SCRUBBERS
conical reaction chamber section replacement
SCRUBBERS
conical reaction chamber section replacement
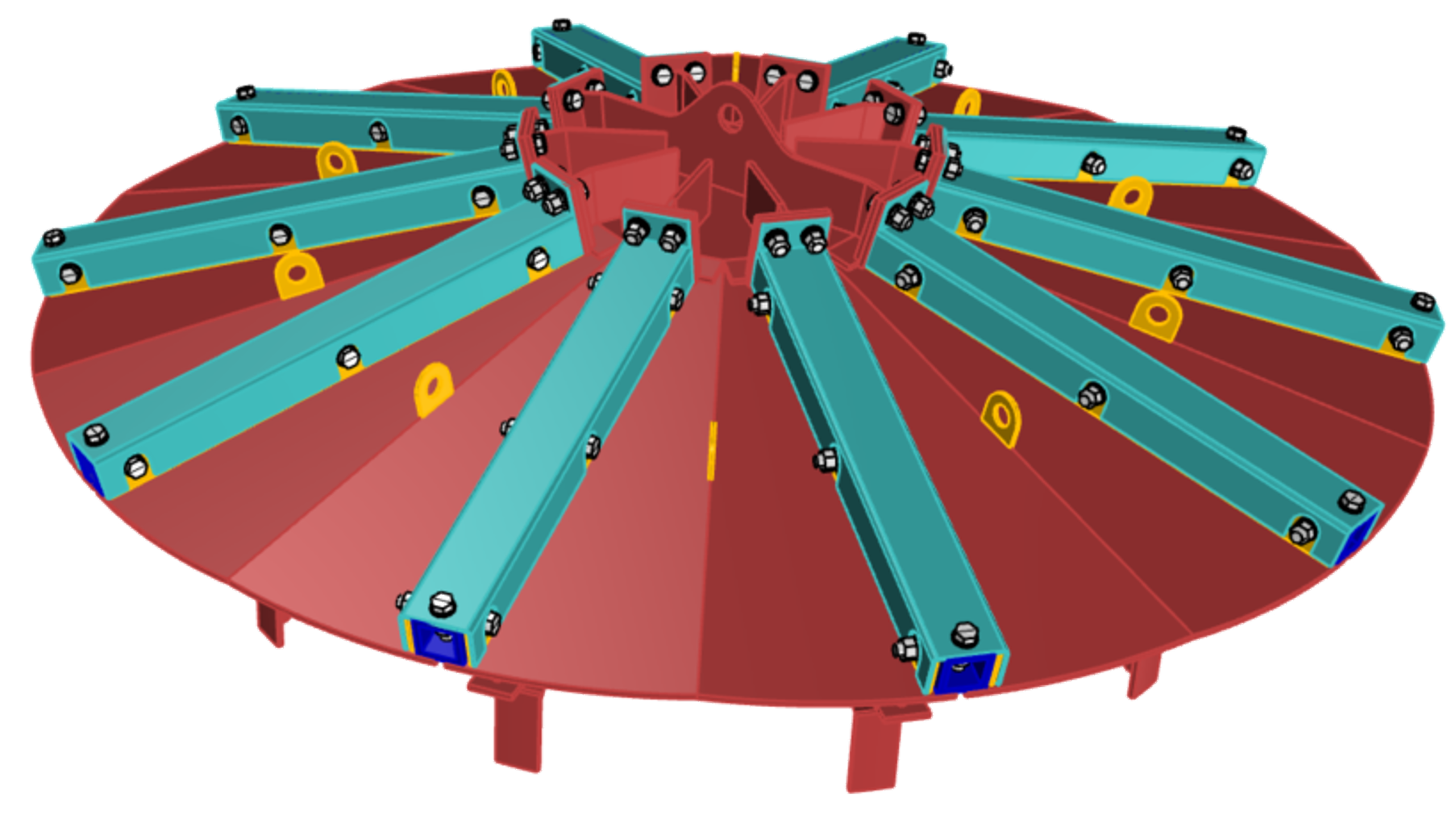
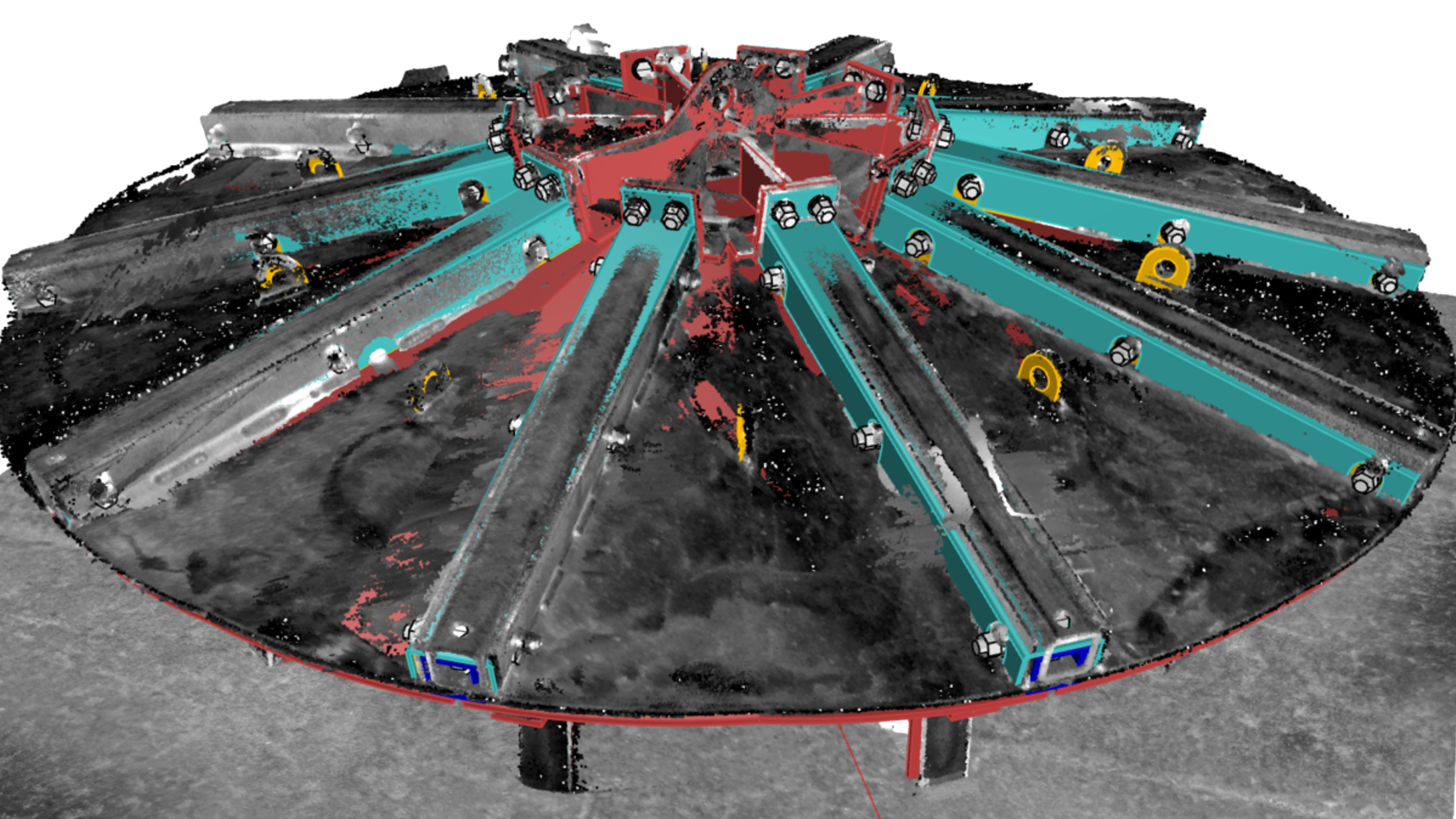
A scrubber on ships is a device used to clean exhaust gases to reduce sulfur oxide (SOx) emissions, in compliance with IMO 2020 regulations, which limit the sulfur content in marine fuel to 0.5%. It works by washing the exhaust gases with seawater (in open-loop systems) or with freshwater mixed with chemicals (in closed-loop systems). There are also hybrid versions that can operate in both modes, depending on local regulations and environmental conditions.
Scrubbers allow shipowners to continue using cheaper high-sulfur fuel oil (HSFO), resulting in significant operational cost savings while meeting environmental requirements without switching to more expensive low-sulfur fuel oil (LSFO). In open-loop systems, the cleaned water is discharged back into the sea, while in closed-loop systems, the liquid circulates in a closed loop, minimizing discharge into the environment and requiring appropriate waste storage infrastructure.
Scrubbers have become a popular solution among shipowners, enabling compliance with emission regulations while optimizing operational costs. This technology is widely used worldwide, supporting the maritime industry’s transition towards more environmentally friendly solutions.
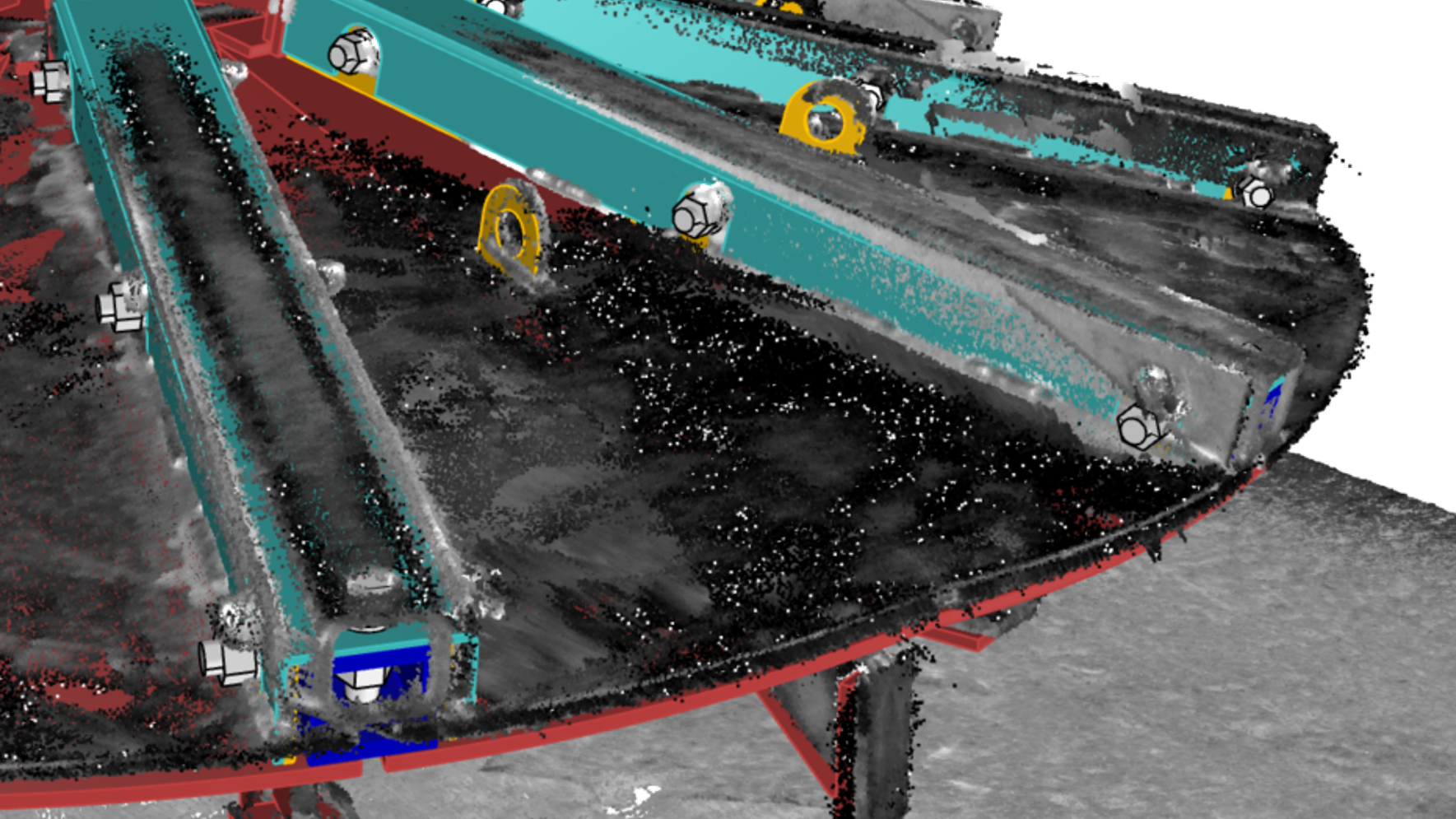
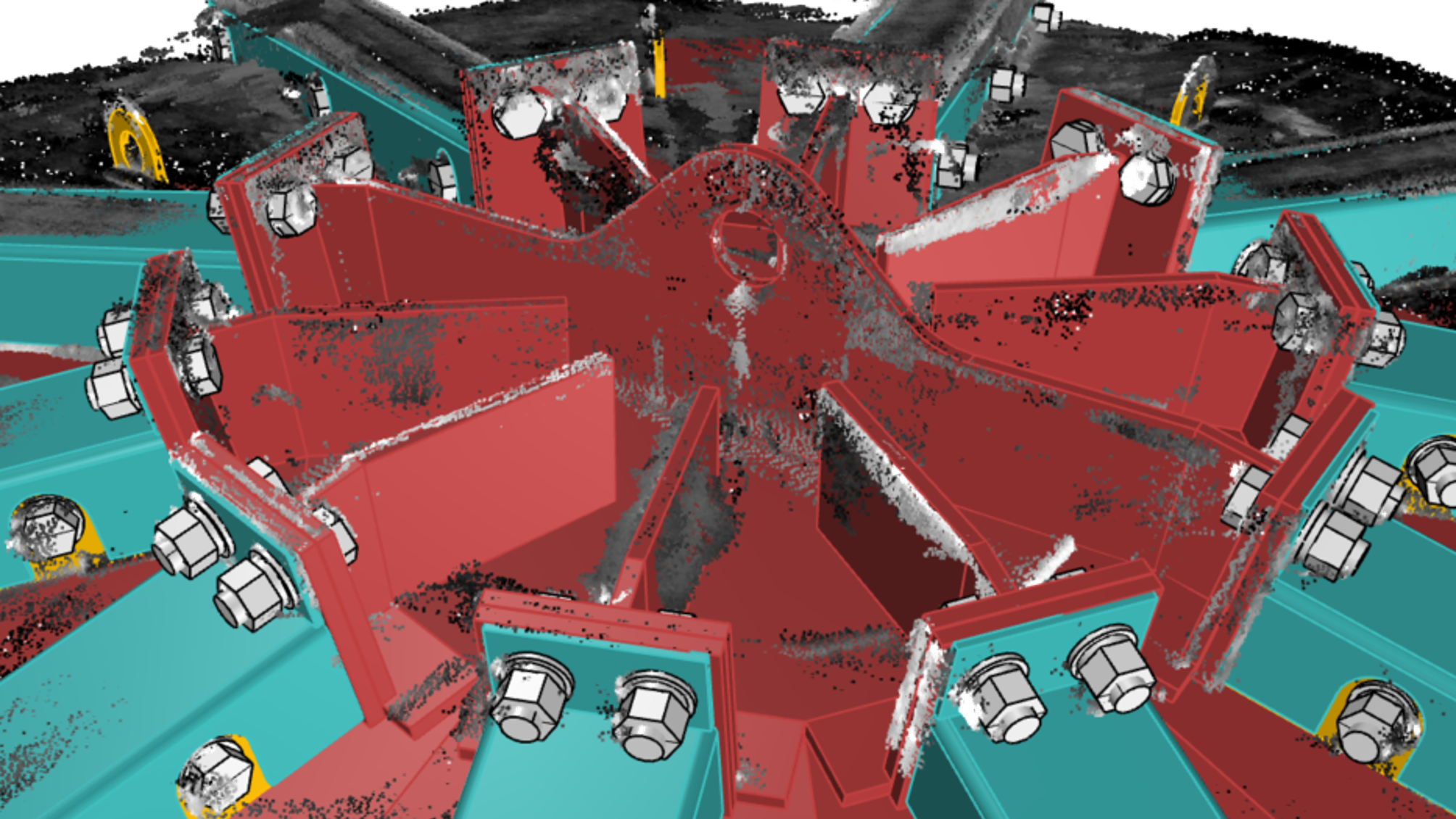
As part of the project related to the Conical Reaction Chamber Section on the scrubber, we carried out a comprehensive process to replace the damaged component, covering several key stages.
In the first phase, we conducted a detailed inspection of the damaged component using advanced 3D scanning technology. This allowed for a precise assessment of the technical condition and the collection of necessary data to develop a new design. Based on the scanning results, we prepared a complete replacement design and full technical documentation, ensuring high accuracy and compliance with the construction and operational requirements of the scrubber.
The next step involved prefabrication of the new component in the production hall. We used modern technologies and materials with high resistance to aggressive gases and operational conditions within the scrubber’s reaction chamber. The prefabrication process proceeded according to schedule and quality standards, guaranteeing the durability and strength of the new component.
After completing the prefabrication, we proceeded with the preparation for the component replacement on the ship. This included detailed logistical planning, coordination of the installation team’s activities, and ensuring the necessary technical resources and safety measures. The replacement process was carried out efficiently with minimal operational downtime for the vessel.
The final stage was the installation of the new Conical Reaction Chamber Section on the scrubber onboard the ship. Due to prior preparation and precision in prefabrication, the installation was completed without disruptions. Functional tests were conducted, confirming full operational efficiency and compliance with technical requirements.
The project was successfully completed, enhancing the scrubber’s operational efficiency while increasing its durability and reliability.
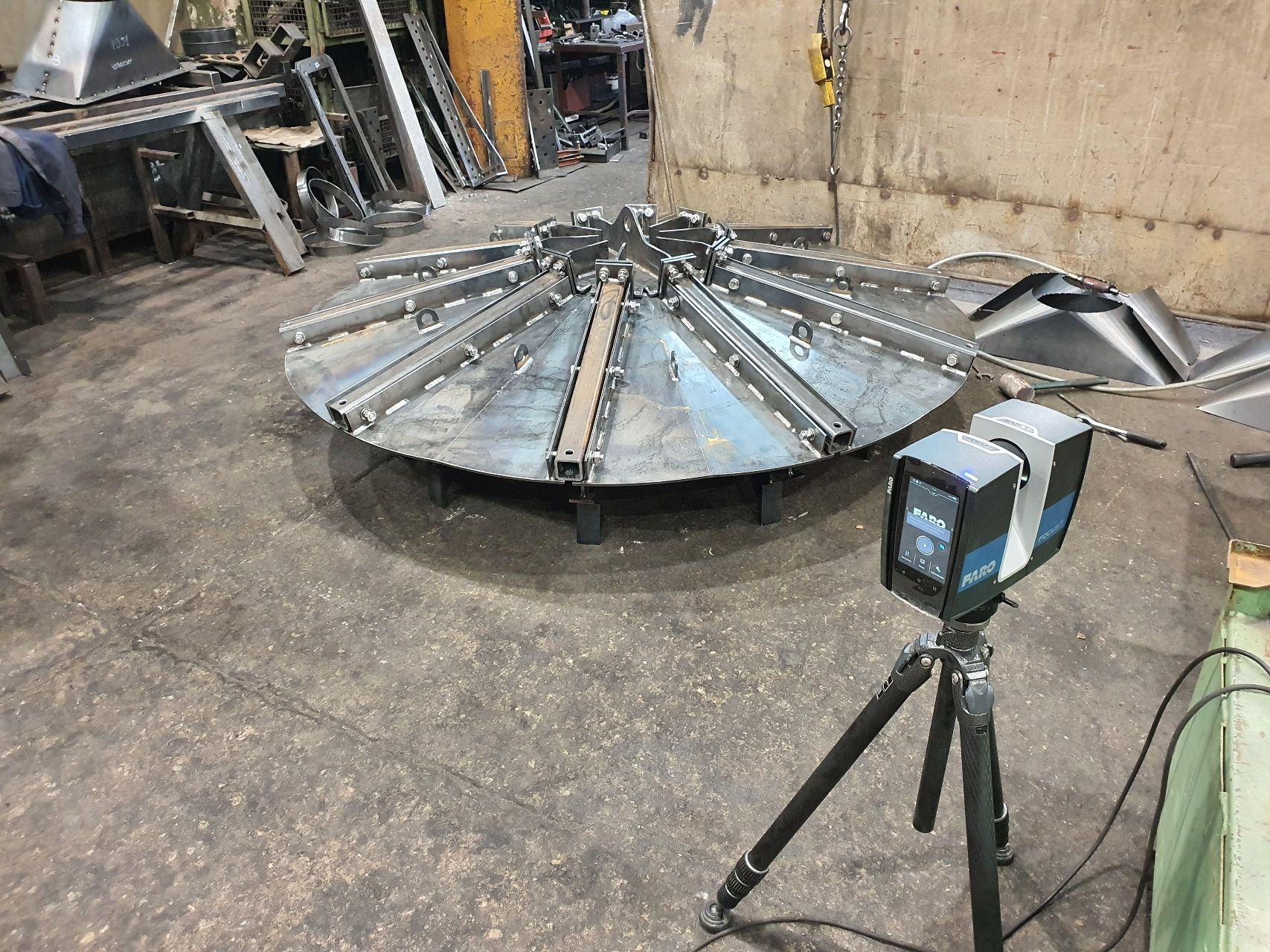
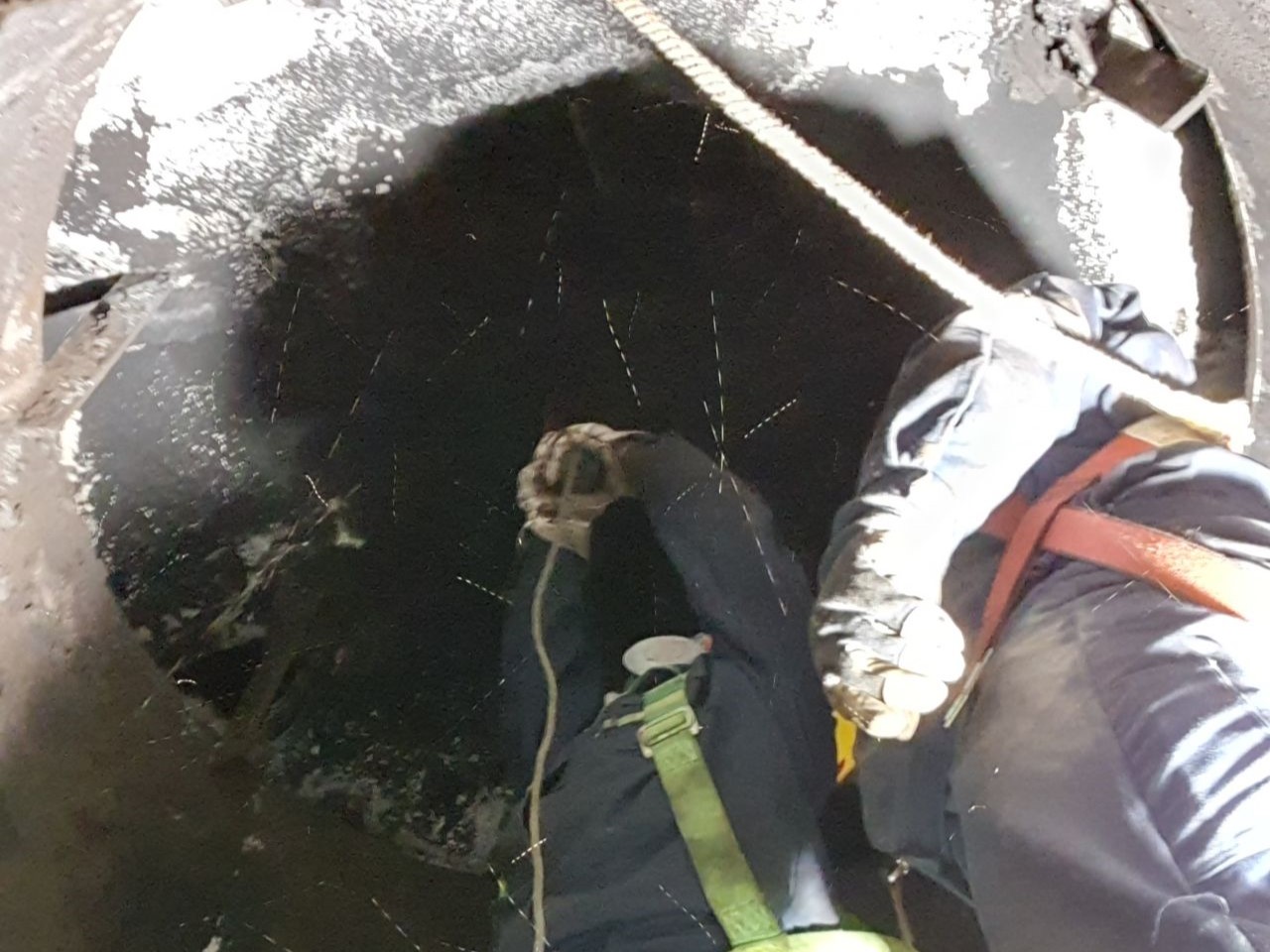
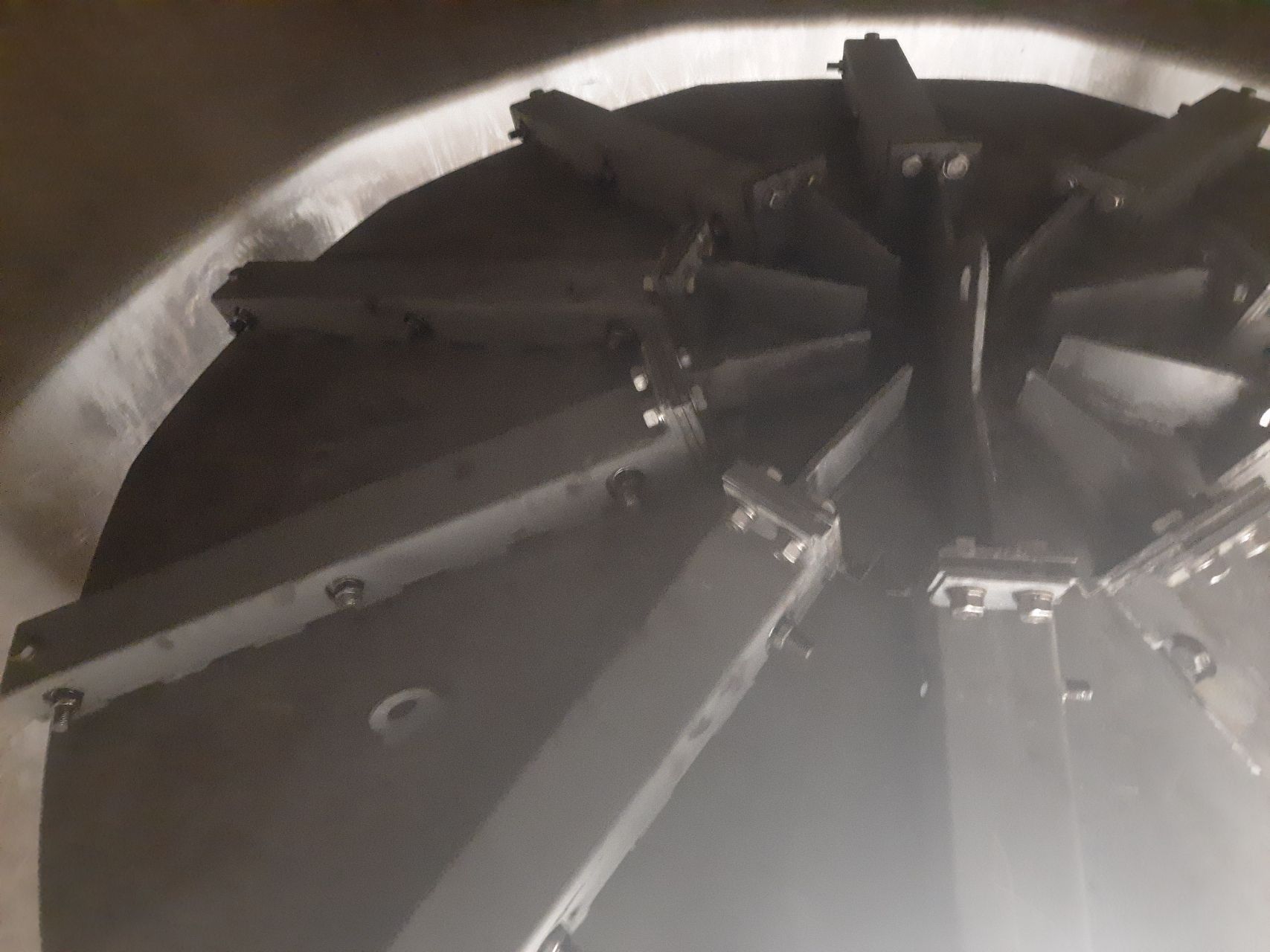
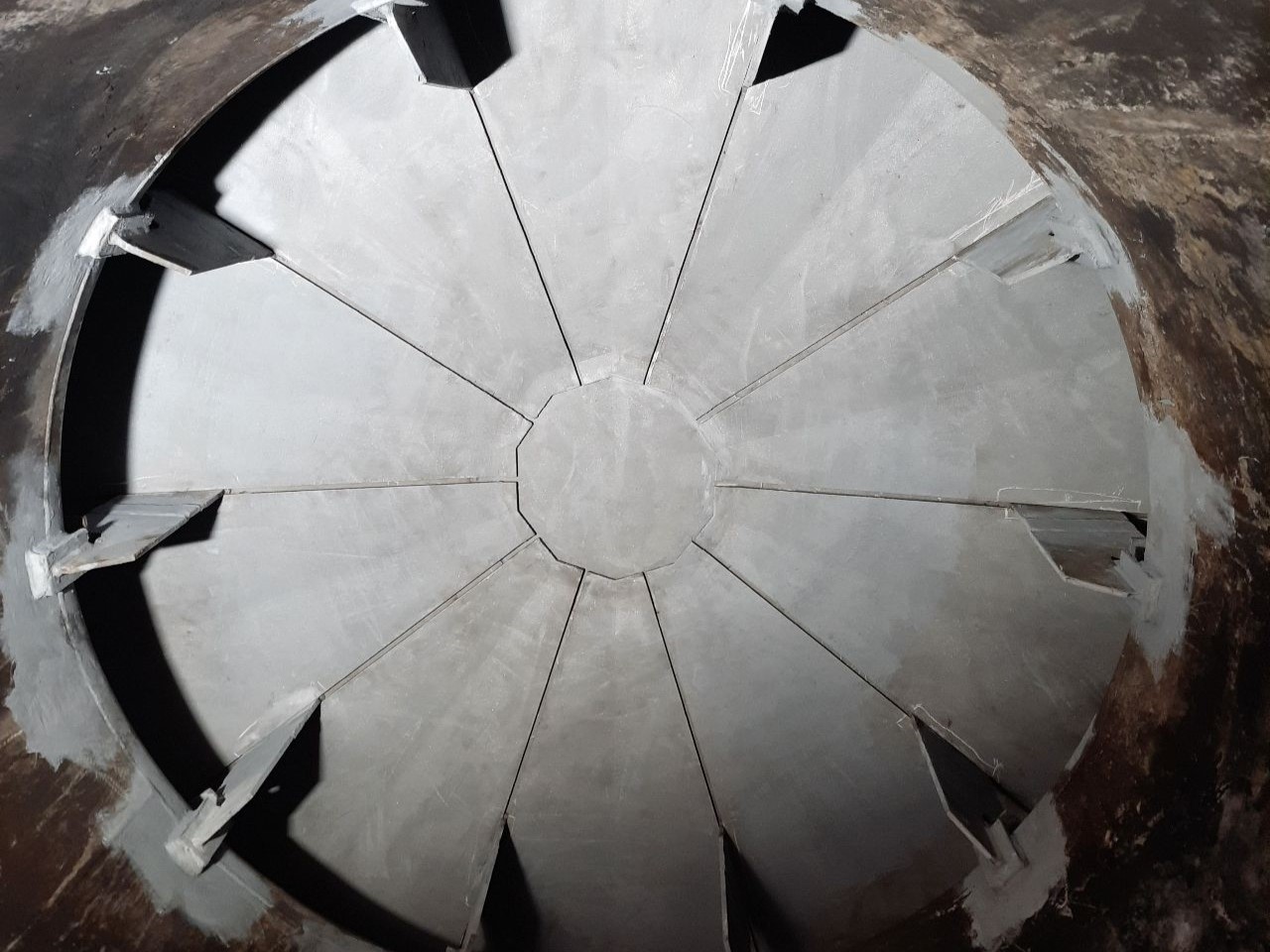
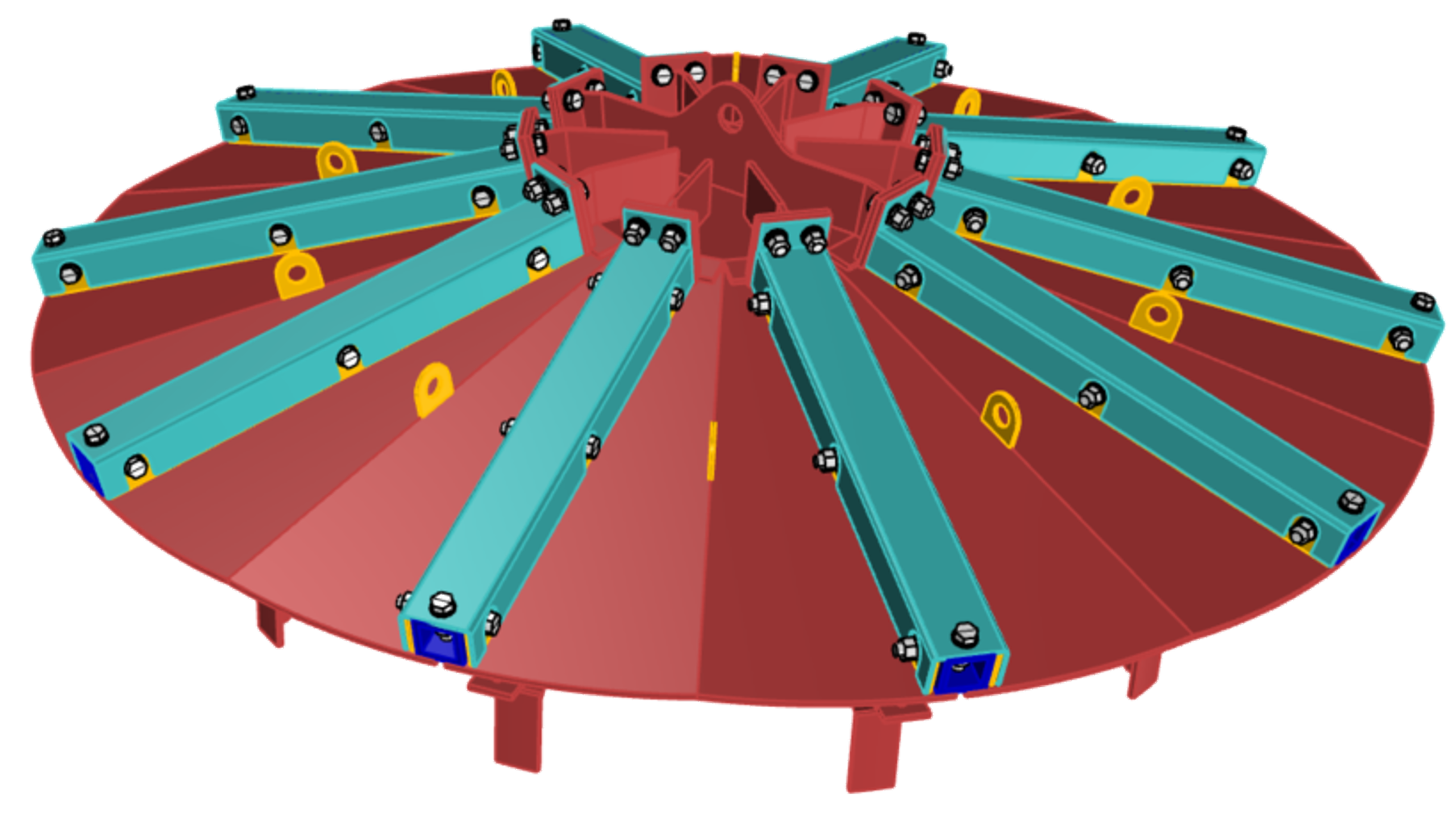
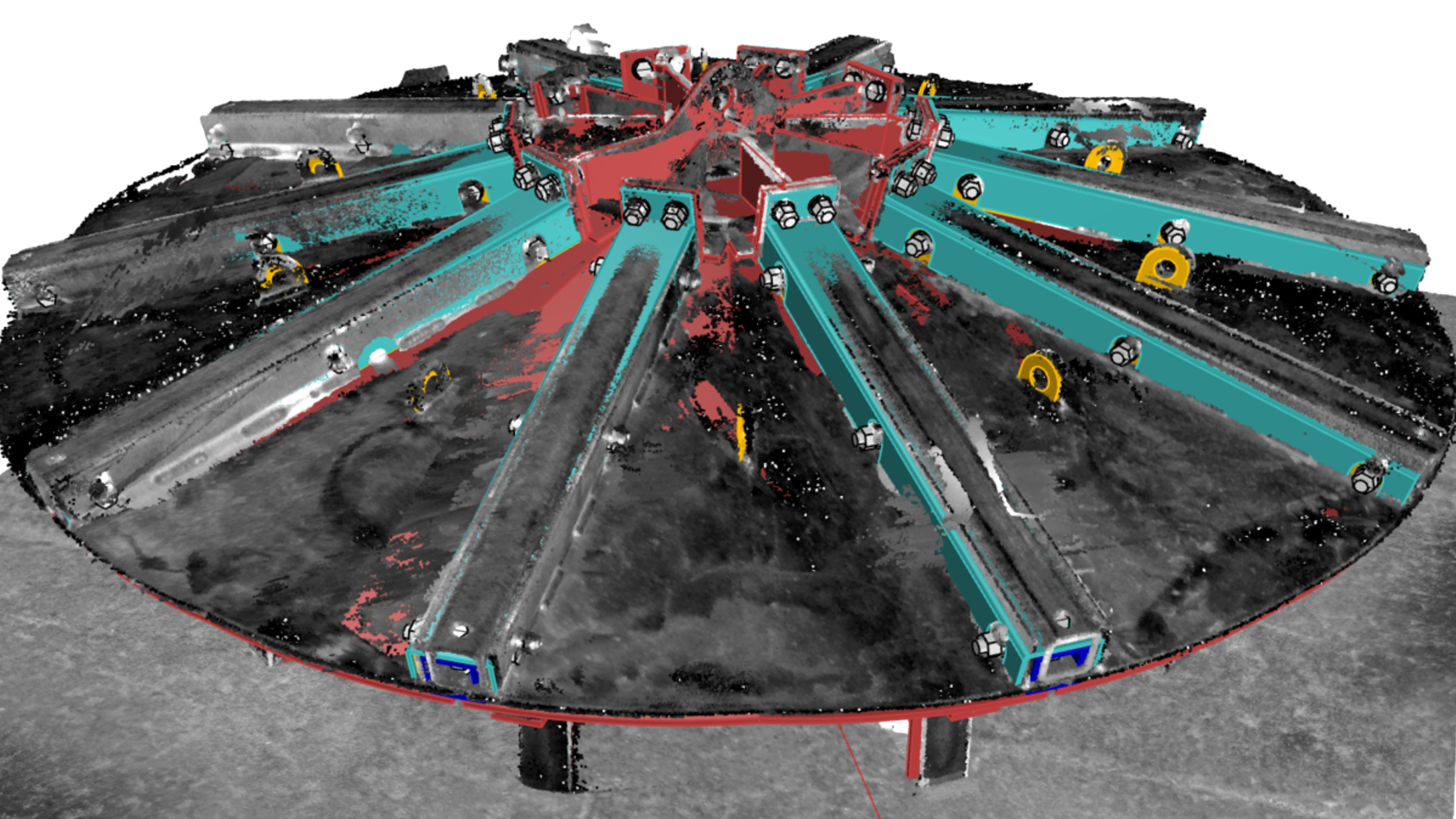
A scrubber on ships is a device used to clean exhaust gases to reduce sulfur oxide (SOx) emissions, in compliance with IMO 2020 regulations, which limit the sulfur content in marine fuel to 0.5%. It works by washing the exhaust gases with seawater (in open-loop systems) or with freshwater mixed with chemicals (in closed-loop systems). There are also hybrid versions that can operate in both modes, depending on local regulations and environmental conditions.
Scrubbers allow shipowners to continue using cheaper high-sulfur fuel oil (HSFO), resulting in significant operational cost savings while meeting environmental requirements without switching to more expensive low-sulfur fuel oil (LSFO). In open-loop systems, the cleaned water is discharged back into the sea, while in closed-loop systems, the liquid circulates in a closed loop, minimizing discharge into the environment and requiring appropriate waste storage infrastructure.
Scrubbers have become a popular solution among shipowners, enabling compliance with emission regulations while optimizing operational costs. This technology is widely used worldwide, supporting the maritime industry’s transition towards more environmentally friendly solutions.
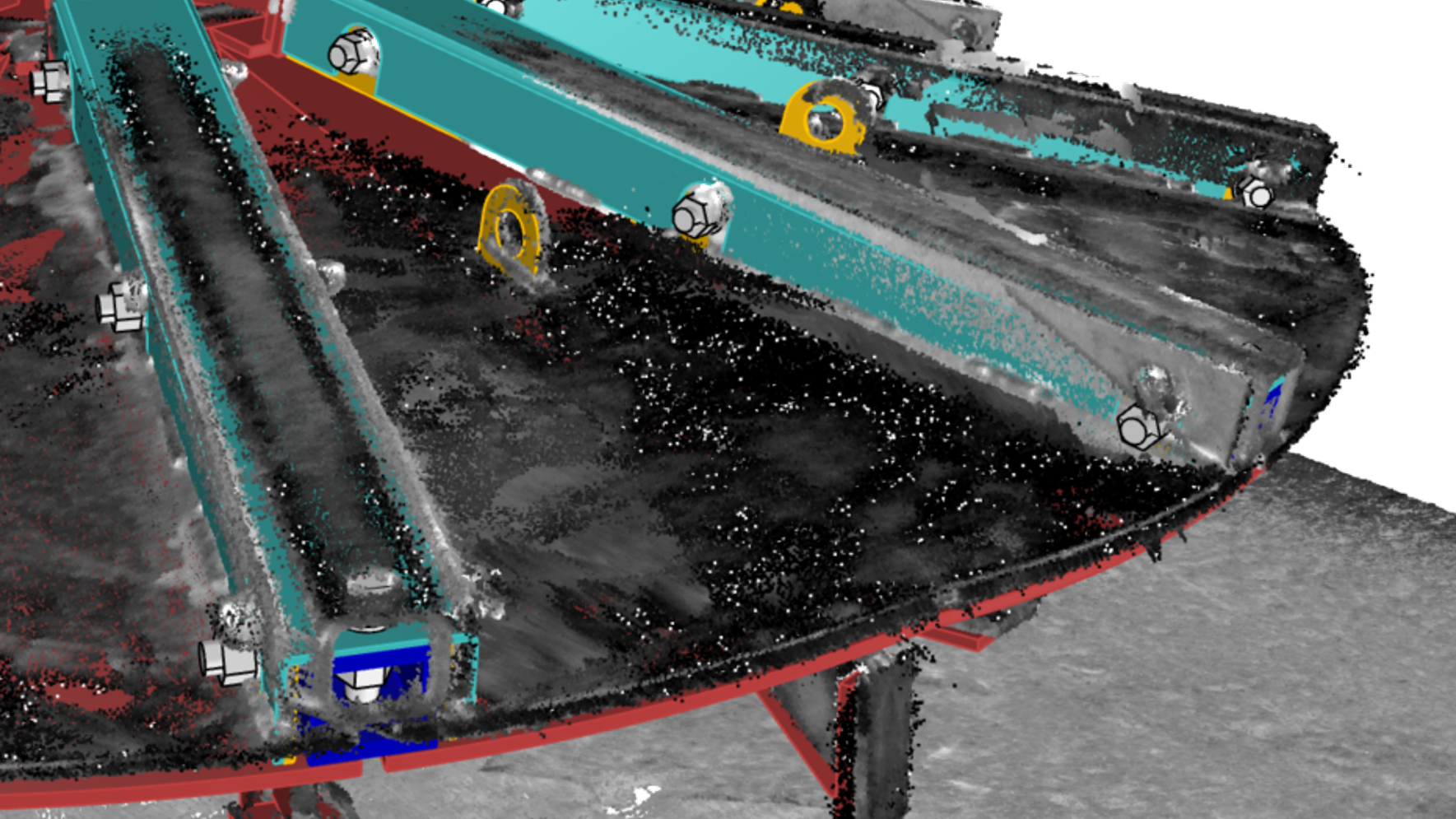
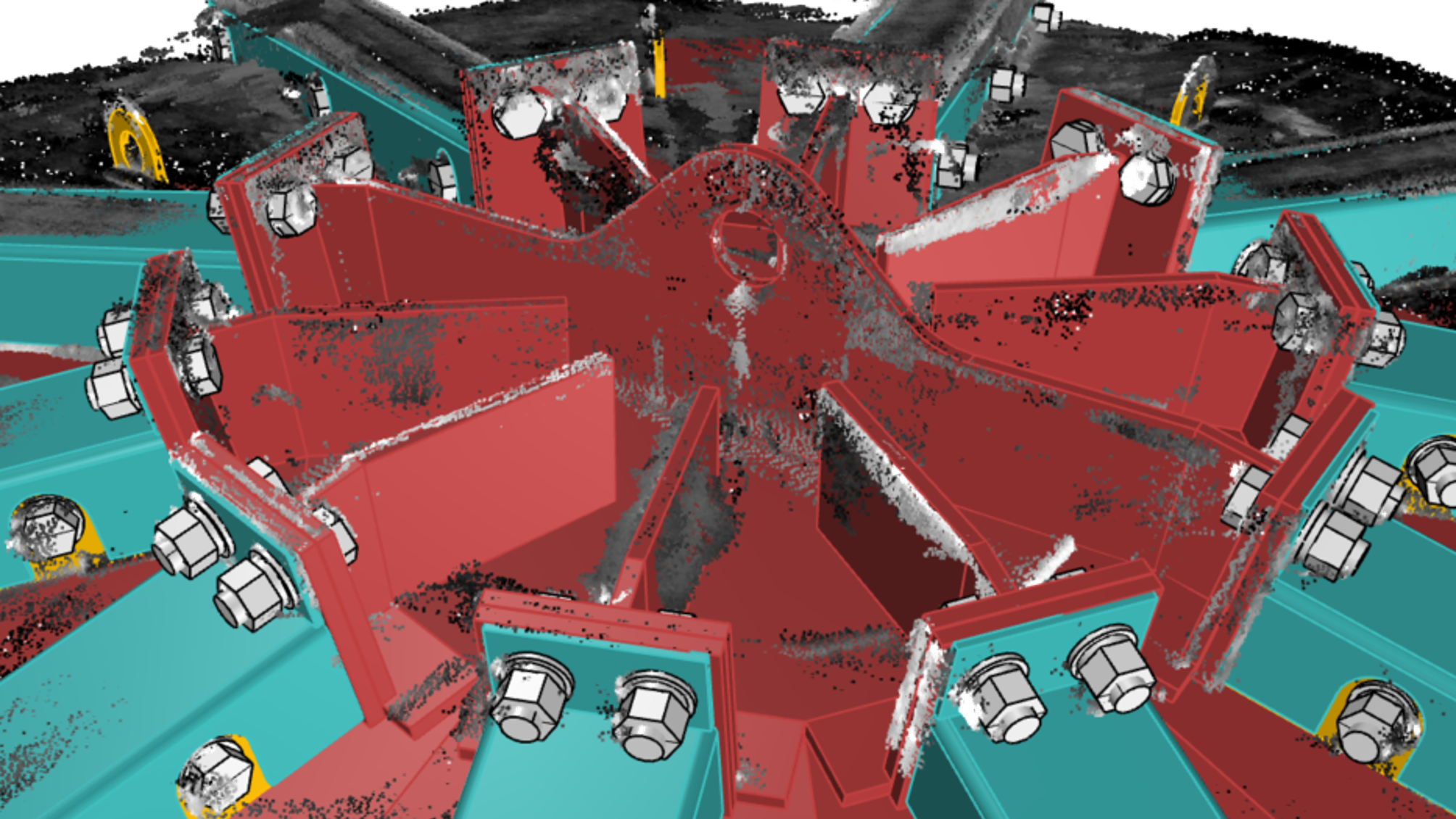
As part of the project related to the Conical Reaction Chamber Section on the scrubber, we carried out a comprehensive process to replace the damaged component, covering several key stages.
In the first phase, we conducted a detailed inspection of the damaged component using advanced 3D scanning technology. This allowed for a precise assessment of the technical condition and the collection of necessary data to develop a new design. Based on the scanning results, we prepared a complete replacement design and full technical documentation, ensuring high accuracy and compliance with the construction and operational requirements of the scrubber.
The next step involved prefabrication of the new component in the production hall. We used modern technologies and materials with high resistance to aggressive gases and operational conditions within the scrubber’s reaction chamber. The prefabrication process proceeded according to schedule and quality standards, guaranteeing the durability and strength of the new component.
After completing the prefabrication, we proceeded with the preparation for the component replacement on the ship. This included detailed logistical planning, coordination of the installation team’s activities, and ensuring the necessary technical resources and safety measures. The replacement process was carried out efficiently with minimal operational downtime for the vessel.
The final stage was the installation of the new Conical Reaction Chamber Section on the scrubber onboard the ship. Due to prior preparation and precision in prefabrication, the installation was completed without disruptions. Functional tests were conducted, confirming full operational efficiency and compliance with technical requirements.
The project was successfully completed, enhancing the scrubber’s operational efficiency while increasing its durability and reliability.
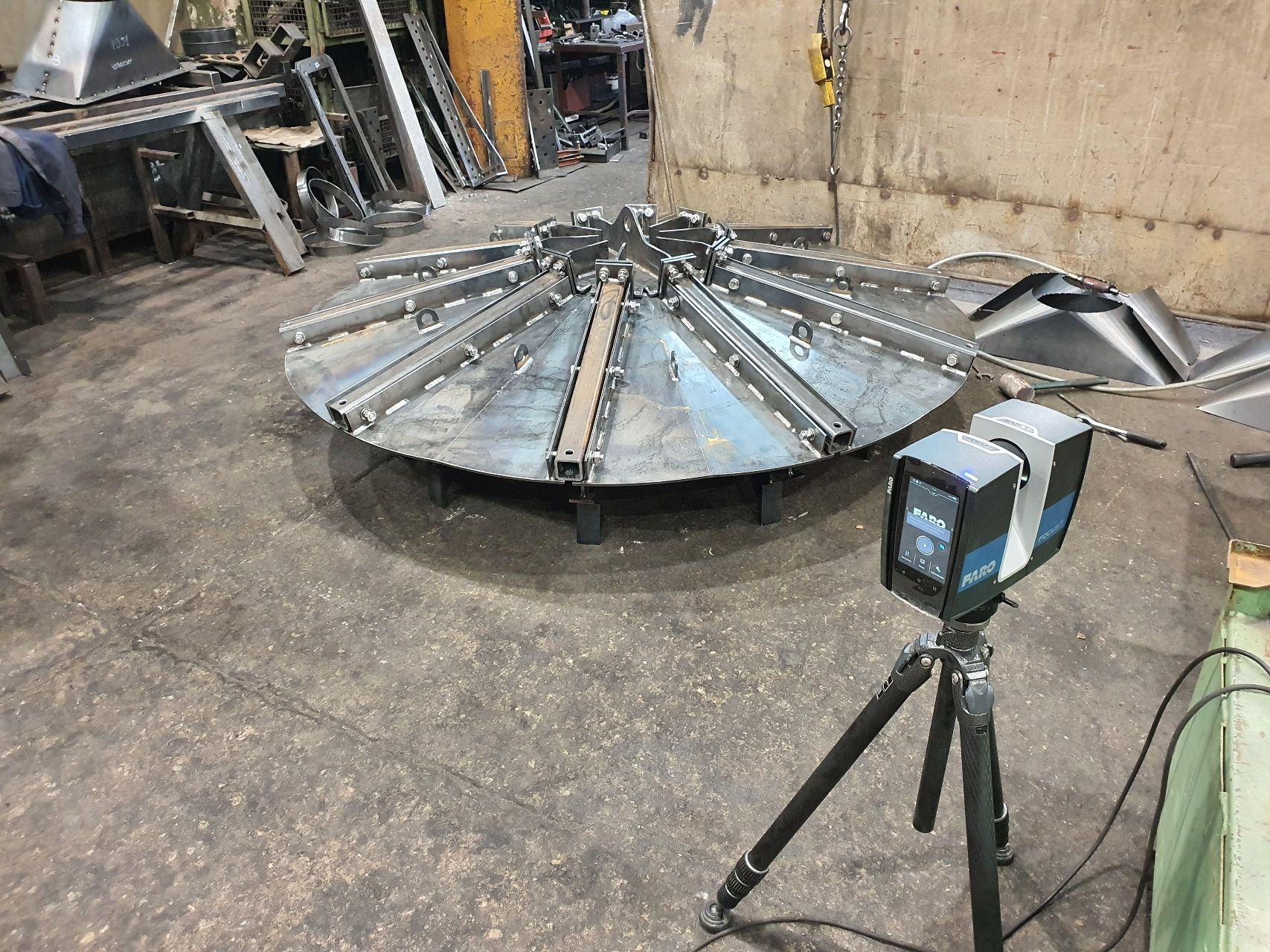
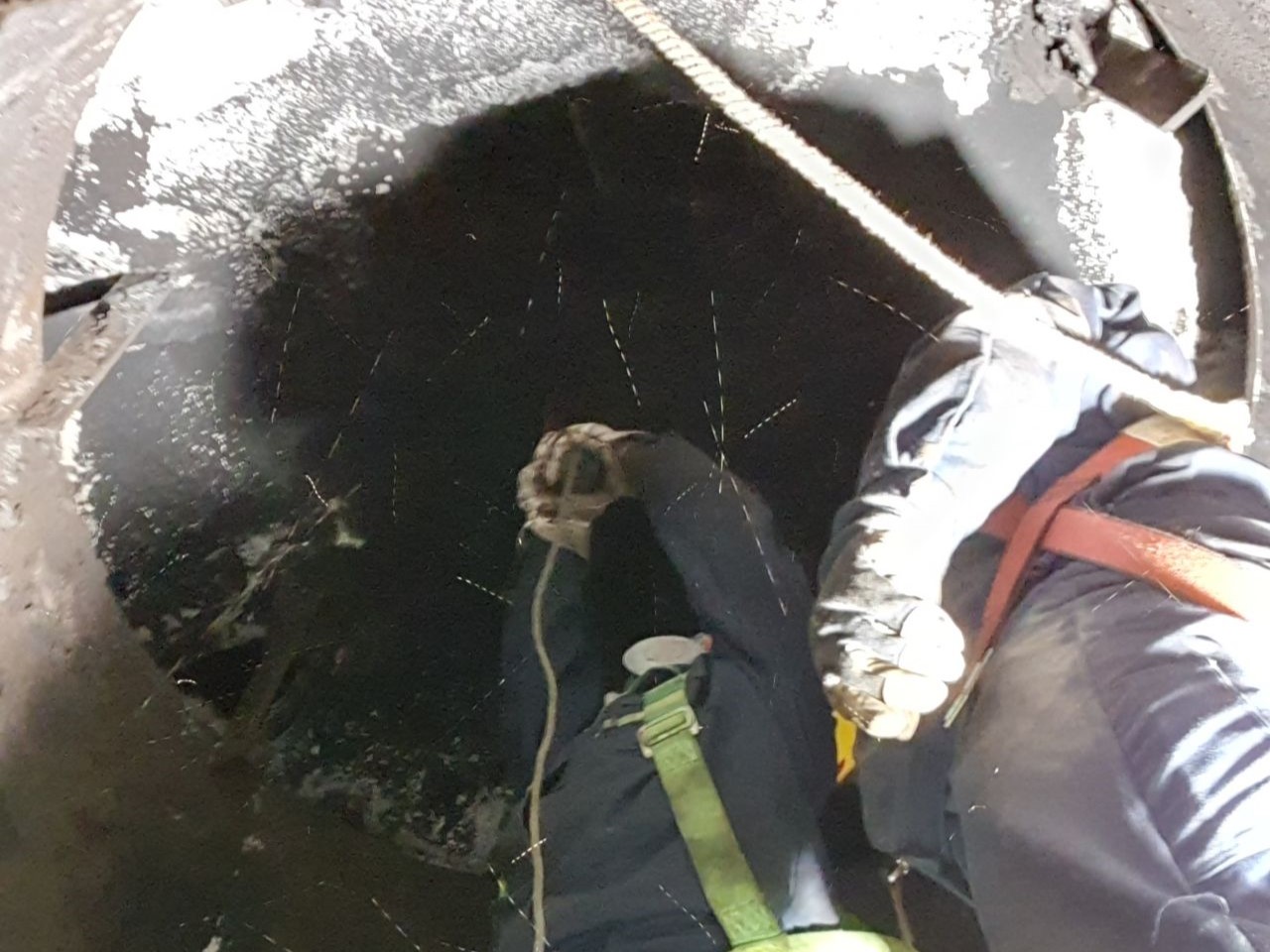
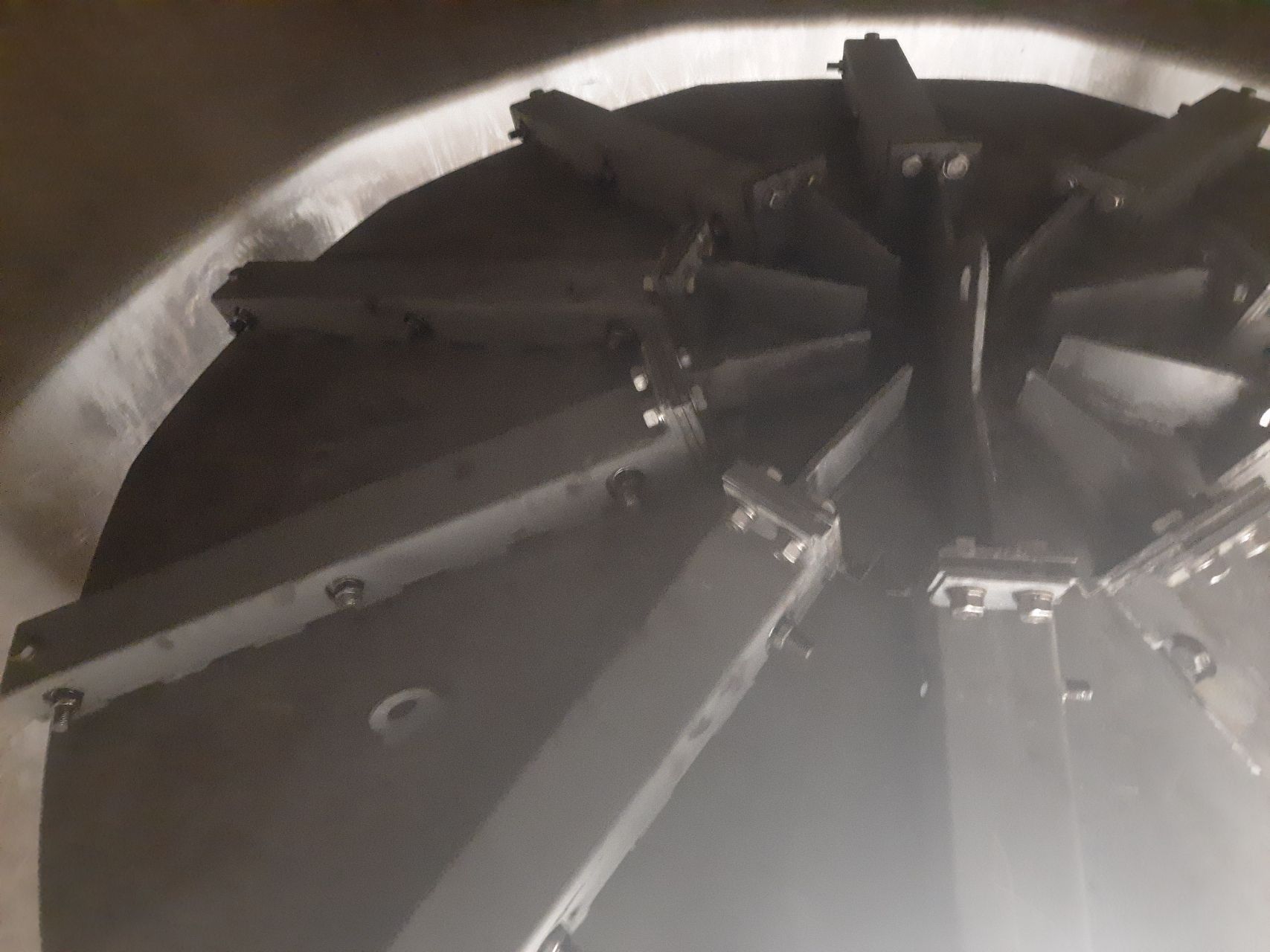
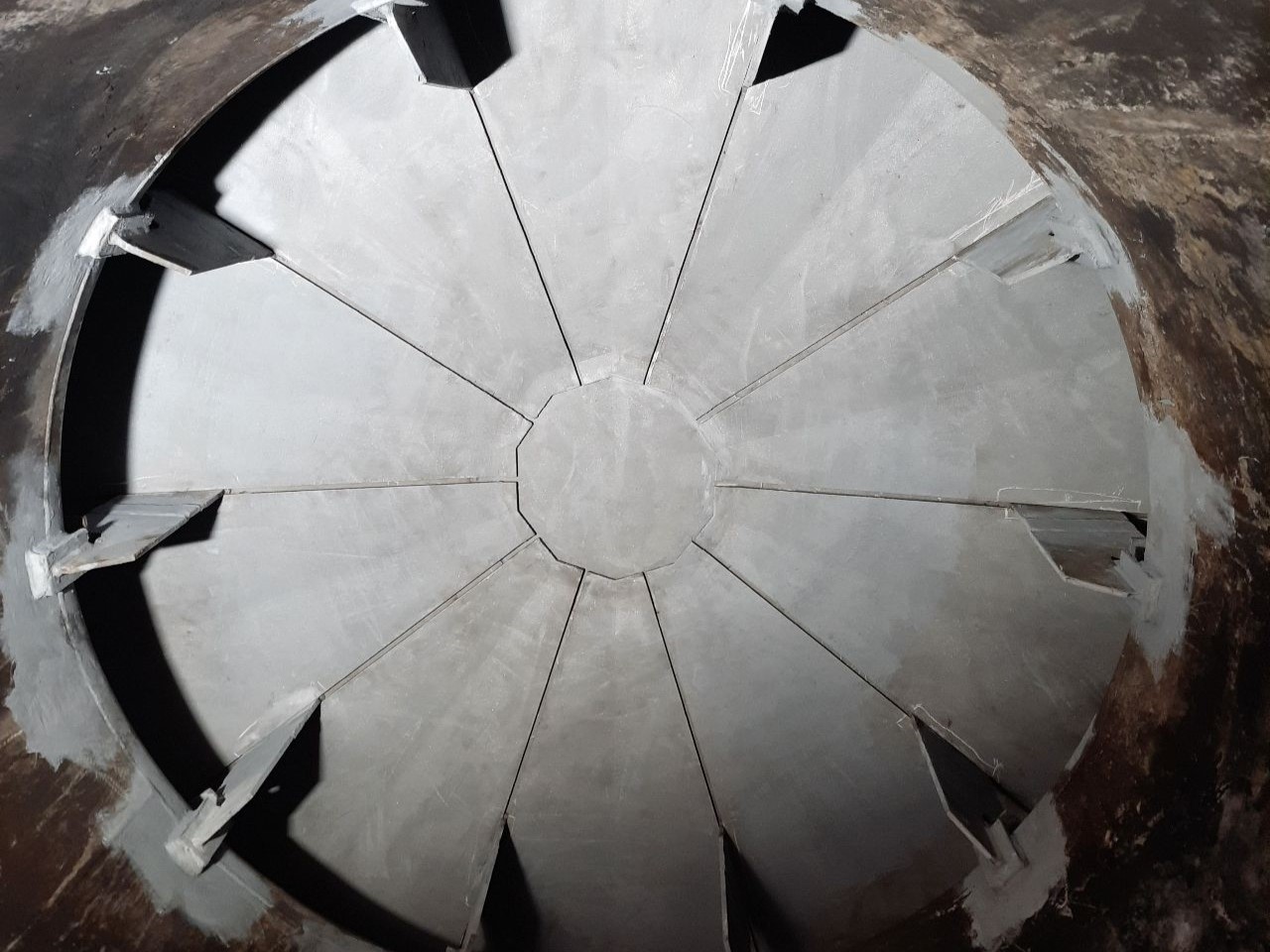