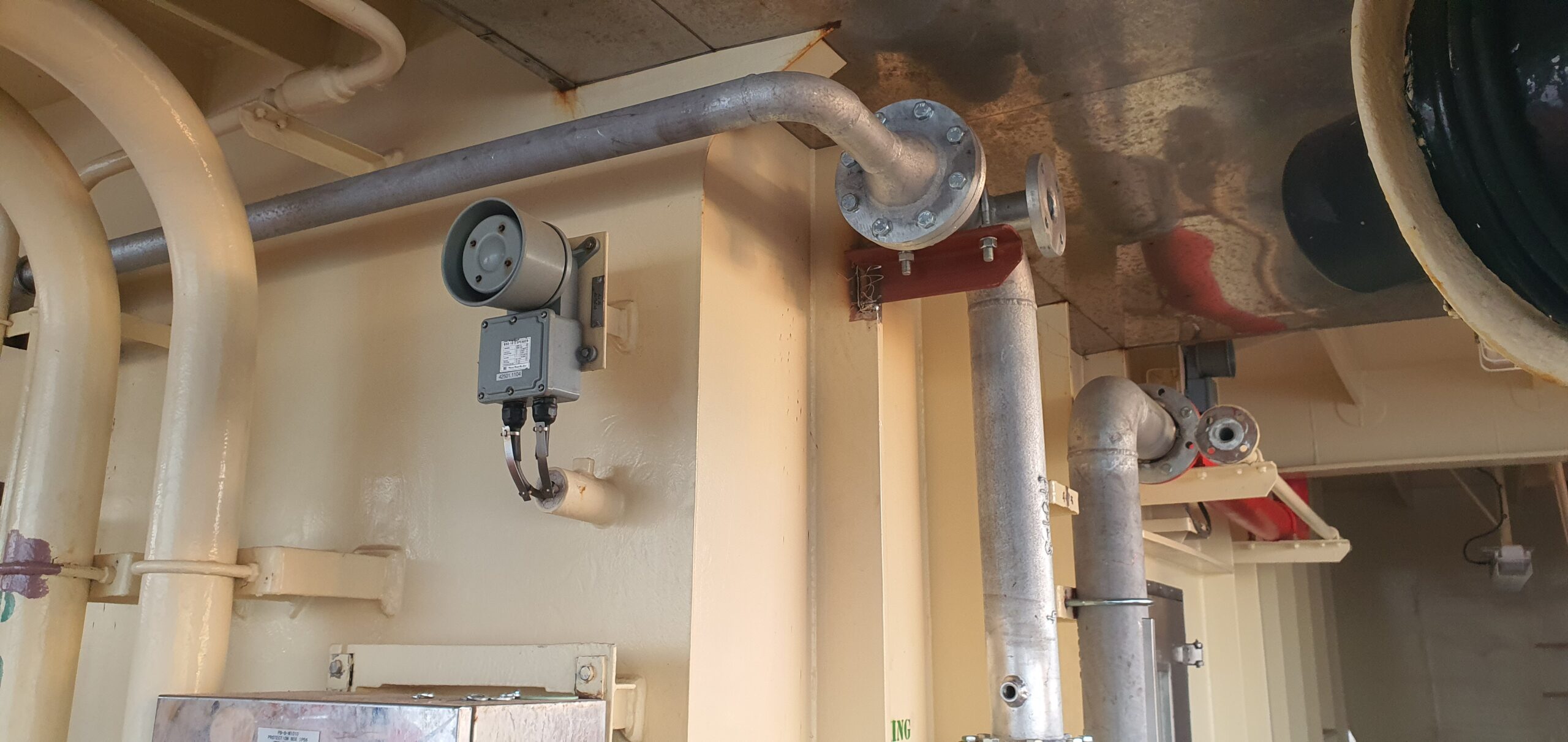
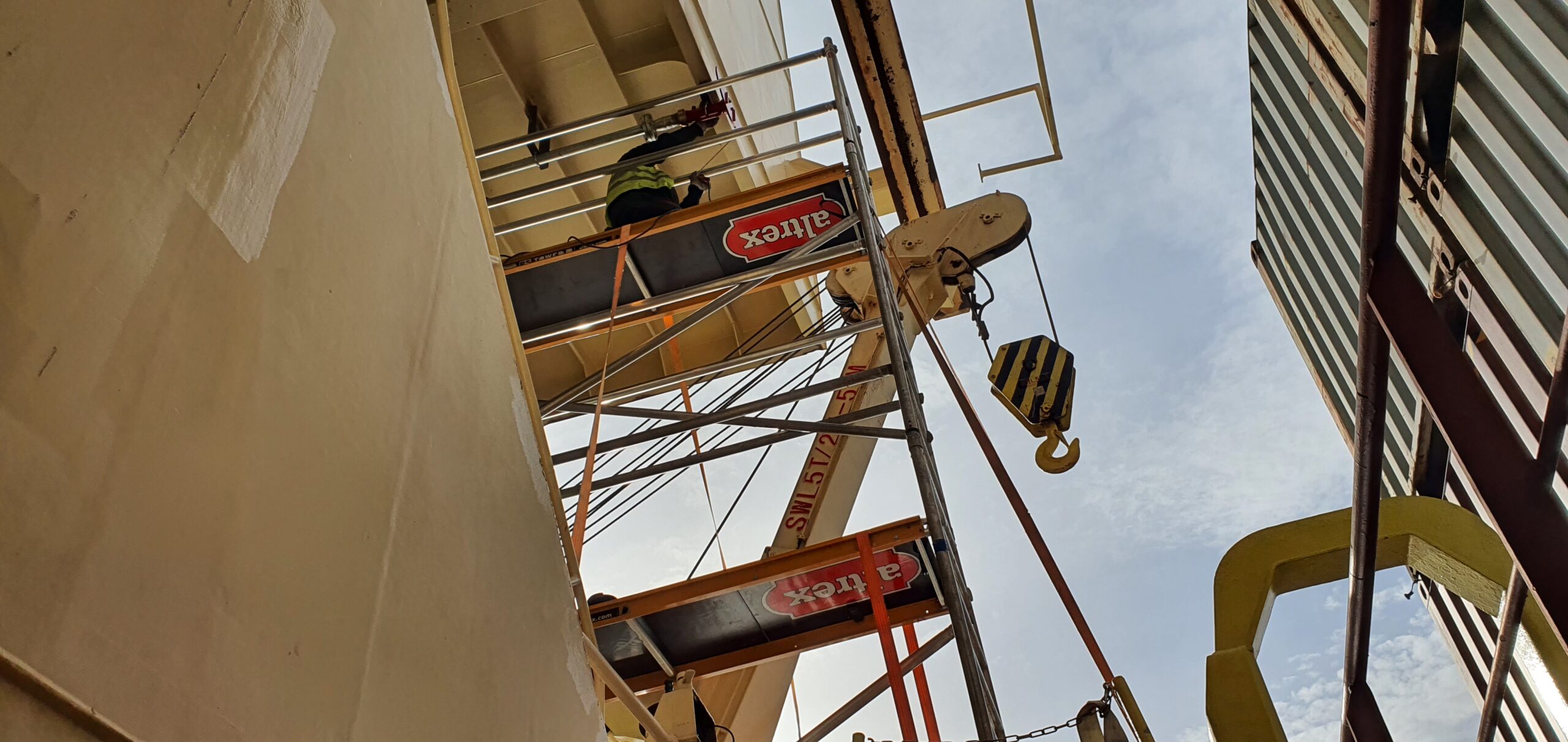
As part of the implementation of the water curtain system on the ship, we carry out a comprehensive process that includes 3D scanning, project development and documentation, prefabrication, pressure testing, and installation. Each of these stages is carefully planned to ensure the highest quality of execution, compliance with regulations, and minimal impact on the vessel’s operations.
The process begins with precise 3D scanning of the ship, allowing for an accurate representation of its structure and existing installations. This enables us to design the water curtain system optimally, taking into account spatial constraints and the specific requirements of the vessel. Based on the collected data, we prepare complete technical documentation and a detailed installation project that complies with all applicable fire safety standards and regulations.
Once the design phase is completed, we proceed with the prefabrication of system components, including pipelines, water nozzles, valves, and mounting structures. The entire process takes place under controlled workshop conditions, ensuring the highest quality of manufacturing and reducing installation time on board. After prefabrication, we conduct pressure testing to verify the system’s tightness and strength, ensuring its reliable operation under real-life conditions.
The fully tested components are then transported to the vessel, where we carry out the installation during its port stay. Thanks to prior prefabrication, pressure testing, and precise planning, we minimize downtime and disruptions to the ship’s operations.
By utilizing modern technologies and the expertise of our team, we provide a comprehensive solution that enhances crew safety during evacuation while fully meeting industry requirements and fire protection standards.
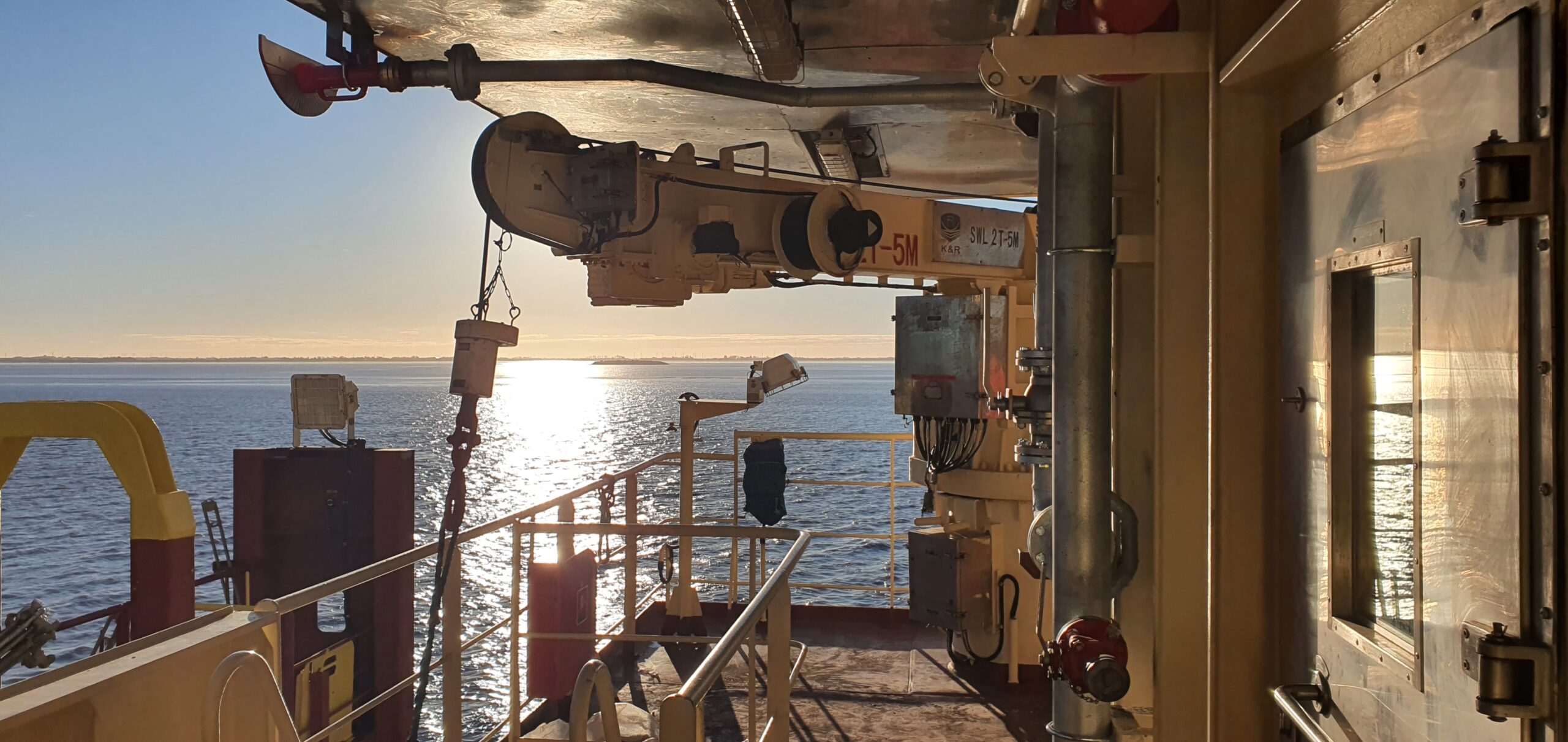
The water curtain system is strategically installed on the ship at the final stage of the evacuation route leading to the lifeboats, acting as a critical safety measure to protect the crew during emergency evacuations. This system creates a continuous barrier of water, effectively shielding evacuees from extreme heat, open flames, and hazardous smoke, which are common risks during onboard fires.
By significantly reducing radiant heat exposure and limiting the spread of flames, the water curtain enhances survivability and ensures that the evacuation path remains accessible for a longer period. Additionally, it helps to control smoke movement, improving visibility and reducing the risk of inhalation injuries, which is essential for maintaining order and efficiency during an emergency escape.
Integrated into the ship’s fire protection system, the water curtain is designed to operate automatically or be manually activated when needed, ensuring immediate response in critical situations. Its deployment is carefully engineered to work seamlessly with other fire suppression and safety measures, creating a comprehensive defense against fire hazards.
This system serves as a key operational component in ensuring the effectiveness of emergency evacuation procedures, significantly improving the probability of a successful evacuation even under severe fire conditions. By enhancing protection in the most vulnerable stage of escape, the water curtain contributes to overall maritime safety and ensures compliance with stringent fire safety regulations.
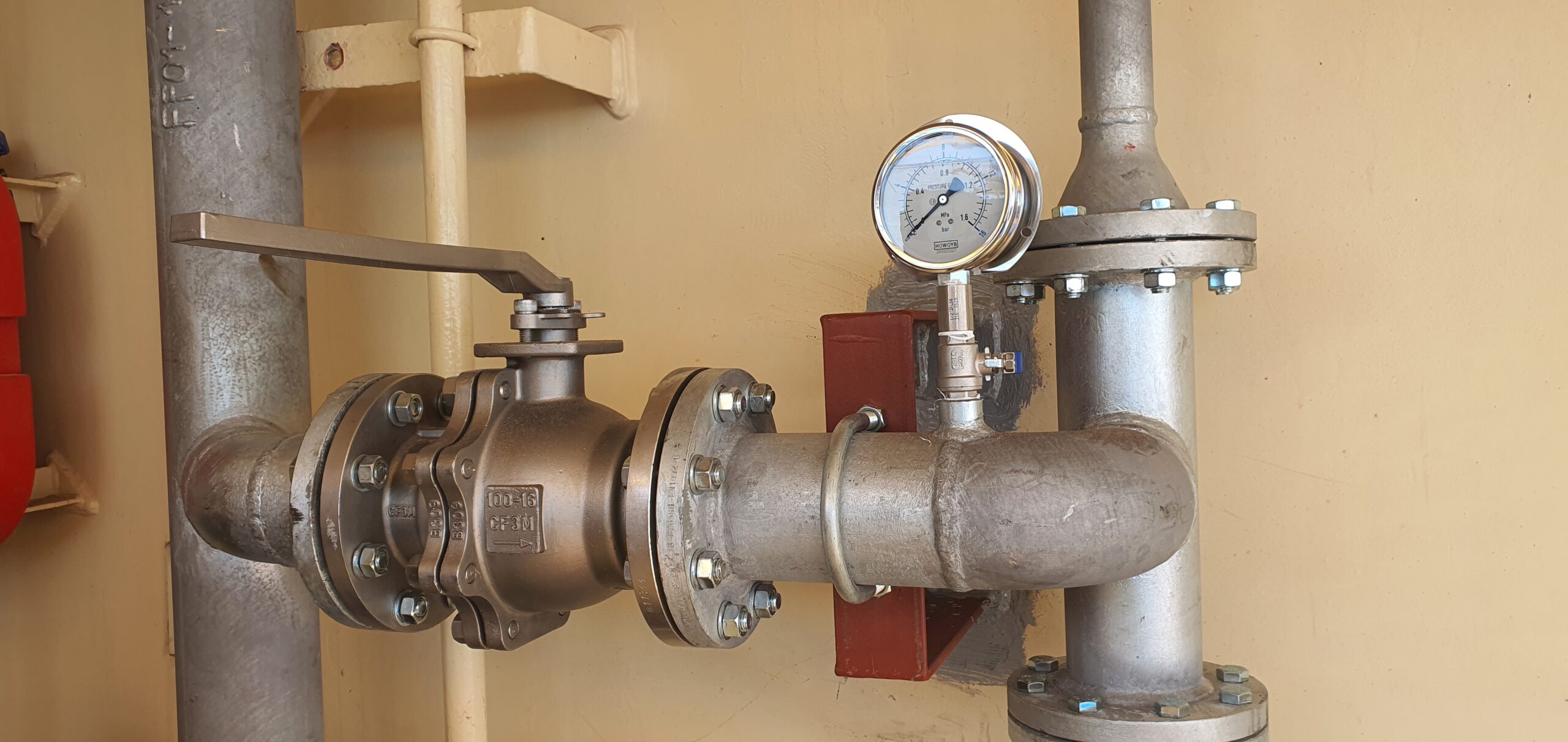
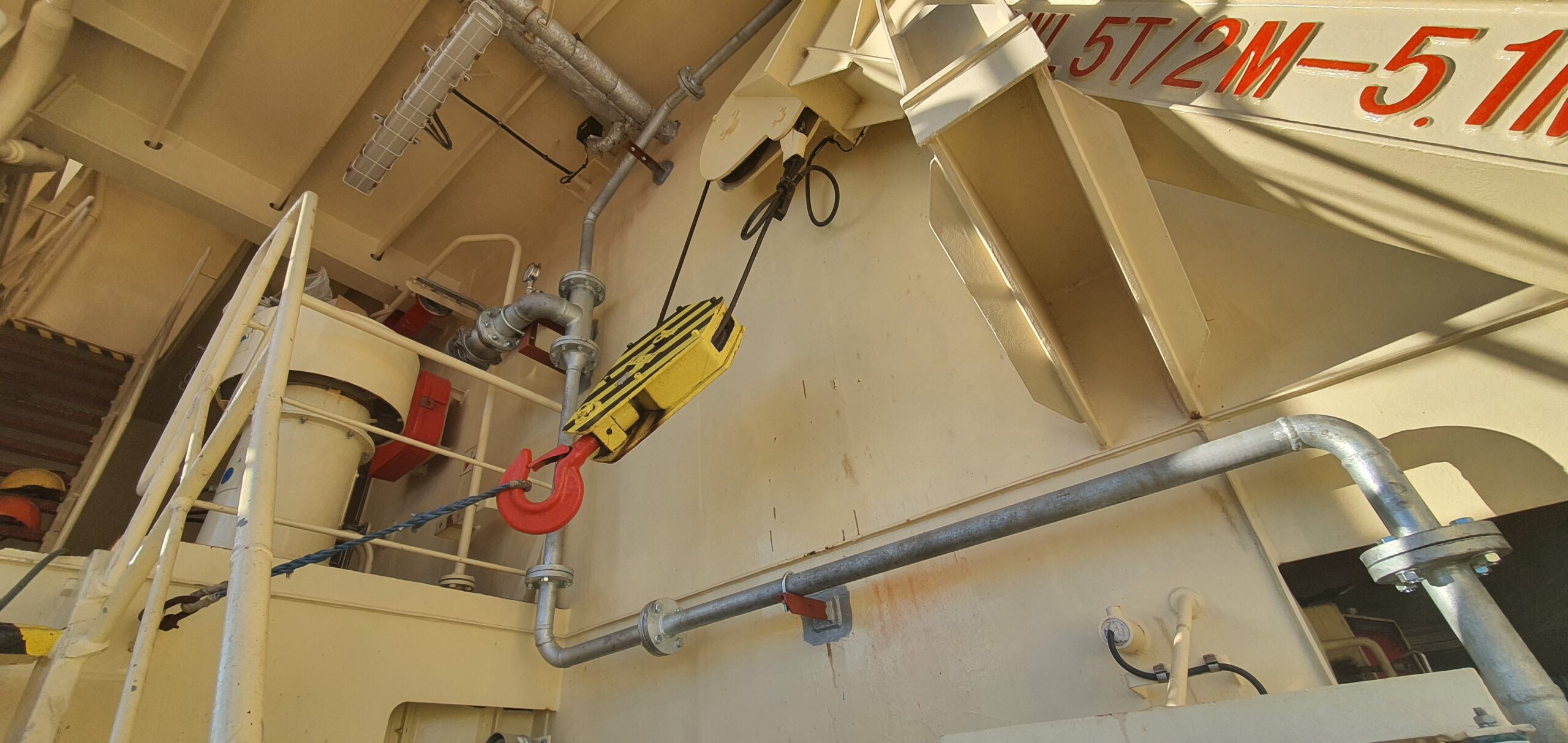
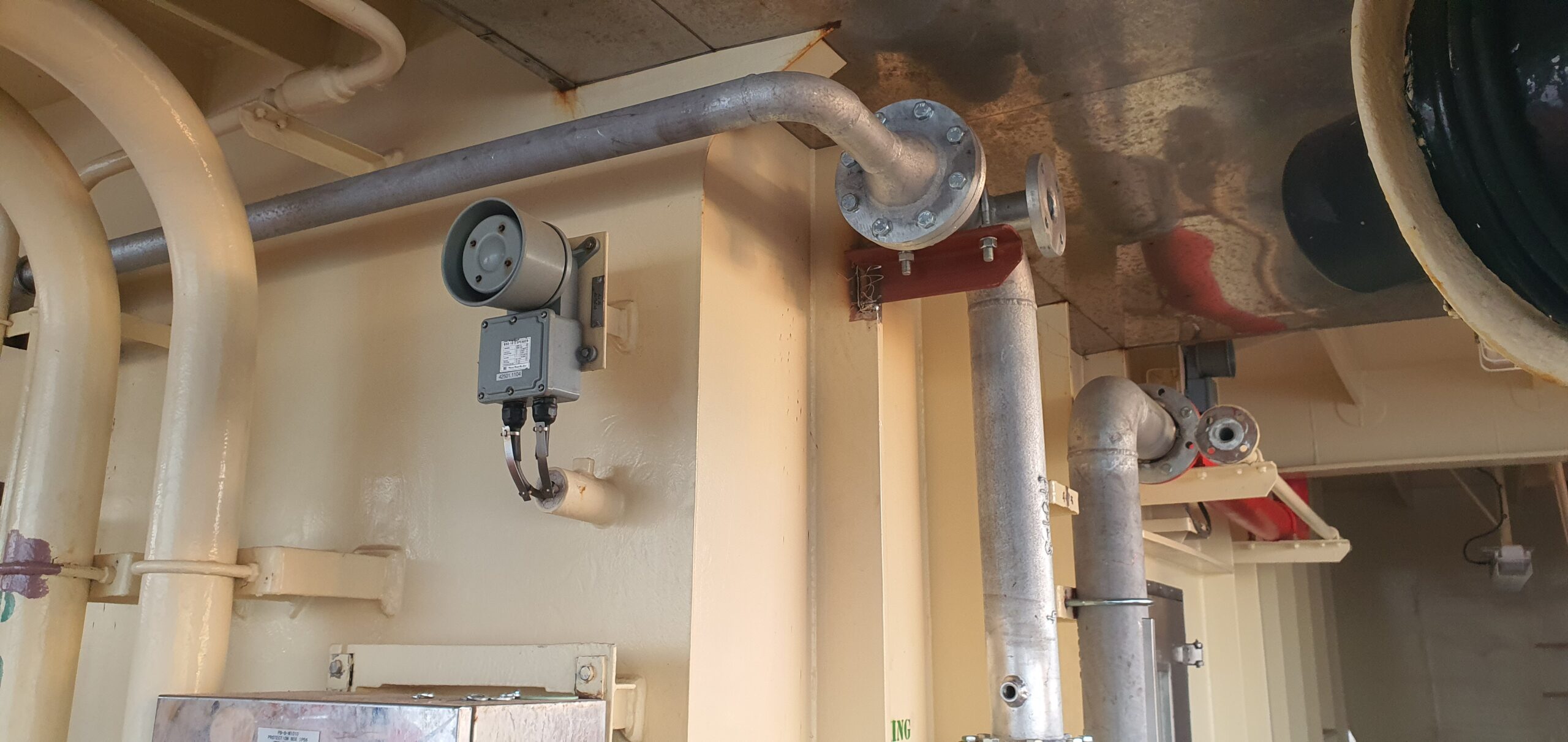

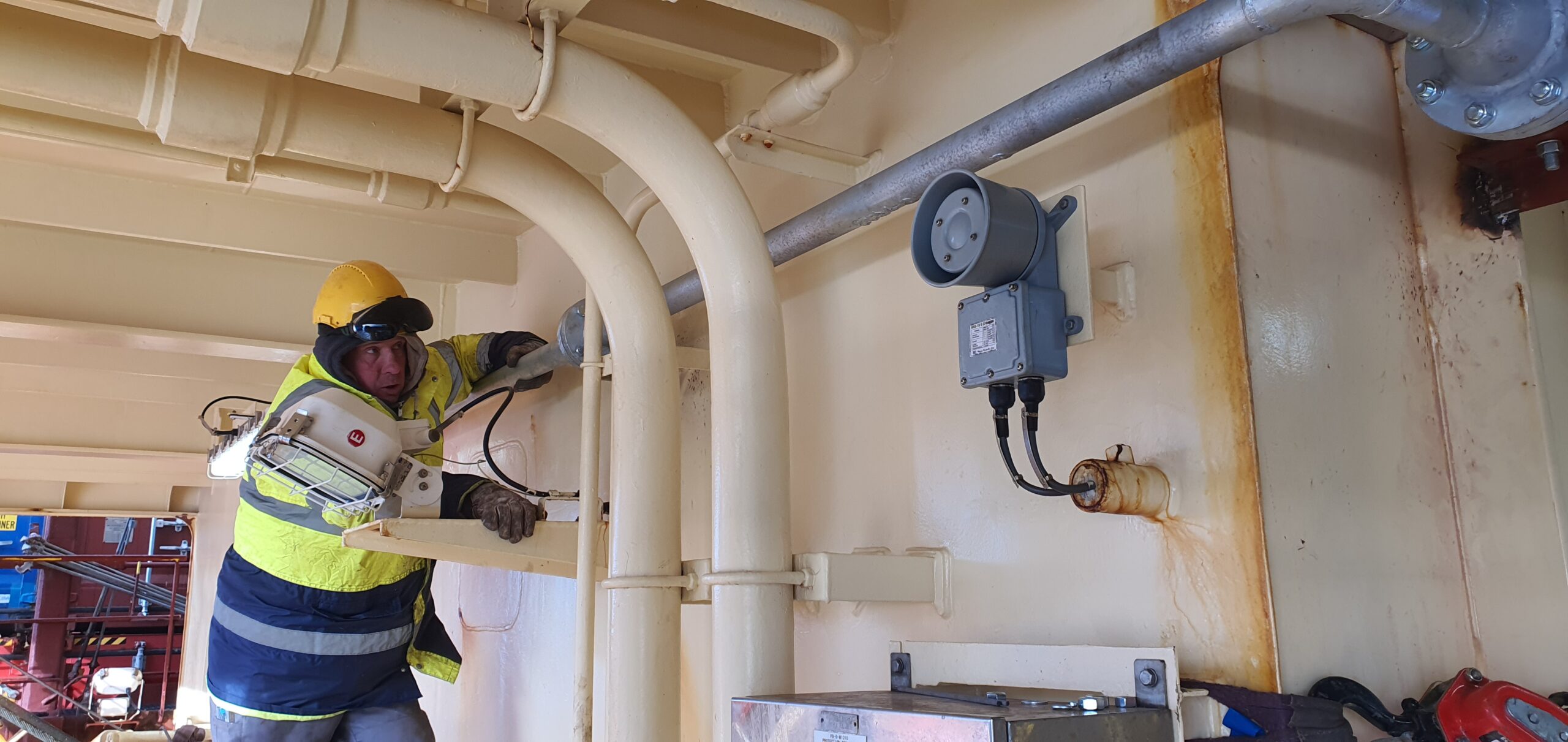
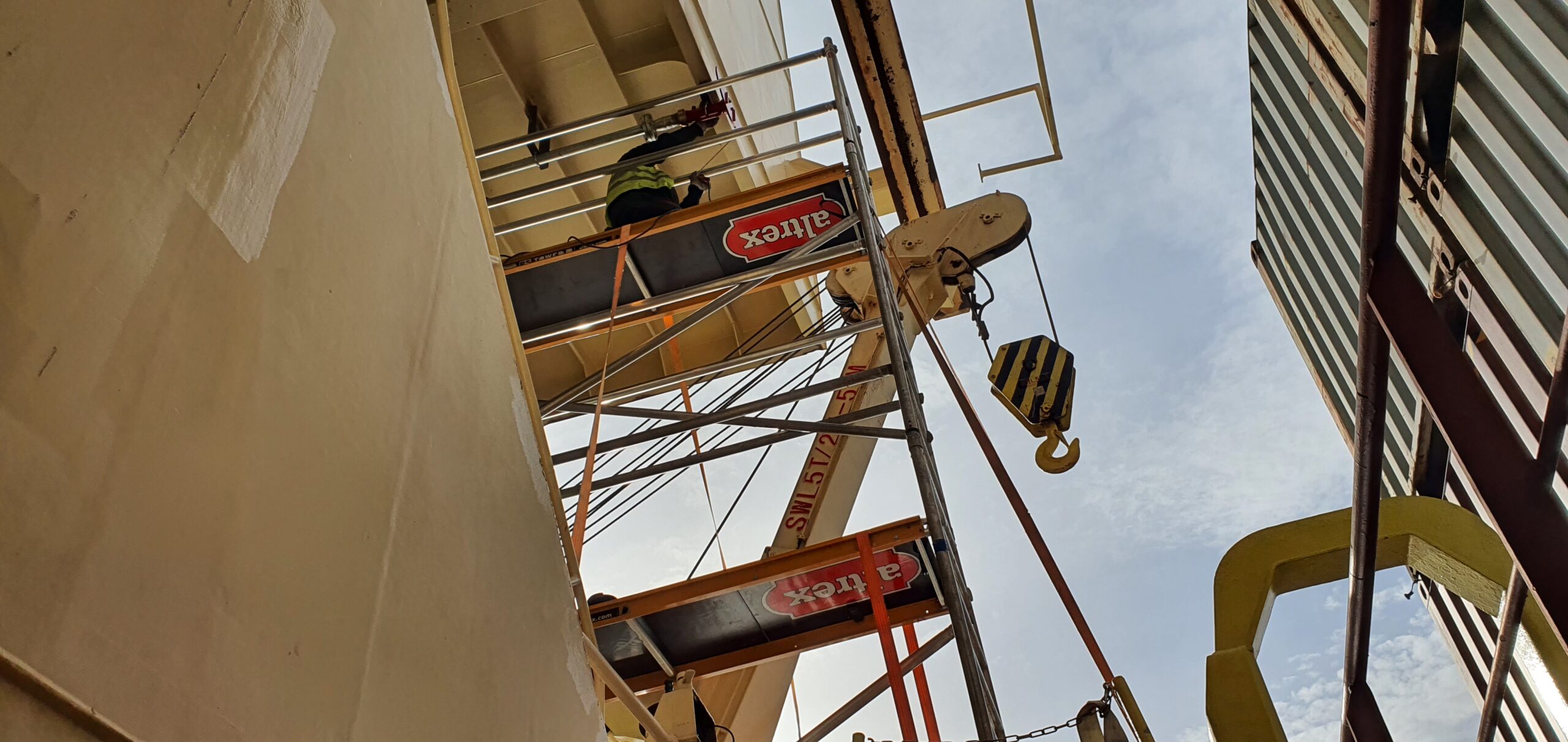
As part of the implementation of the water curtain system on the ship, we carry out a comprehensive process that includes 3D scanning, project development and documentation, prefabrication, pressure testing, and installation. Each of these stages is carefully planned to ensure the highest quality of execution, compliance with regulations, and minimal impact on the vessel’s operations.
The process begins with precise 3D scanning of the ship, allowing for an accurate representation of its structure and existing installations. This enables us to design the water curtain system optimally, taking into account spatial constraints and the specific requirements of the vessel. Based on the collected data, we prepare complete technical documentation and a detailed installation project that complies with all applicable fire safety standards and regulations.
Once the design phase is completed, we proceed with the prefabrication of system components, including pipelines, water nozzles, valves, and mounting structures. The entire process takes place under controlled workshop conditions, ensuring the highest quality of manufacturing and reducing installation time on board. After prefabrication, we conduct pressure testing to verify the system’s tightness and strength, ensuring its reliable operation under real-life conditions.
The fully tested components are then transported to the vessel, where we carry out the installation during its port stay. Thanks to prior prefabrication, pressure testing, and precise planning, we minimize downtime and disruptions to the ship’s operations.
By utilizing modern technologies and the expertise of our team, we provide a comprehensive solution that enhances crew safety during evacuation while fully meeting industry requirements and fire protection standards.
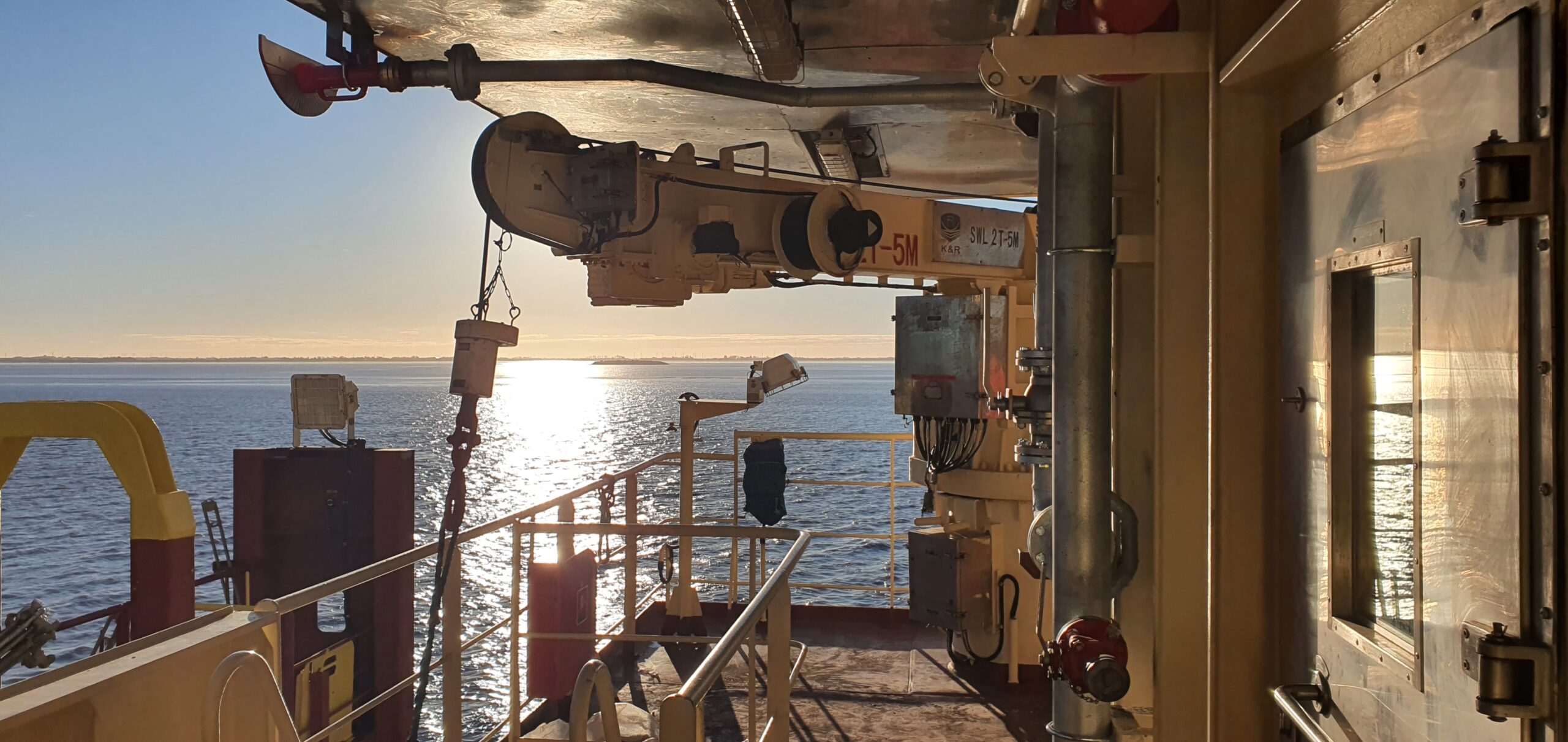