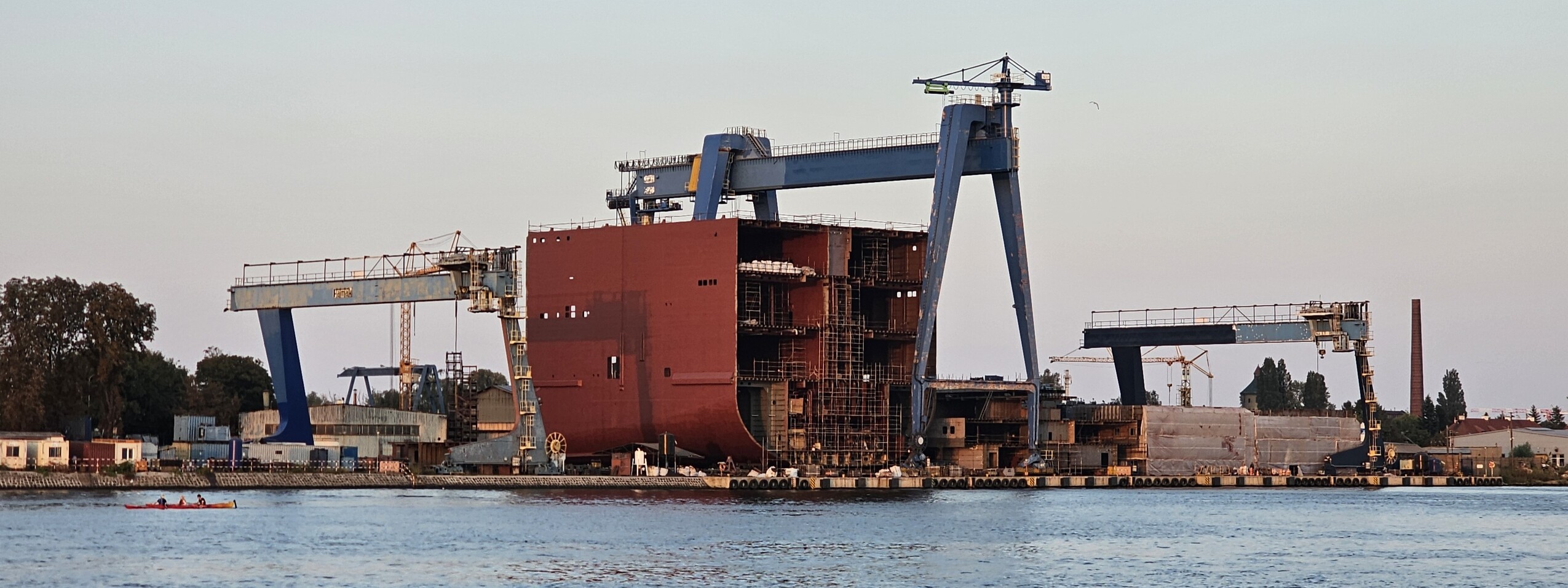
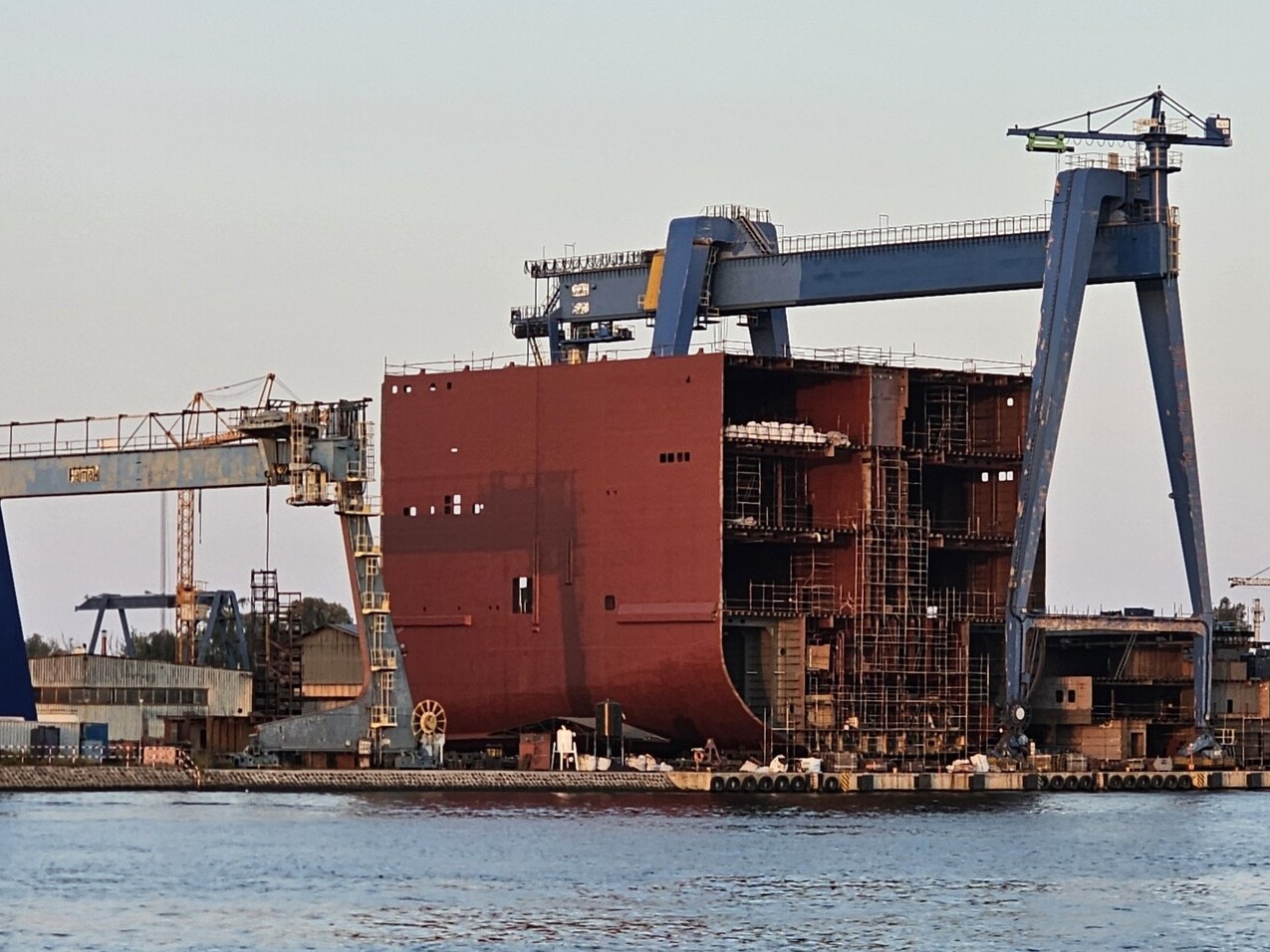
Design & Engineering
Design & Engineering encompasses a comprehensive process of engineering development, integrating both new concepts and the enhancement of existing solutions. The services include technical analyses, structural optimization, and the preparation of complete documentation in compliance with classification and contractual requirements. Additionally, the process involves strength and dynamic assessments, as well as documentation updates following vessel modernization. This ensures that every solution is refined for functionality, safety, and adherence to industry standards.
Design & Engineering
Design & Engineering encompasses a comprehensive process of engineering development, integrating both new concepts and the enhancement of existing solutions. The services include technical analyses, structural optimization, and the preparation of complete documentation in compliance with classification and contractual requirements. Additionally, the process involves strength and dynamic assessments, as well as documentation updates following vessel modernization. This ensures that every solution is refined for functionality, safety, and adherence to industry standards.
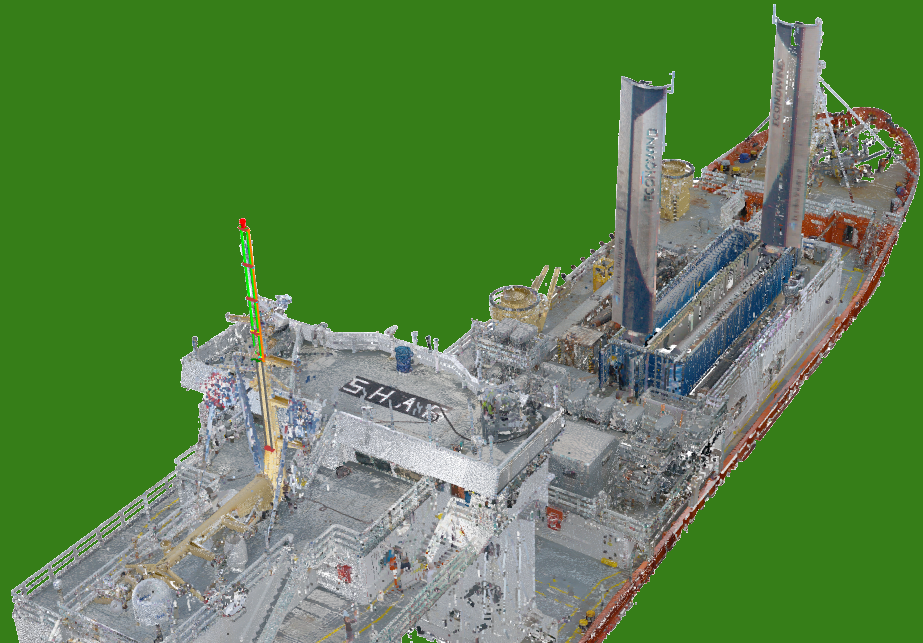

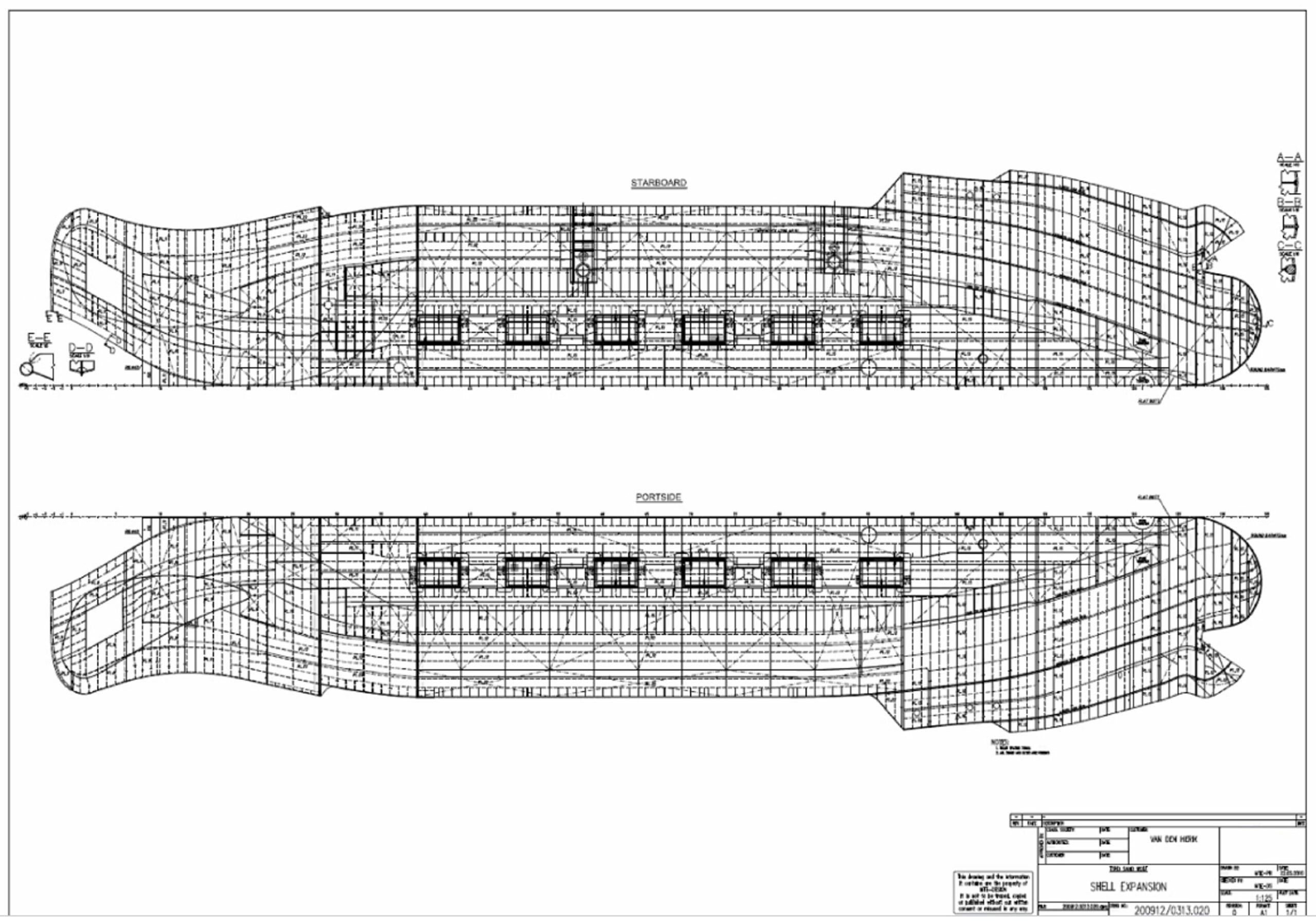
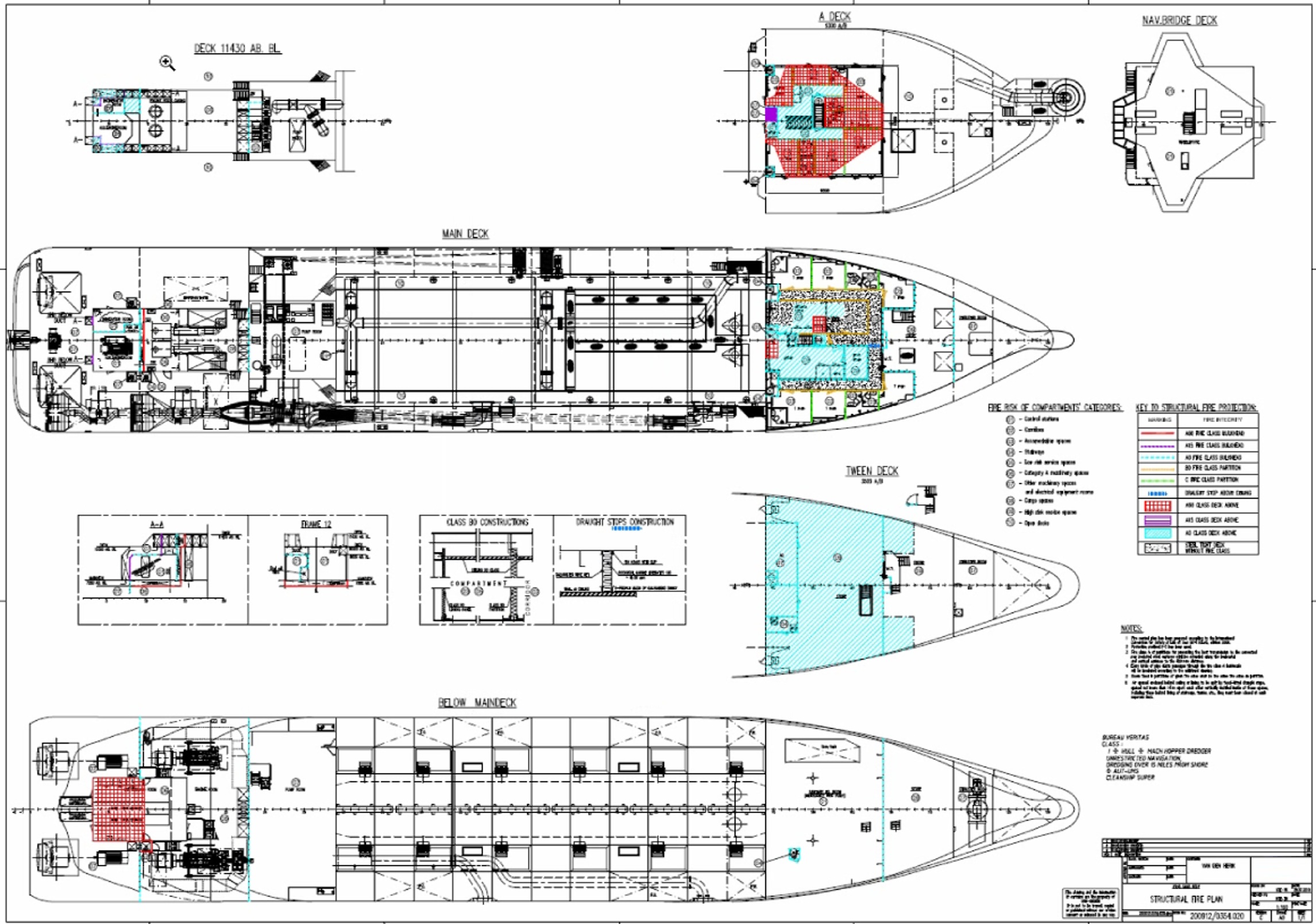
-
contract documentation – preparation of essential documents required for the contract between the shipowner and the shipyard. This includes principal dimensions and technical data, general arrangement plans, preliminary stability assumptions, vendor list, and conceptual system diagrams (general ship systems, engine room, and electrical systems), ensuring a clear foundation for project execution.
-
concept design – development of initial design concepts, focusing on innovation, cost optimization, and technical feasibility. This process includes requirement analysis, technical research, and preliminary modeling.
-
technical documents – creation and management of detailed technical documentation, including material specifications, technological procedures, assembly instructions, and compliance reports to meet industry standards.
-
vibration analysis – assessment of structural and mechanical vibrations to improve durability, performance, and operational safety. Identifies potential issues related to resonance, material fatigue, and damping system efficiency.
-
strength analysis – evaluation of material and structural integrity to ensure safety and reliability. Includes load simulations, fatigue testing, and numerical modeling to optimize designed components.
-
class drawings – engineering projects in compliance with classification society regulations and maritime safety standards. Includes structural plans, propulsion systems, onboard equipment, and other required technical specifications.
-
detail design – development of precise engineering solutions, refining conceptual designs into fully manufacturable and functional components, considering geometry, assembly, and material selection.
-
workshop drawings – preparation of detailed production documentation, including bill of materials, guidelines and instructions for workshop.
-
as-built documentation – final records reflecting the completed project, documenting modifications and deviations from original designs, ensuring accuracy for future operation, maintenance and commissionig documentation.

-
contract documentation – preparation of essential documents required for the contract between the shipowner and the shipyard. This includes principal dimensions and technical data, general arrangement plans, preliminary stability assumptions, vendor list, and conceptual system diagrams (general ship systems, engine room, and electrical systems), ensuring a clear foundation for project execution.
-
concept design – development of initial design concepts, focusing on innovation, cost optimization, and technical feasibility. This process includes requirement analysis, technical research, and preliminary modeling.
-
technical documents – creation and management of detailed technical documentation, including material specifications, technological procedures, assembly instructions, and compliance reports to meet industry standards.
-
vibration analysis – assessment of structural and mechanical vibrations to improve durability, performance, and operational safety. Identifies potential issues related to resonance, material fatigue, and damping system efficiency.
-
strength analysis – evaluation of material and structural integrity to ensure safety and reliability. Includes load simulations, fatigue testing, and numerical modeling to optimize designed components.
-
class drawings – engineering projects in compliance with classification society regulations and maritime safety standards. Includes structural plans, propulsion systems, onboard equipment, and other required technical specifications.
-
detail design – development of precise engineering solutions, refining conceptual designs into fully manufacturable and functional components, considering geometry, assembly, and material selection.
-
workshop drawings – preparation of detailed production documentation, including bill of materials, guidelines and instructions for workshop.
-
as-built documentation – final records reflecting the completed project, documenting modifications and deviations from original designs, ensuring accuracy for future operation, maintenance and commissionig documentation.
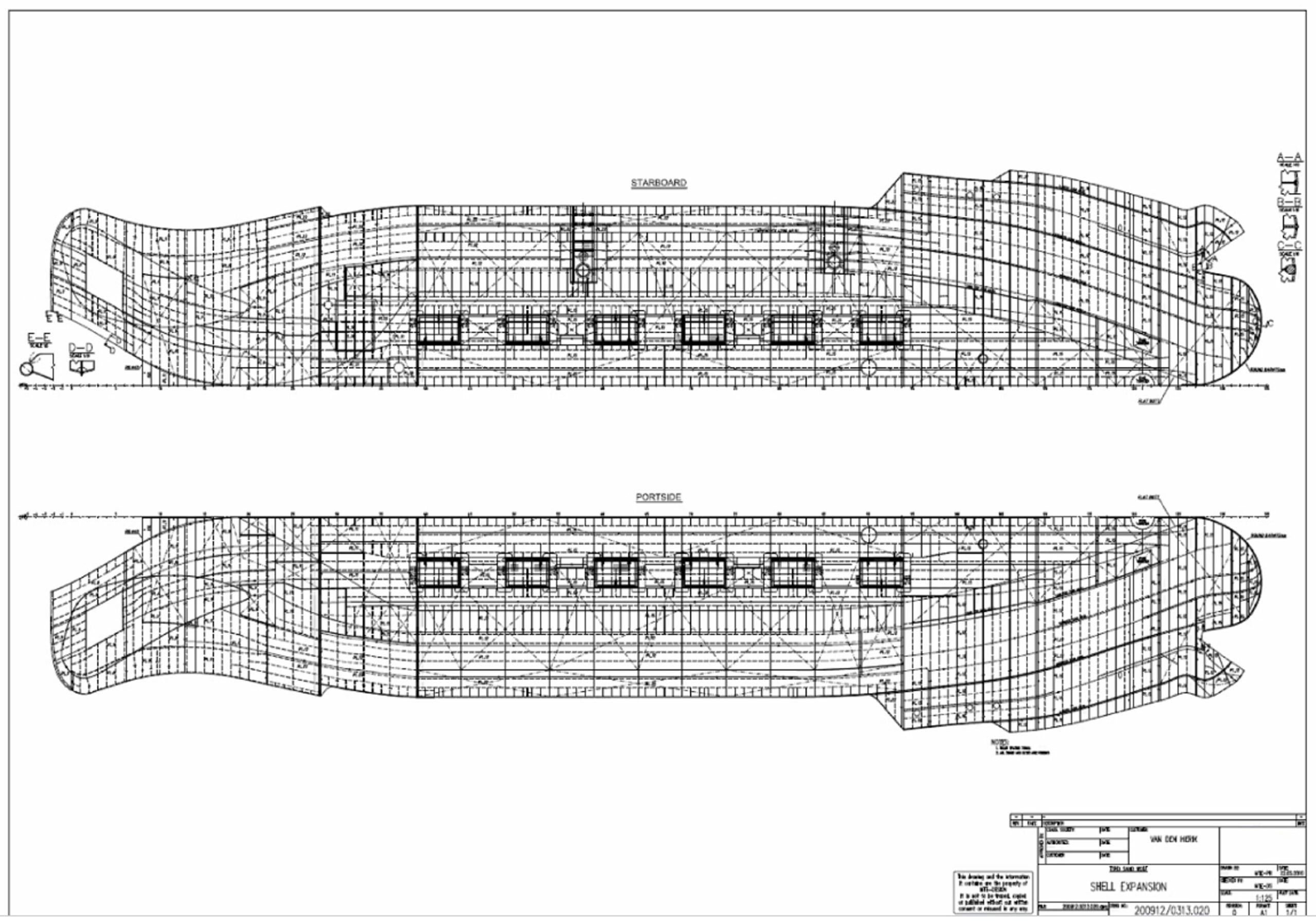
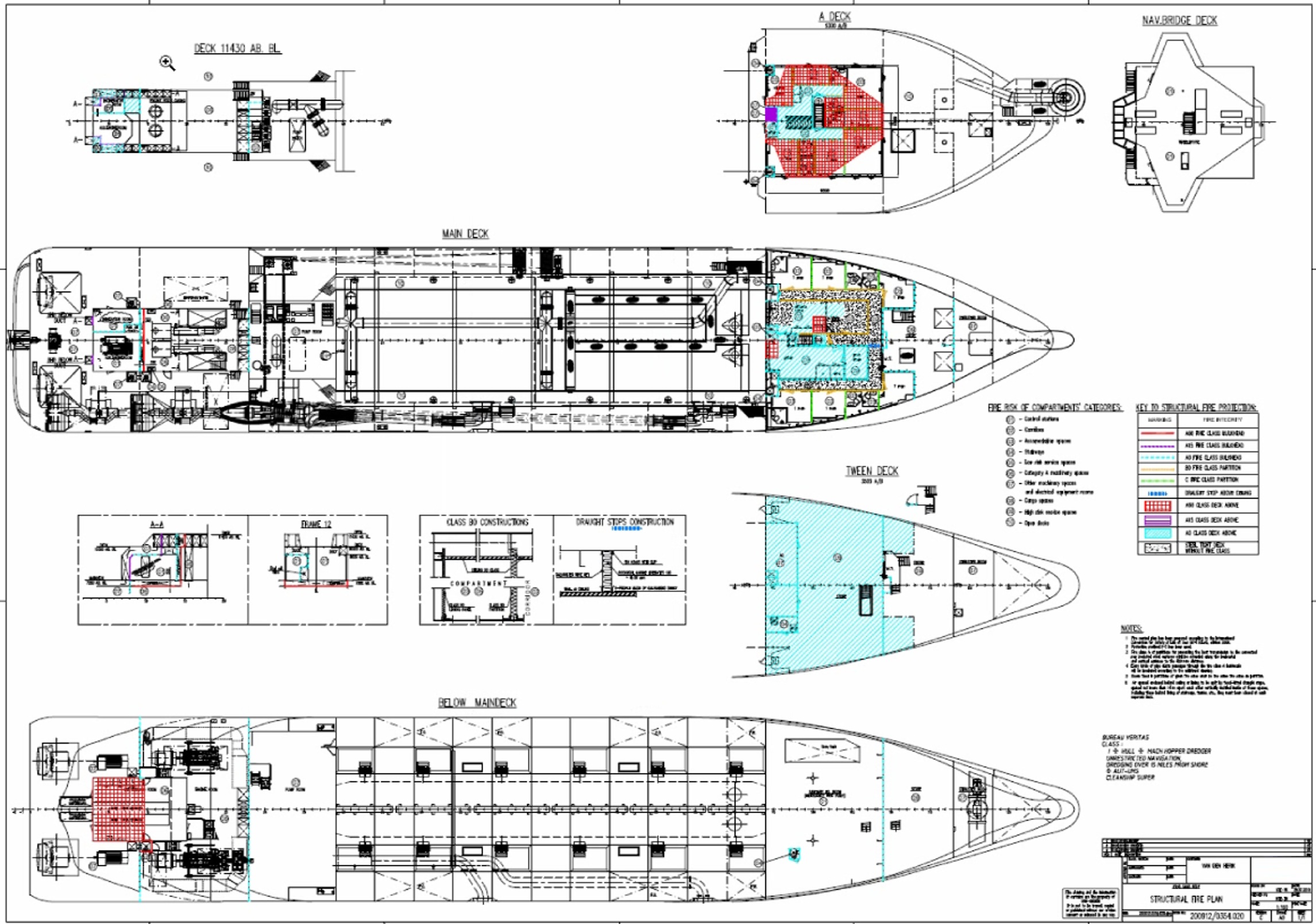
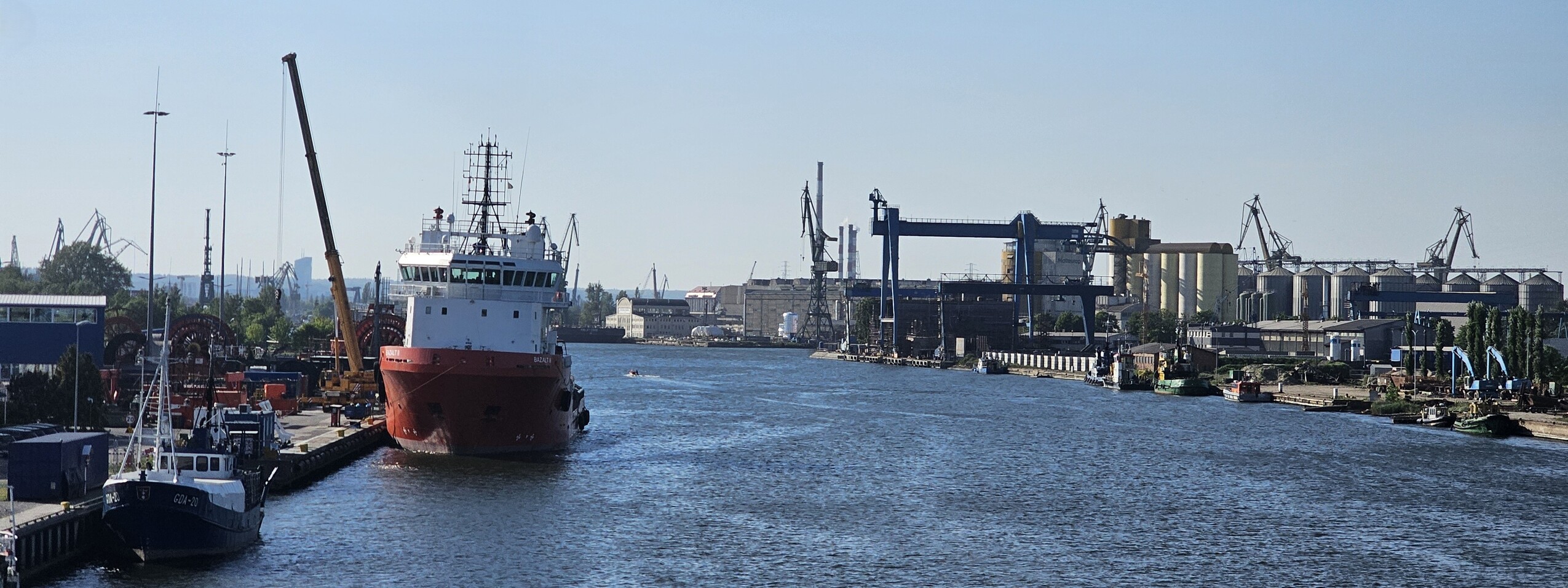
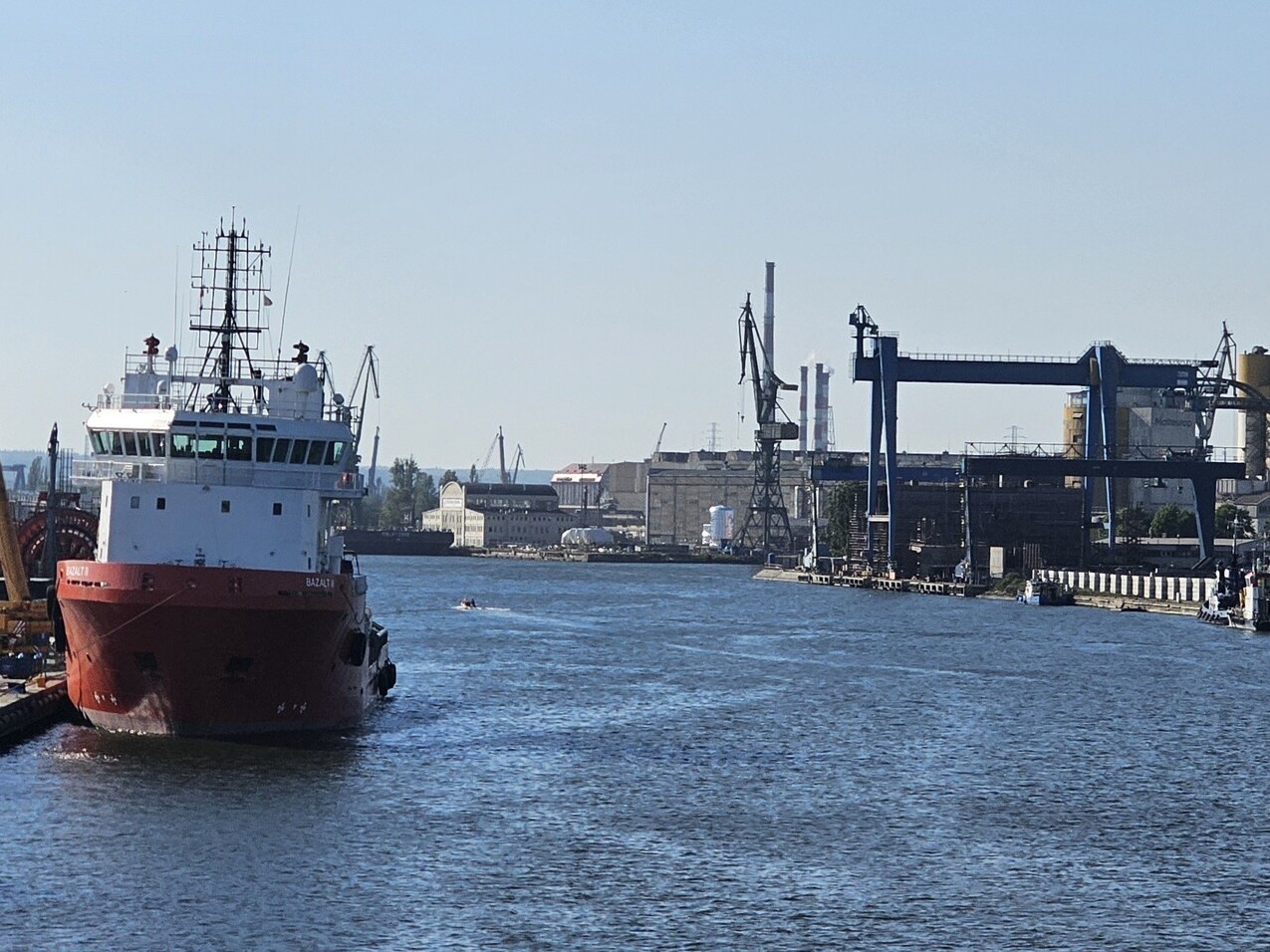
Production
Production encompasses the manufacturing, assembly, and modernization of structural components and onboard systems, ensuring compliance with industry standards and classification requirements. This includes the fabrication of steel structures, installation of piping, HVAC, and electrical systems, as well as the integration of automation and exhaust emission control solutions. Each stage of the process is carried out with a focus on precision, efficiency, and durability to meet the demands of the maritime and industrial sectors.
Advanced prefabrication techniques enable accurate and efficient assembly, while specialized welding and surface treatment technologies provide enhanced strength and protection against environmental factors. The implementation of modern engineering solutions ensures that all systems function reliably, optimizing operational performance and extending service life. Through a combination of high-quality materials and cutting-edge manufacturing techniques, production delivers robust and adaptable solutions tailored to specific project requirements.
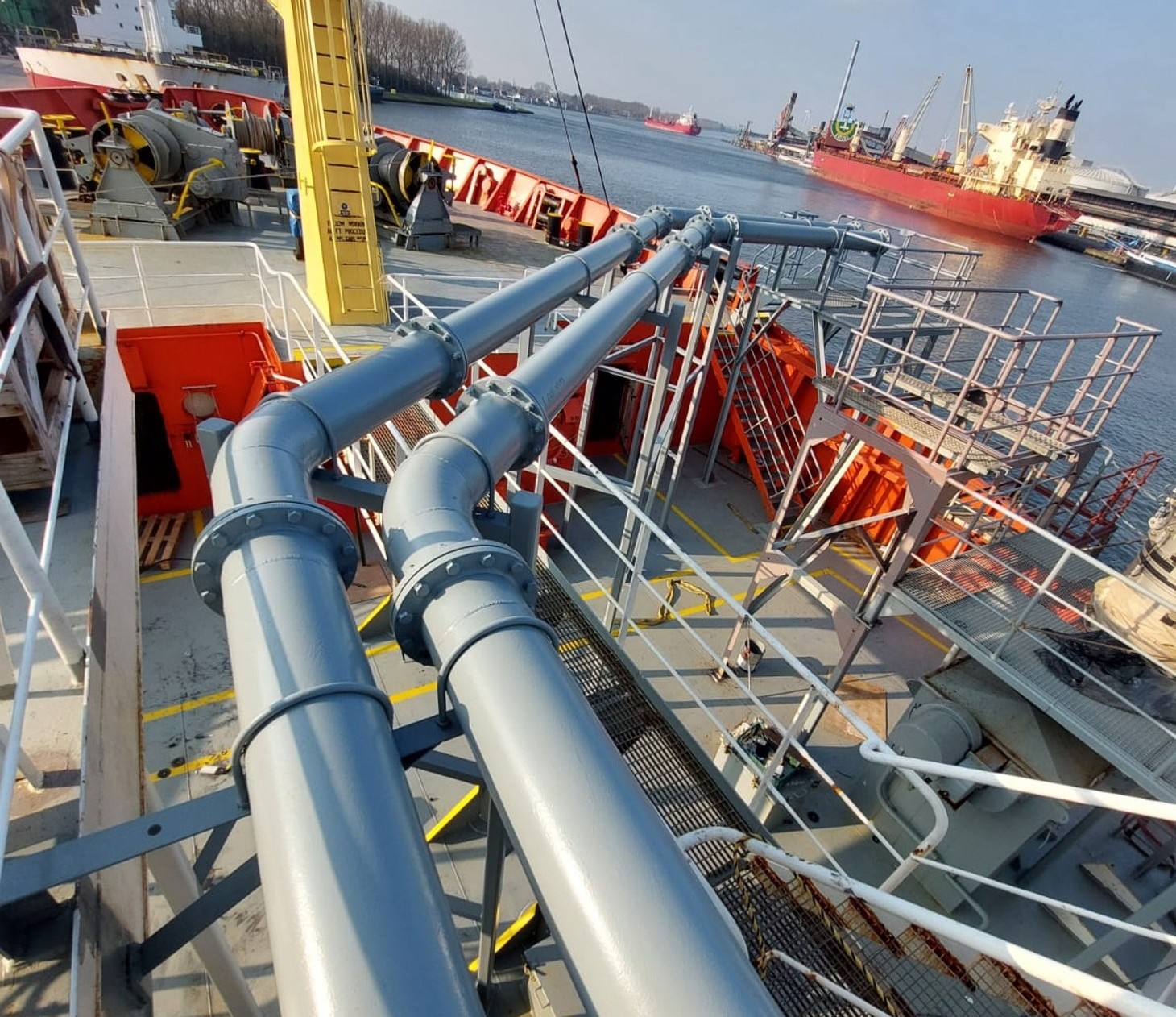
Production
Production encompasses the manufacturing, assembly, and modernization of structural components and onboard systems, ensuring compliance with industry standards and classification requirements. This includes the fabrication of steel structures, installation of piping, HVAC, and electrical systems, as well as the integration of automation and exhaust emission control solutions. Each stage of the process is carried out with a focus on precision, efficiency, and durability to meet the demands of the maritime and industrial sectors.
Advanced prefabrication techniques enable accurate and efficient assembly, while specialized welding and surface treatment technologies provide enhanced strength and protection against environmental factors. The implementation of modern engineering solutions ensures that all systems function reliably, optimizing operational performance and extending service life. Through a combination of high-quality materials and cutting-edge manufacturing techniques, production delivers robust and adaptable solutions tailored to specific project requirements.
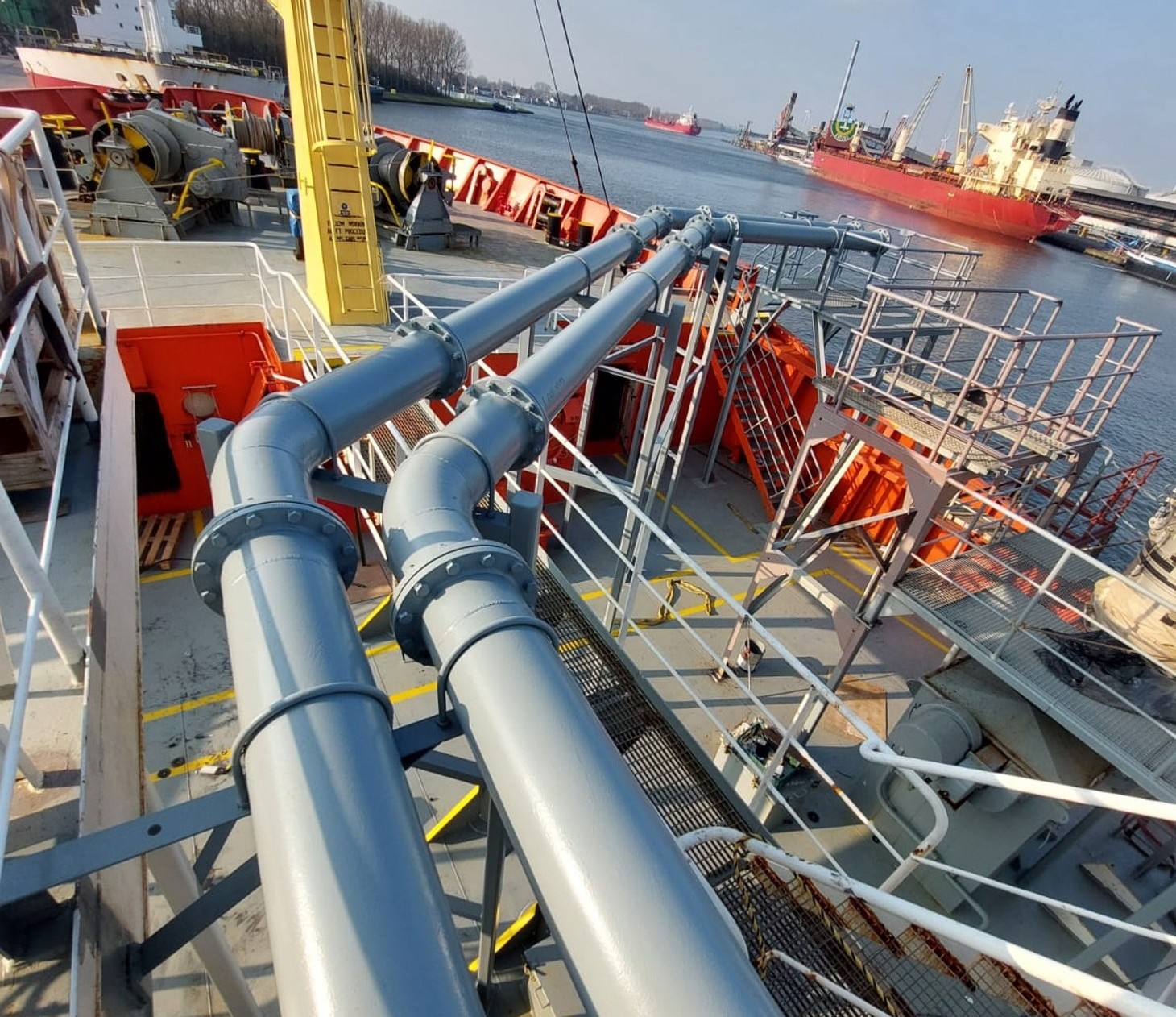
hull and steel structures
• steel structures – fabrication, assembly, and reinforcement of ship hulls, decks, bulkheads, and support frames to ensure durability and compliance with classification standards.
• foundations – structural support for machinery and onboard equipment, designed to absorb vibrations and withstand operational stresses.
outfitting
• ventilation and air release systems – installation of air release mechanisms and ventilation systems to maintain safe and efficient airflow.
• fire protection systems – integration of fire suppression, detection, and prevention solutions to enhance onboard safety.
• insulation works – thermal and acoustic insulation for improved energy efficiency, safety, and comfort.
piping systems
• pipelines – new installations, repairs, and refurbishments – design, assembly, and maintenance of piping networks for fluid and gas transport.
• ballast water treatment systems (BWTS) – implementation of systems for filtering and treating ballast water to meet environmental regulations.
• sea water cooling systems – installation and maintenance of cooling systems utilizing seawater for temperature regulation in onboard machinery.
• hydraulic systems – development and servicing of hydraulic networks for power transmission and mechanical operation.
heating, ventilation, and air conditioning
• HVAC systems – installation and optimization of heating, ventilation, and air conditioning to maintain climate control onboard.
automation and electrical engineering
• electrical systems, including installation repairs – design, installation, and maintenance of onboard electrical infrastructure.
• automation and valve control systems – implementation of automated control solutions for valves, machinery, and process optimization.
exhaust and emission control
• exhaust gas treatment systems (scrubbers) – installation and servicing of scrubbers to reduce emissions and comply with environmental standards.
• exhaust pipe replacement and repair – maintenance and replacement of exhaust piping to ensure optimal performance and longevity.
fabrication and specialized welding
• component prefabrication – precision manufacturing of structural and mechanical components for seamless assembly.
• laser welding – advanced laser welding techniques for high-precision, durable, and efficient joint formation.
surface treatment and protection
• mobile galvanization – on-site galvanization services to protect metal surfaces from corrosion and extend lifespan.
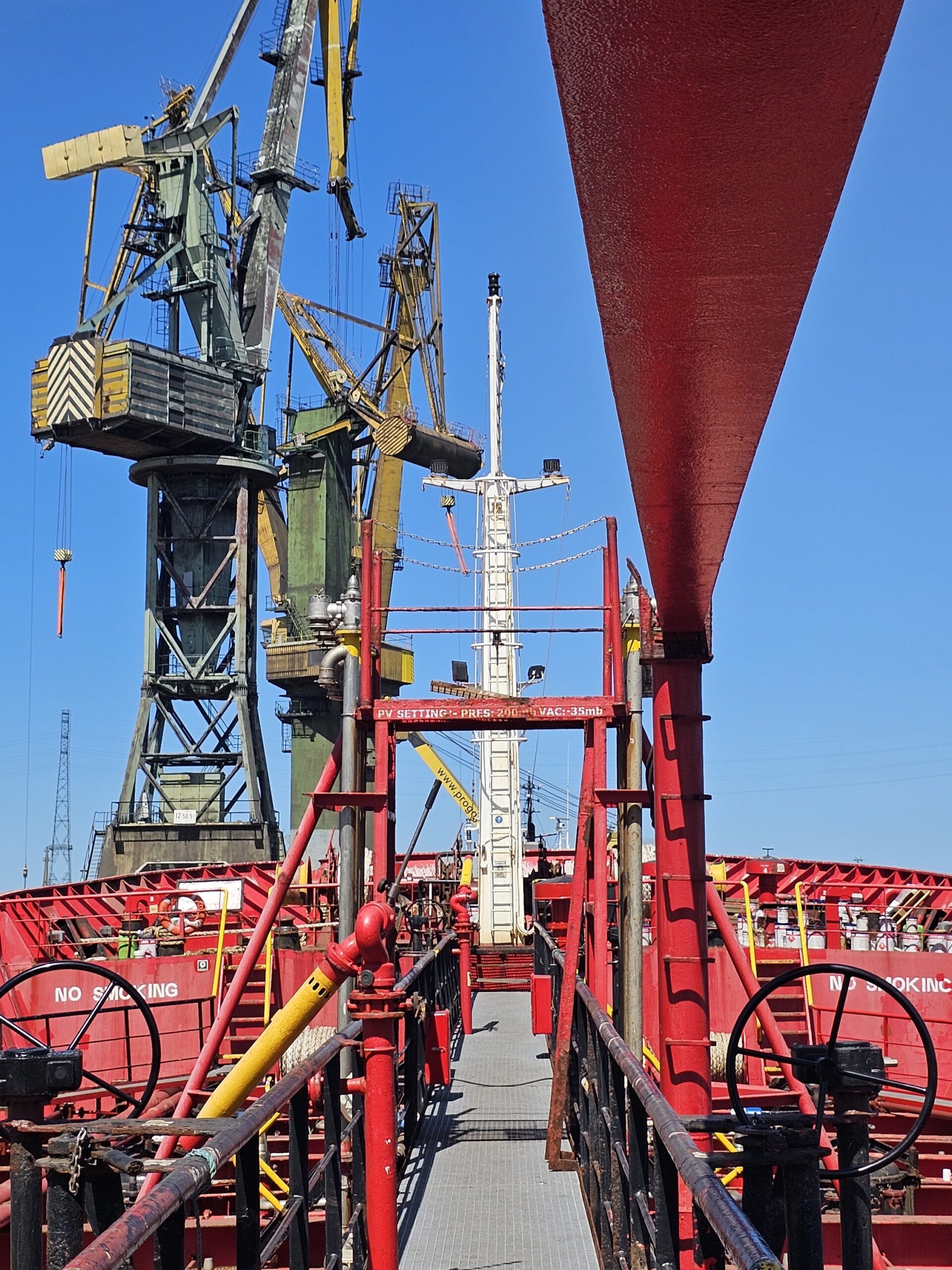
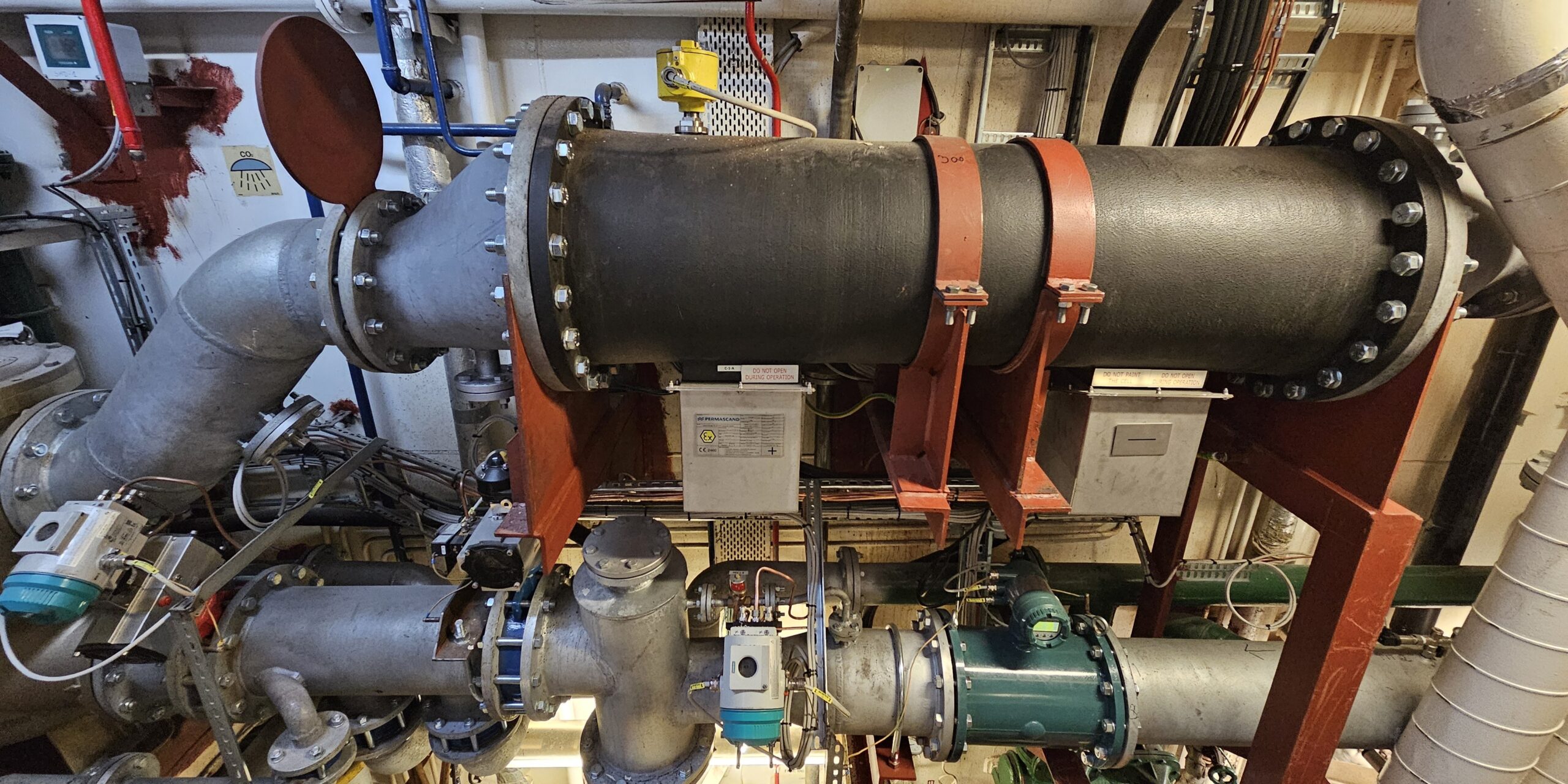
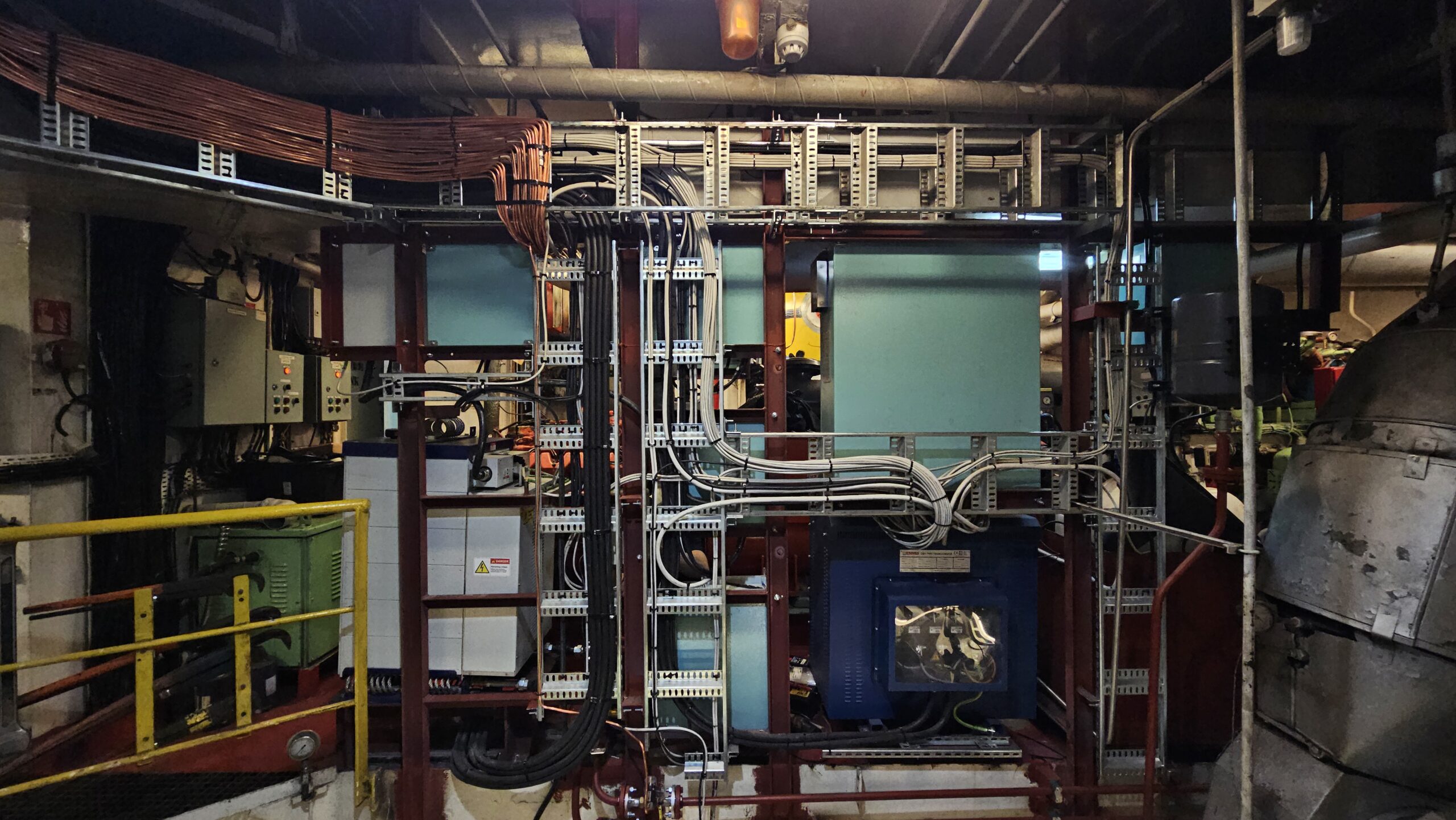
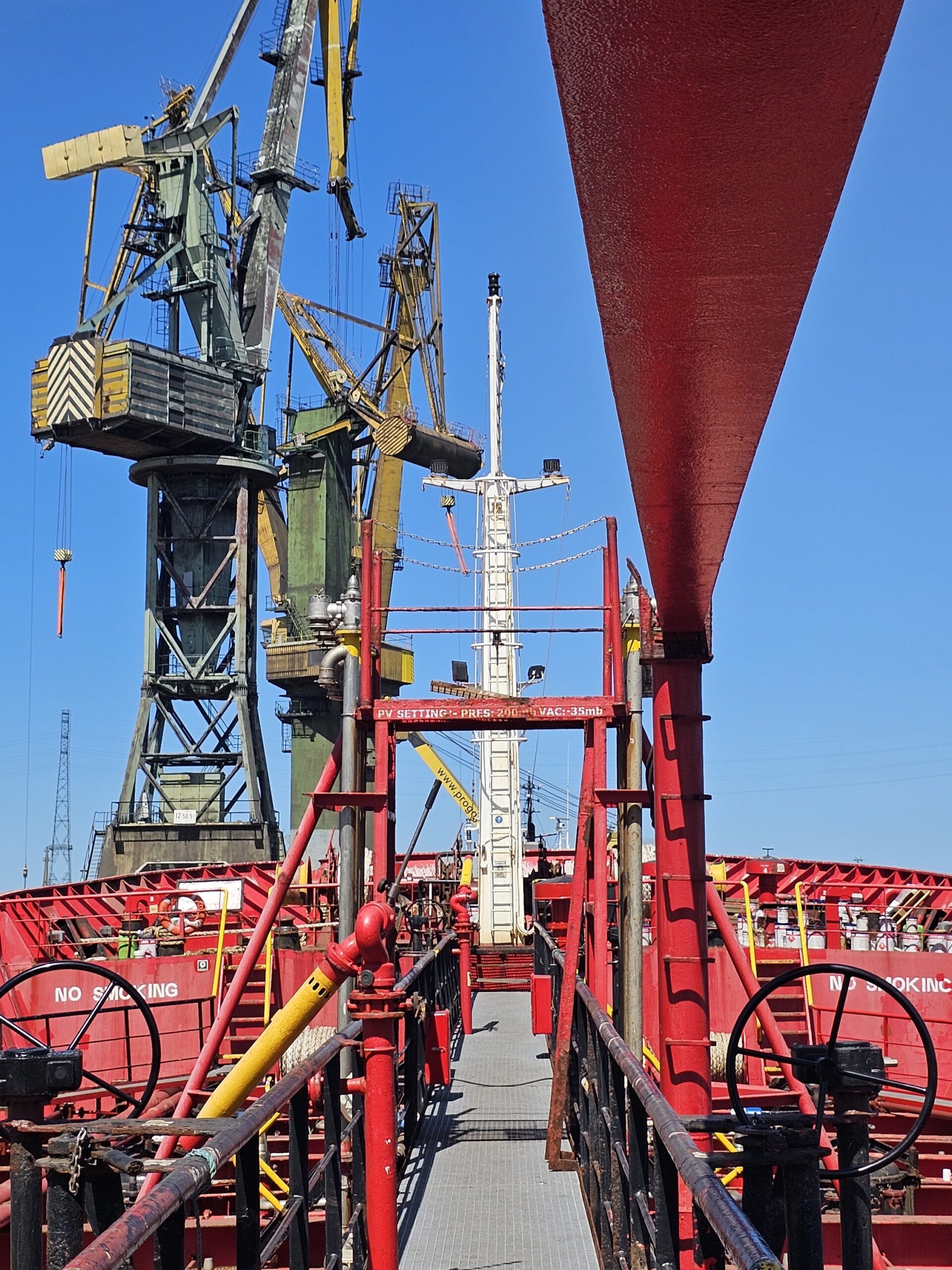
hull and steel structures
• steel structures – fabrication, assembly, and reinforcement of ship hulls, decks, bulkheads, and support frames to ensure durability and compliance with classification standards.
• foundations – structural support for machinery and onboard equipment, designed to absorb vibrations and withstand operational stresses.
outfitting
• ventilation and air release systems – installation of air release mechanisms and ventilation systems to maintain safe and efficient airflow.
• fire protection systems – integration of fire suppression, detection, and prevention solutions to enhance onboard safety.
• insulation works – thermal and acoustic insulation for improved energy efficiency, safety, and comfort.
piping systems
• pipelines – new installations, repairs, and refurbishments – design, assembly, and maintenance of piping networks for fluid and gas transport.
• ballast water treatment systems (BWTS) – implementation of systems for filtering and treating ballast water to meet environmental regulations.
• sea water cooling systems – installation and maintenance of cooling systems utilizing seawater for temperature regulation in onboard machinery.
• hydraulic systems – development and servicing of hydraulic networks for power transmission and mechanical operation.
heating, ventilation, and air conditioning
• HVAC systems – installation and optimization of heating, ventilation, and air conditioning to maintain climate control onboard.
automation and electrical engineering
• electrical systems, including installation repairs – design, installation, and maintenance of onboard electrical infrastructure.
• automation and valve control systems – implementation of automated control solutions for valves, machinery, and process optimization.
exhaust and emission control
• exhaust gas treatment systems (scrubbers) – installation and servicing of scrubbers to reduce emissions and comply with environmental standards.
• exhaust pipe replacement and repair – maintenance and replacement of exhaust piping to ensure optimal performance and longevity.
fabrication and specialized welding
• component prefabrication – precision manufacturing of structural and mechanical components for seamless assembly.
• laser welding – advanced laser welding techniques for high-precision, durable, and efficient joint formation.
surface treatment and protection
• mobile galvanization – on-site galvanization services to protect metal surfaces from corrosion and extend lifespan.
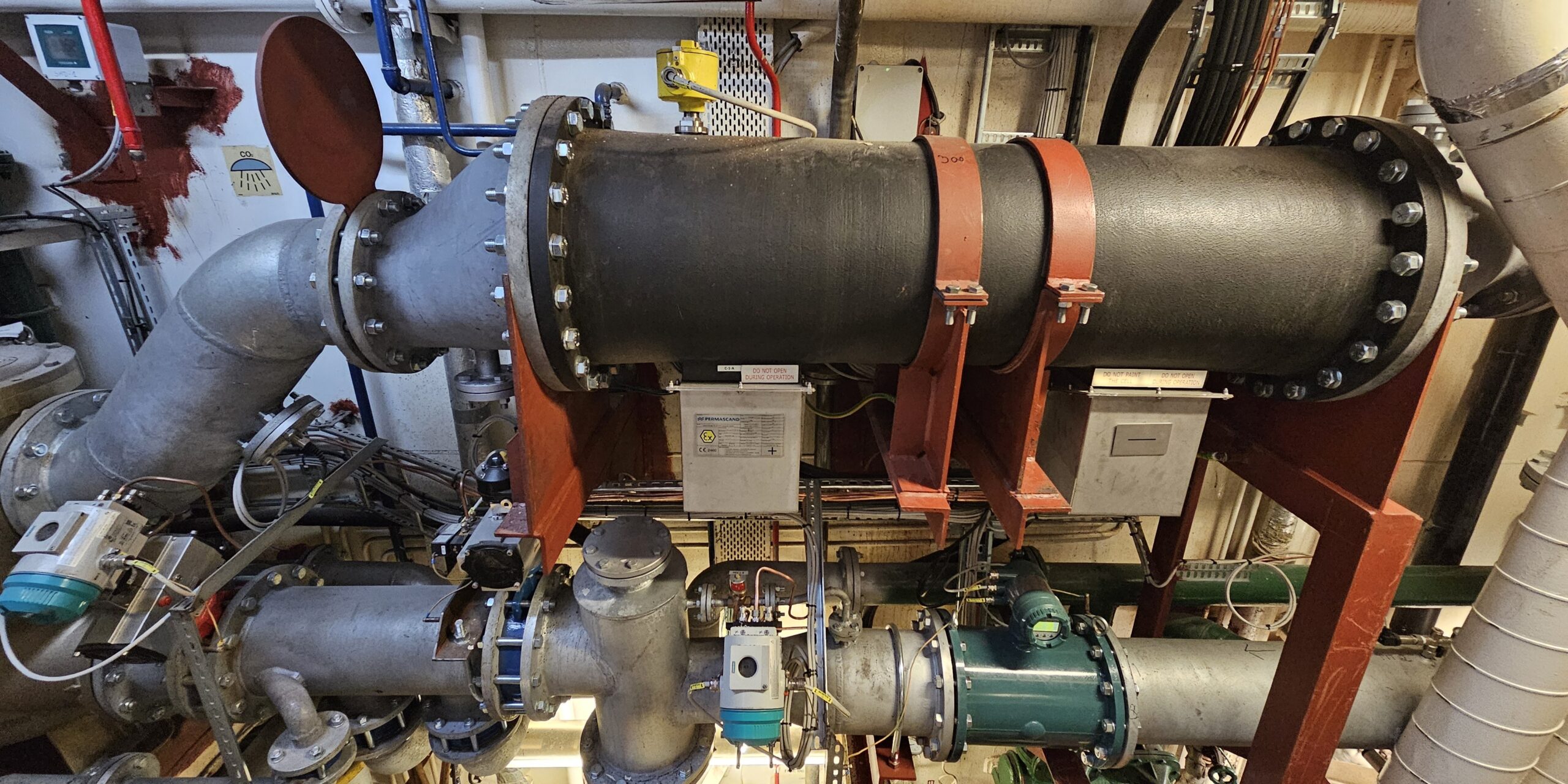
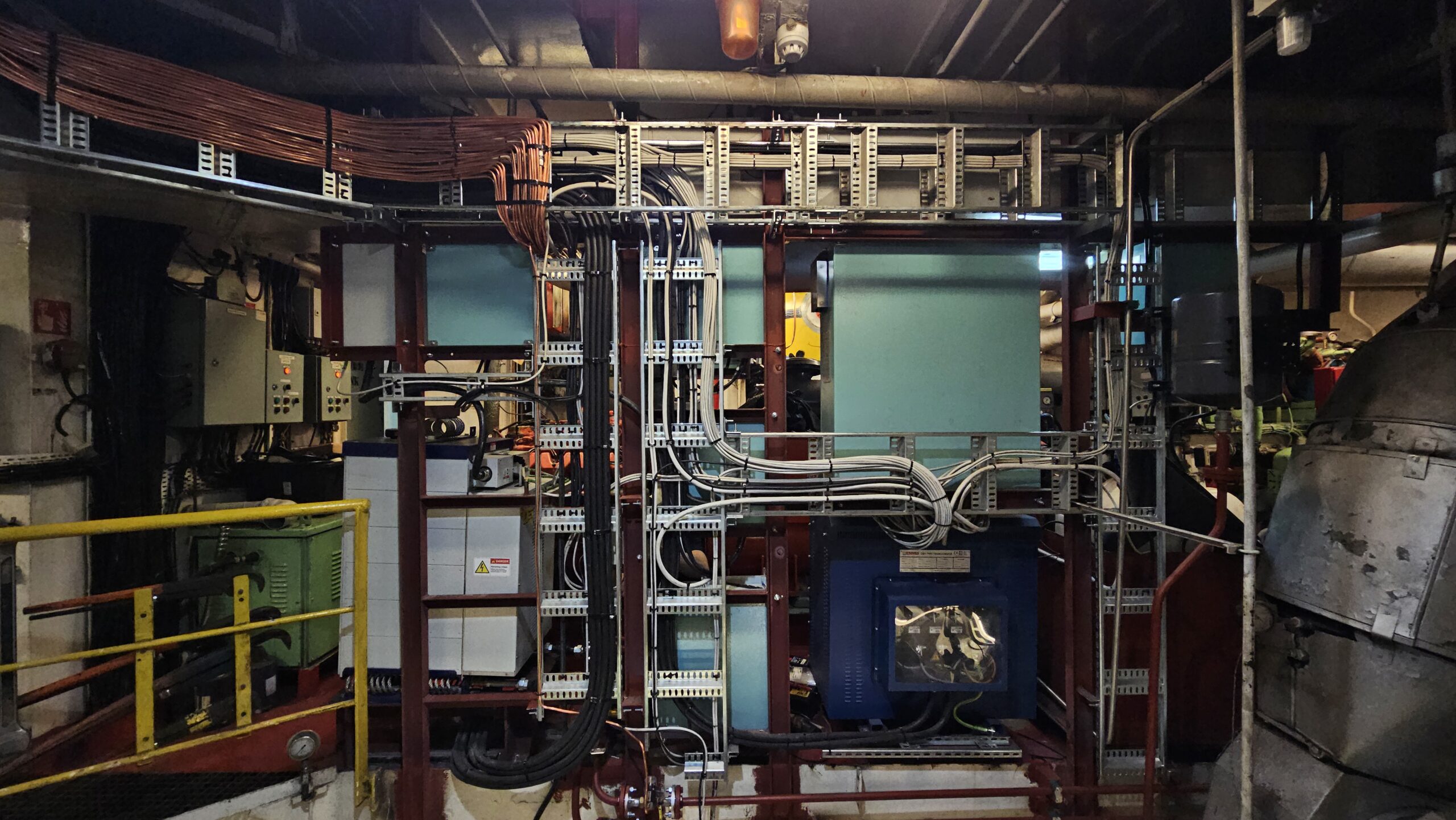
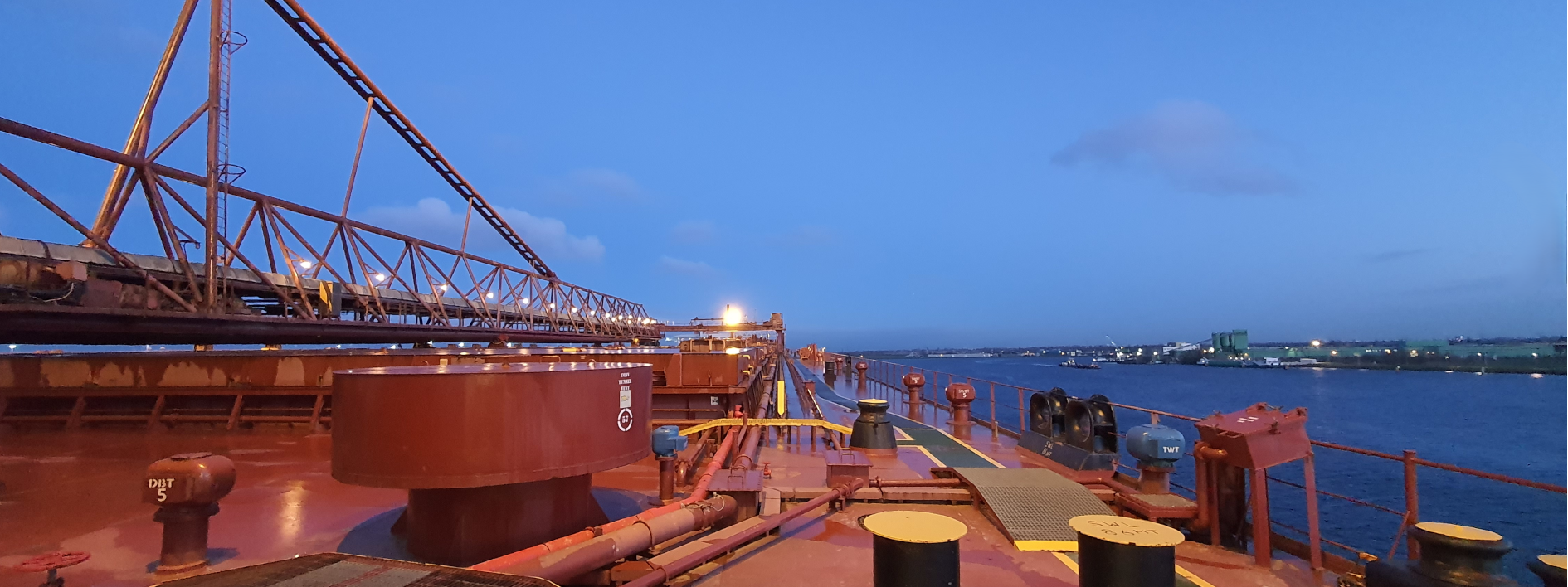
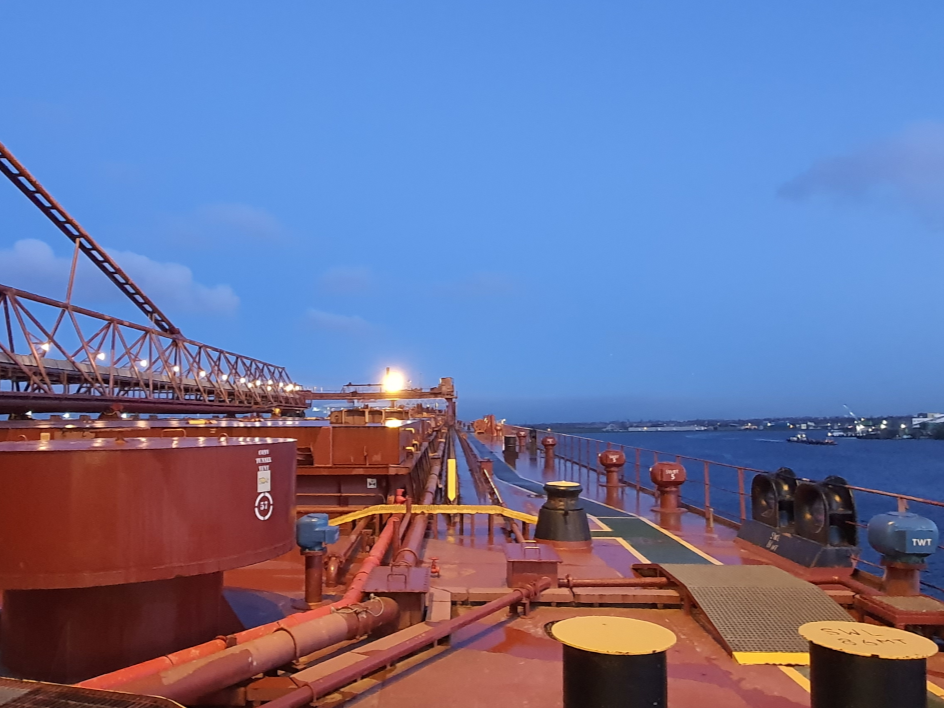