ENGINE C.W. HEAT EXCHANGER
ENGINE C.W. HEAT EXCHANGER
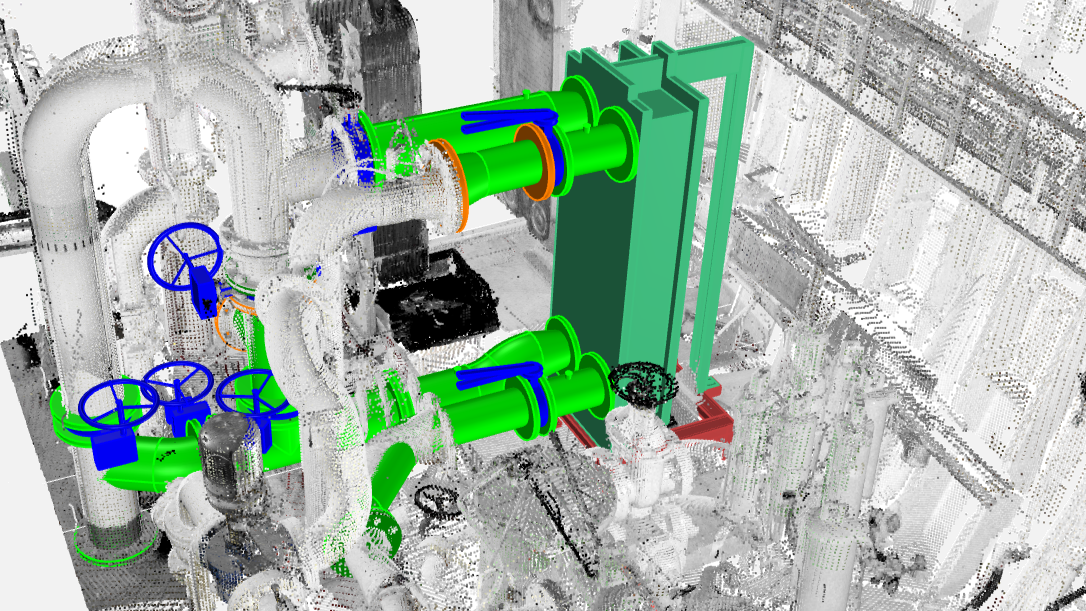
On the vessel where we had previously installed the ballast water treatment system (BWTS), it became necessary to replace the main engine cooler. The decision to replace it was due to operational wear and the need to adapt the cooling system to the vessel’s current operational requirements. Thanks to a prior inspection, we had a complete set of technical data, which allowed for precise planning of the entire process and helped avoid unexpected issues during installation.
The work began with creating a detailed 3D model of the new cooler, foundation, and piping connections. The modeling process took into account the available space, existing structural elements, and installations to ensure optimal component fit. A subsequent analysis of potential installation issues helped identify and eliminate any difficulties at the design stage. Model verification was a crucial step, as any errors at this stage could lead to complications during installation on the vessel, especially considering the limited docking time in port.
Once the model was approved, we proceeded with the prefabrication of all necessary components. This process included preparing the foundation and appropriate pipeline sections that would be connected to the existing main engine cooling system. Prefabrication in controlled workshop conditions ensured high precision in execution and reduced the time required for onboard assembly.
After prefabrication was completed, the components were delivered to the vessel and prepared for installation. The cooler replacement was carried out while the ship was docked in port, requiring efficient work organization and close team coordination. The removal of the old cooler and installation of the new one had to be executed quickly and efficiently to avoid extending the vessel’s downtime. During the installation, proper pipeline connections, leak tests, and operational checks of the cooling system were carried out to ensure full functionality after the work was completed.
The entire process was executed as planned, and the cooler replacement was successfully completed. Thanks to prior planning, precise prefabrication, and efficient execution of the installation work, we managed to minimize the vessel’s downtime and ensure its full operational readiness.
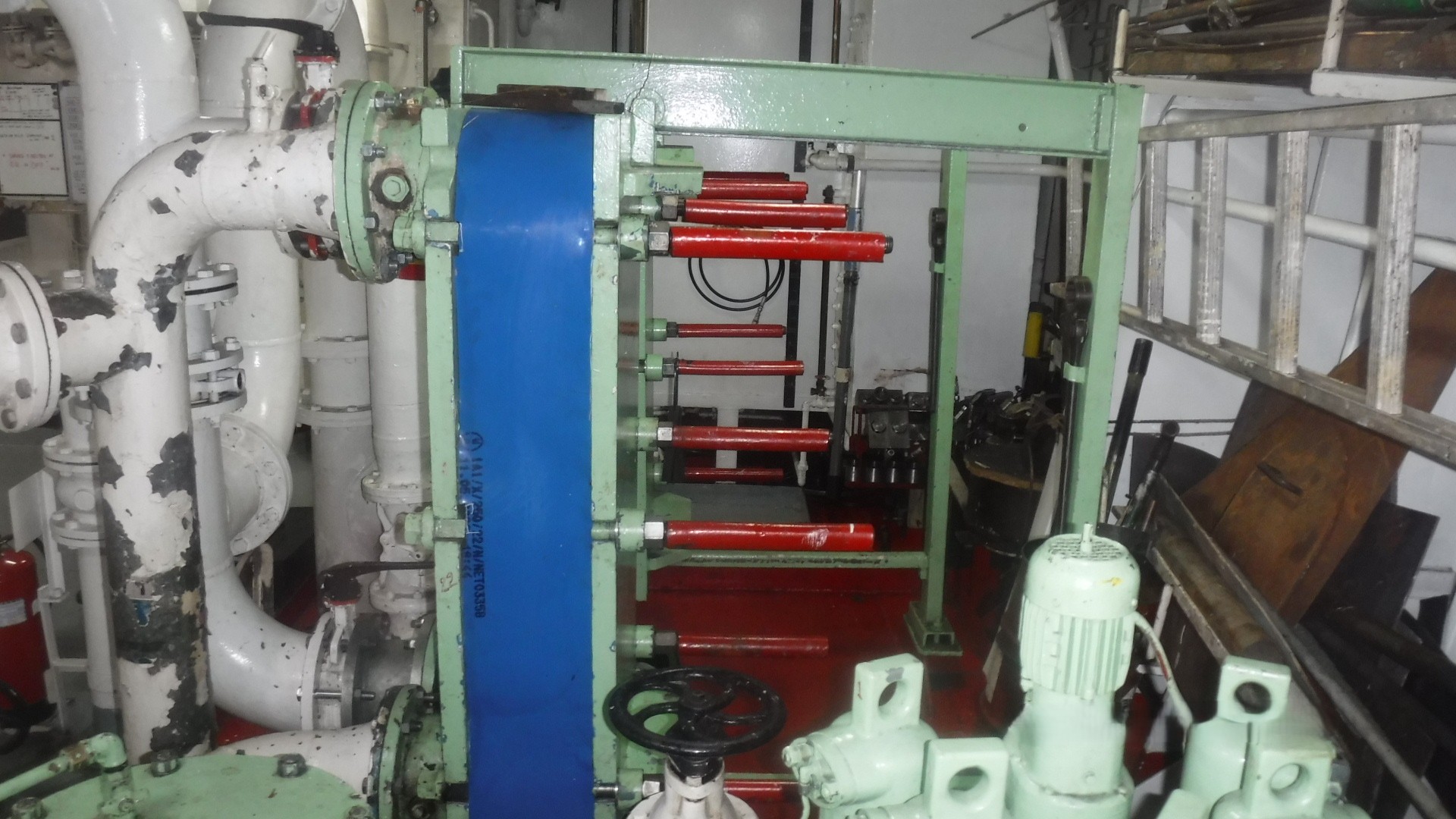
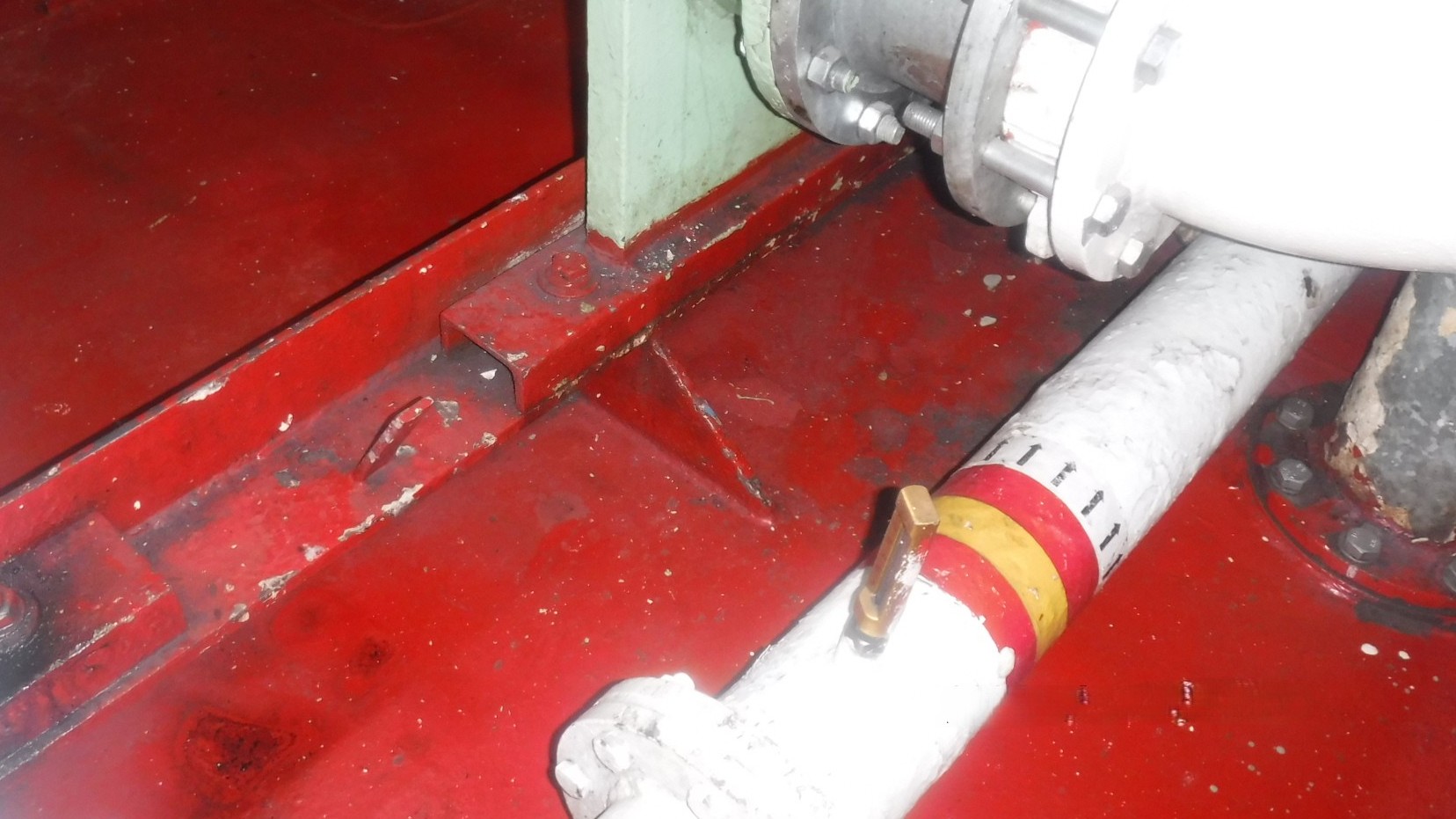

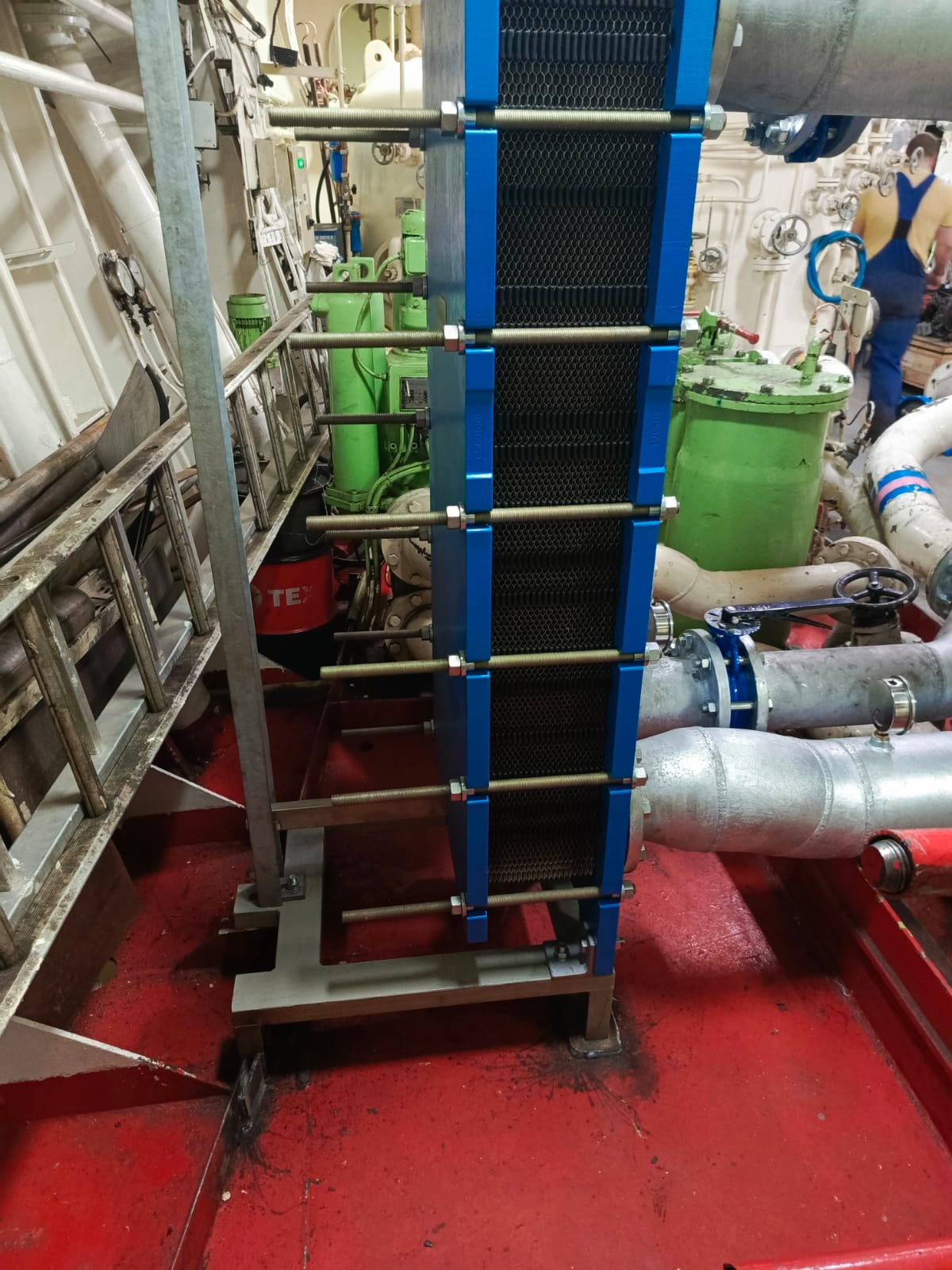
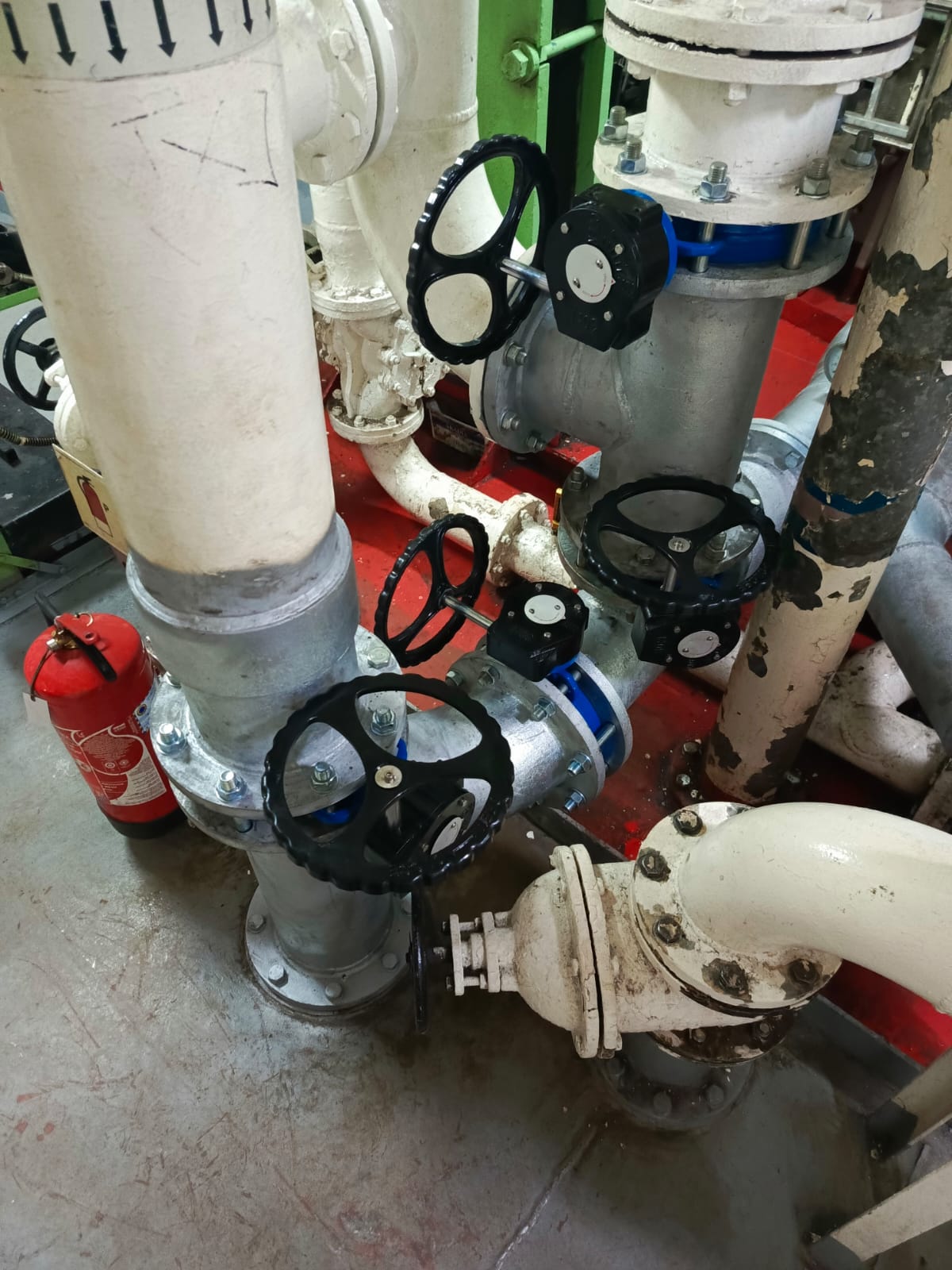
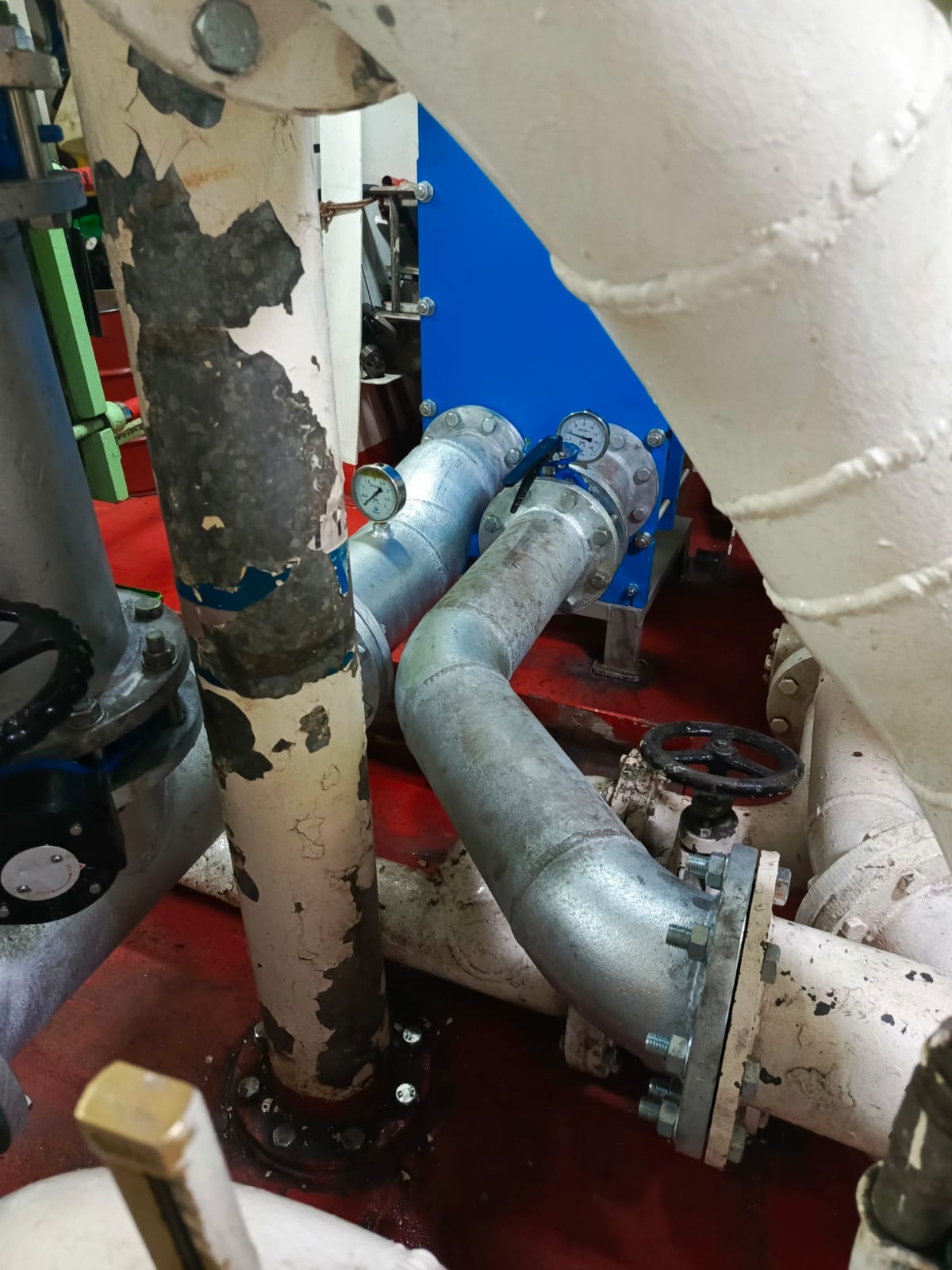
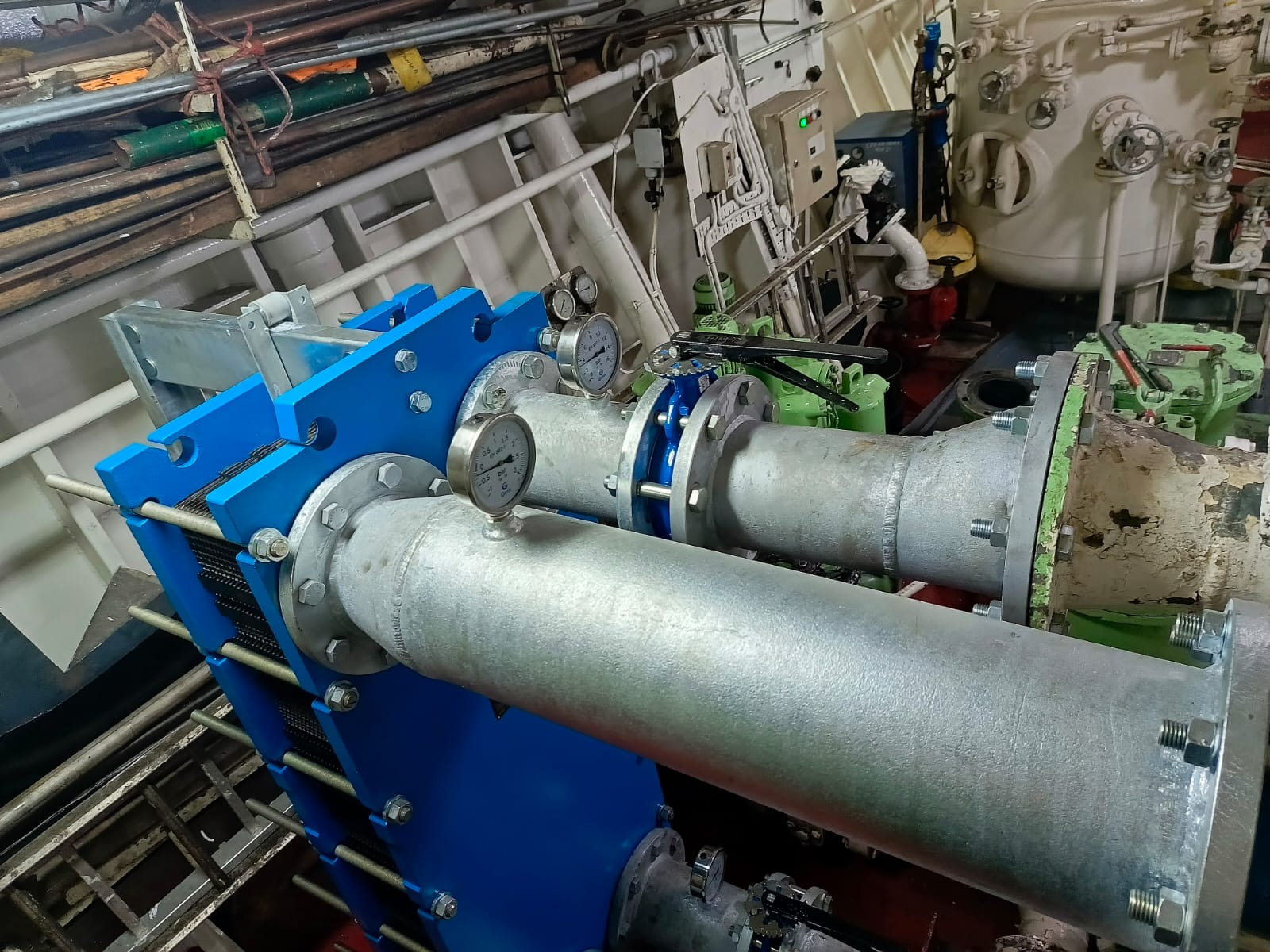
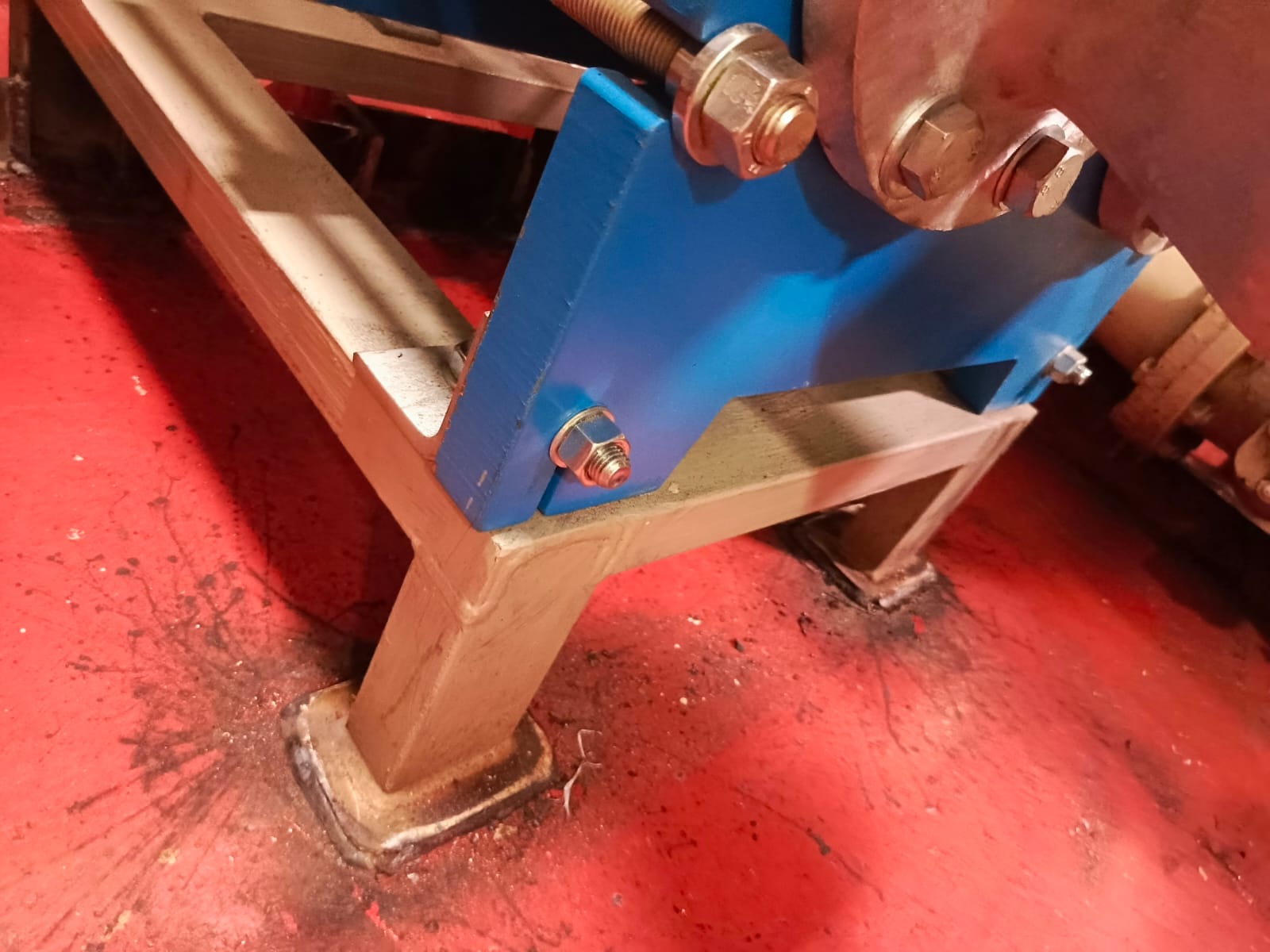
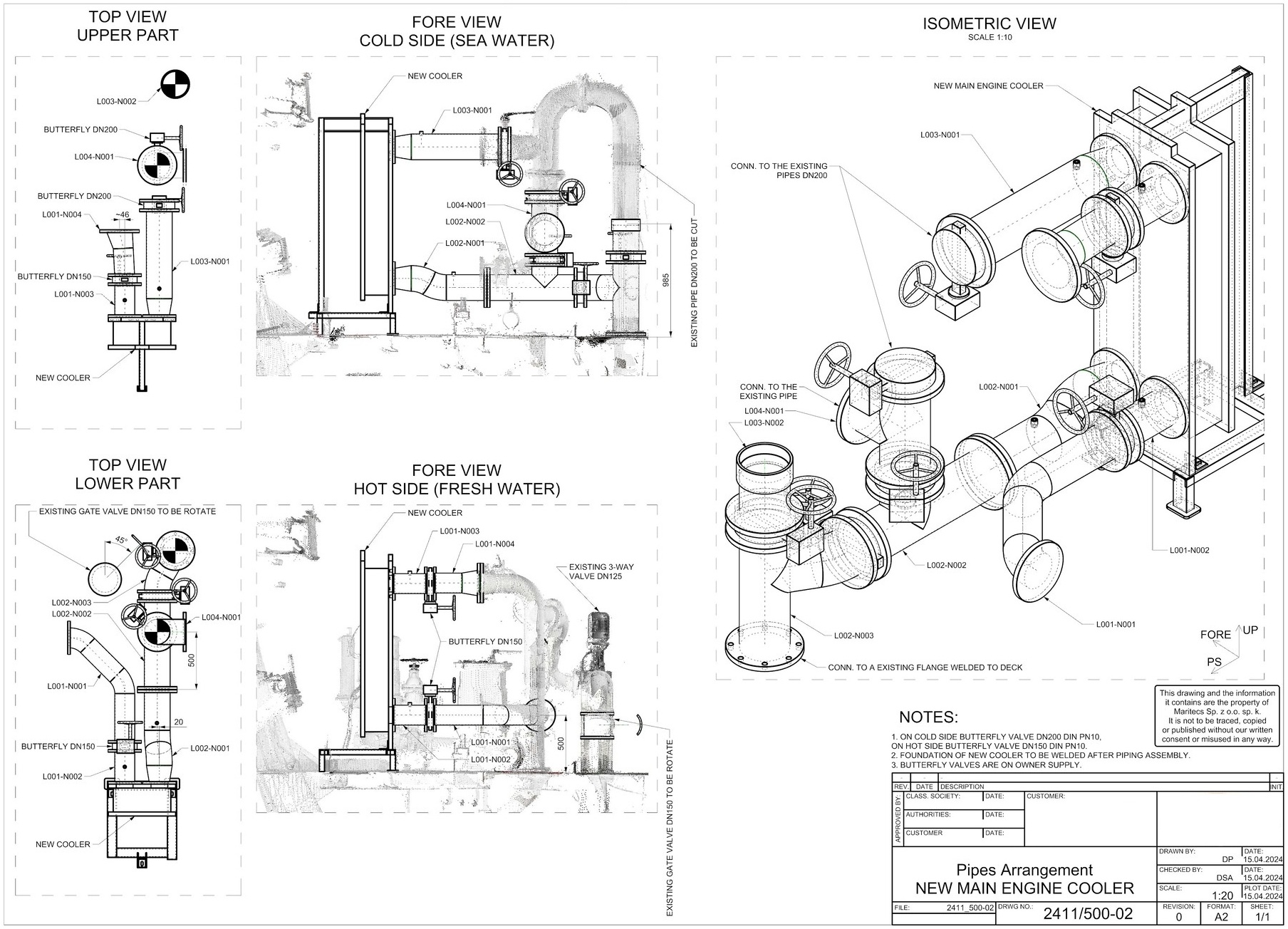
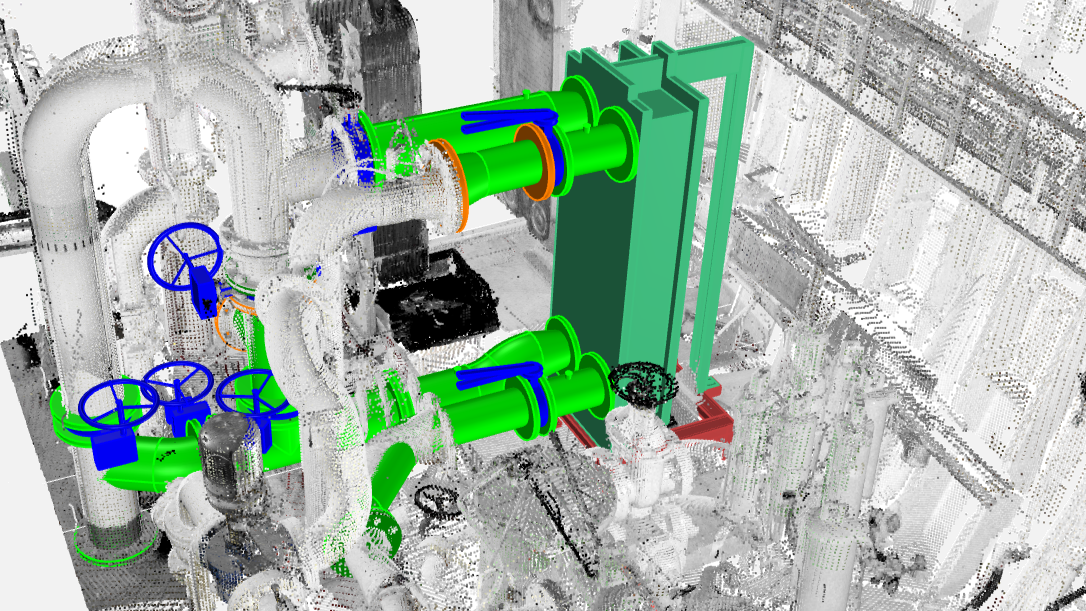
On the vessel where we had previously installed the ballast water treatment system (BWTS), it became necessary to replace the main engine cooler. The decision to replace it was due to operational wear and the need to adapt the cooling system to the vessel’s current operational requirements. Thanks to a prior inspection, we had a complete set of technical data, which allowed for precise planning of the entire process and helped avoid unexpected issues during installation.
The work began with creating a detailed 3D model of the new cooler, foundation, and piping connections. The modeling process took into account the available space, existing structural elements, and installations to ensure optimal component fit. A subsequent analysis of potential installation issues helped identify and eliminate any difficulties at the design stage. Model verification was a crucial step, as any errors at this stage could lead to complications during installation on the vessel, especially considering the limited docking time in port.
Once the model was approved, we proceeded with the prefabrication of all necessary components. This process included preparing the foundation and appropriate pipeline sections that would be connected to the existing main engine cooling system. Prefabrication in controlled workshop conditions ensured high precision in execution and reduced the time required for onboard assembly.
After prefabrication was completed, the components were delivered to the vessel and prepared for installation. The cooler replacement was carried out while the ship was docked in port, requiring efficient work organization and close team coordination. The removal of the old cooler and installation of the new one had to be executed quickly and efficiently to avoid extending the vessel’s downtime. During the installation, proper pipeline connections, leak tests, and operational checks of the cooling system were carried out to ensure full functionality after the work was completed.
The entire process was executed as planned, and the cooler replacement was successfully completed. Thanks to prior planning, precise prefabrication, and efficient execution of the installation work, we managed to minimize the vessel’s downtime and ensure its full operational readiness.
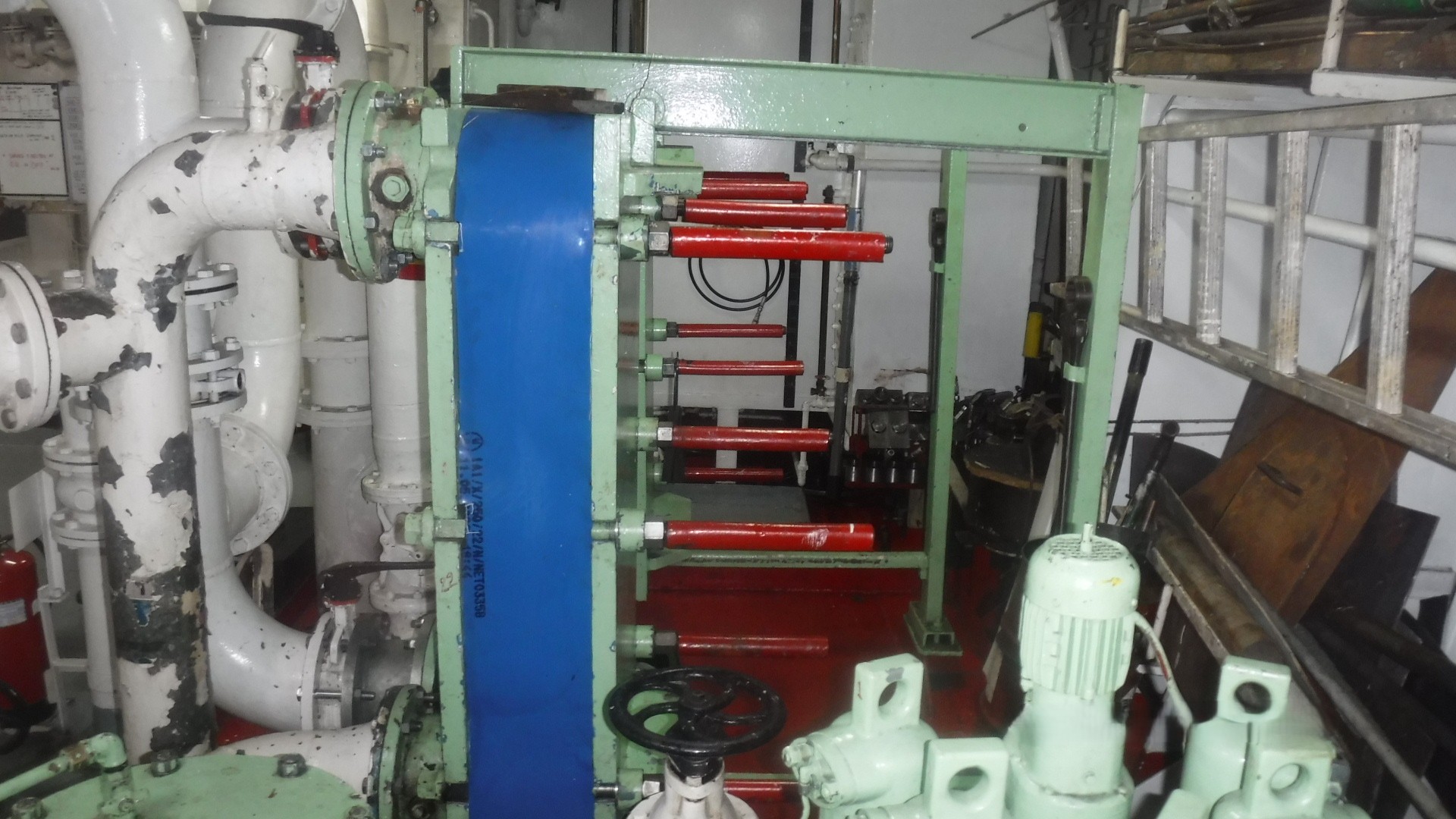
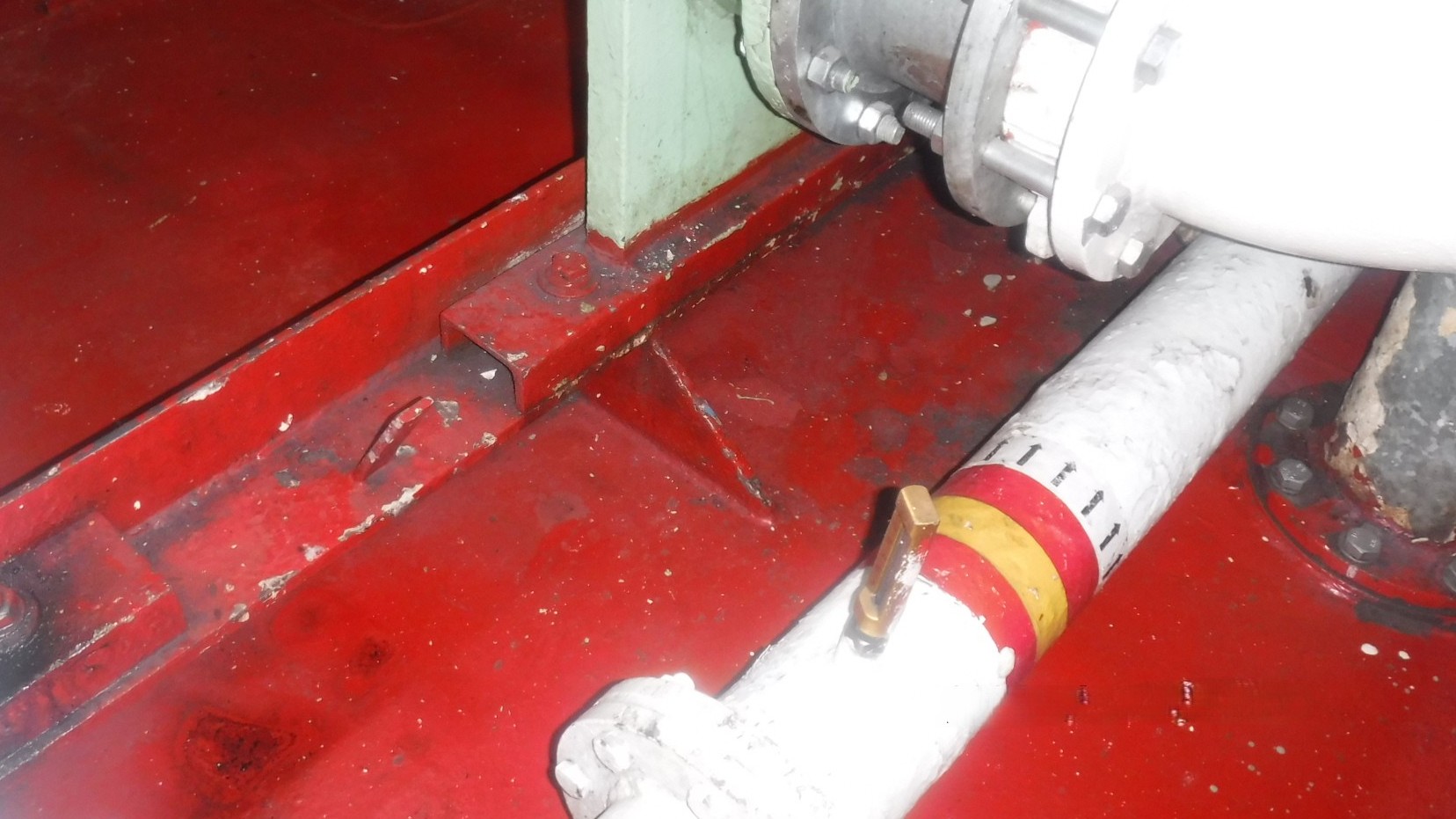

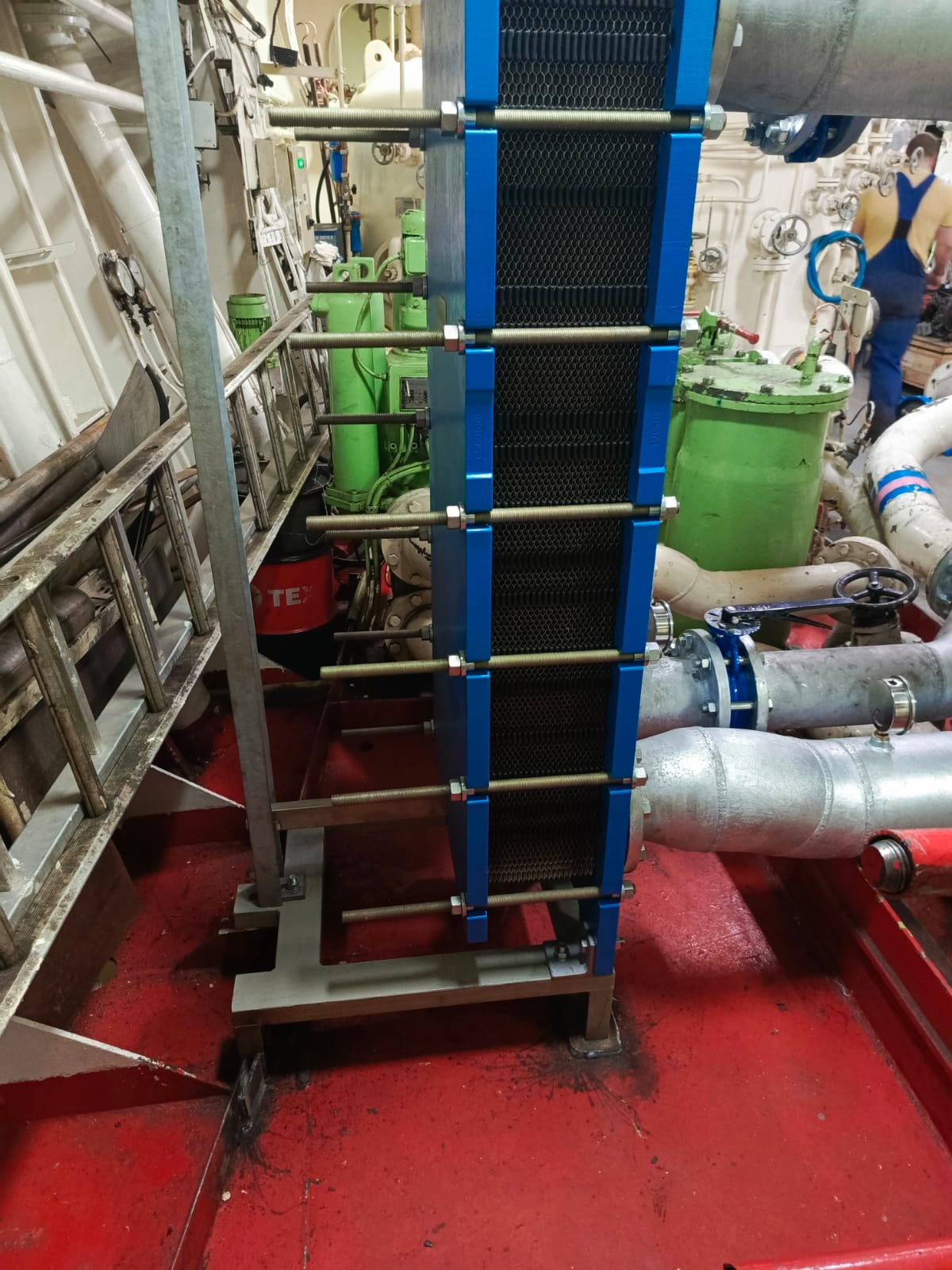
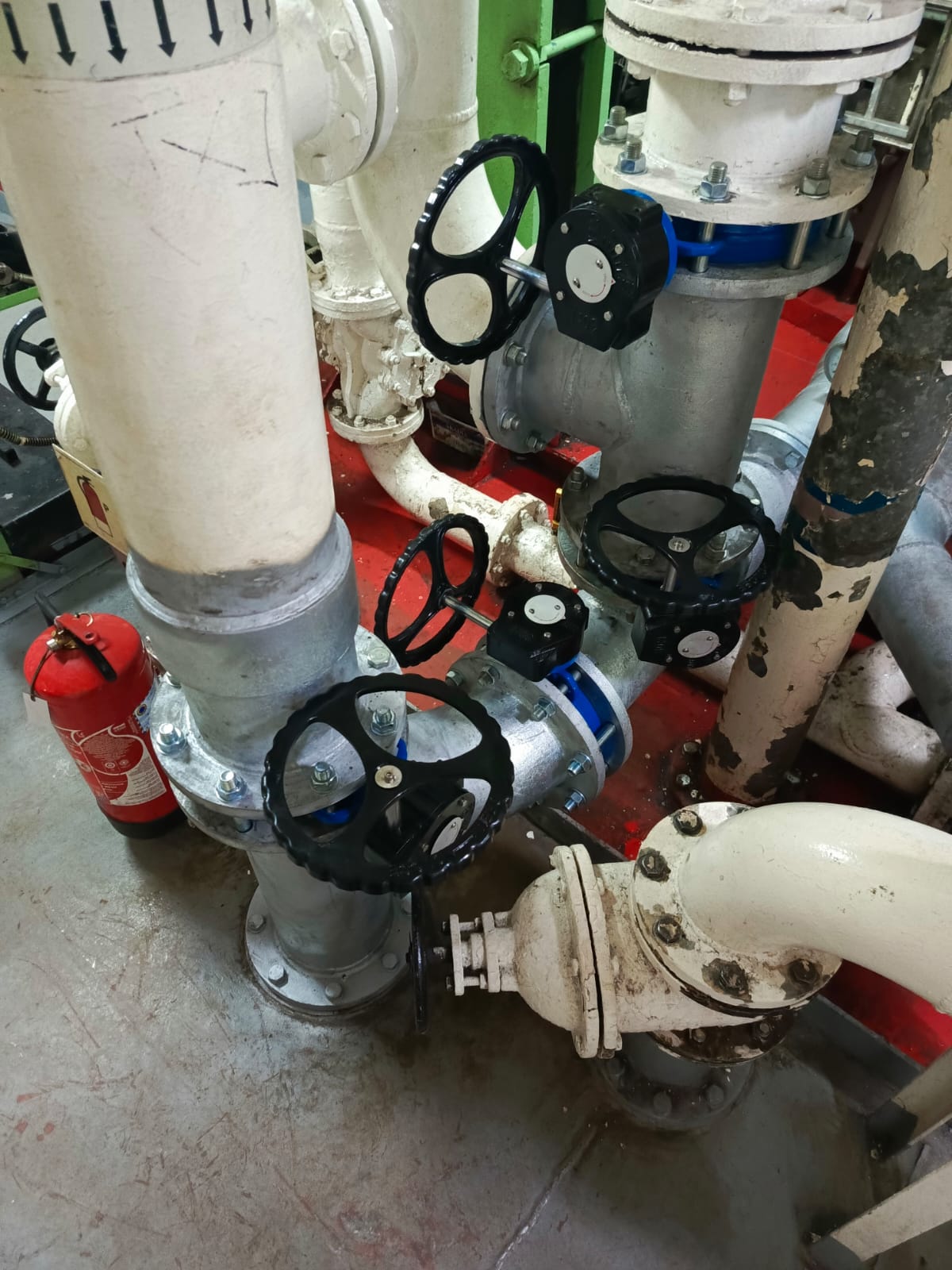
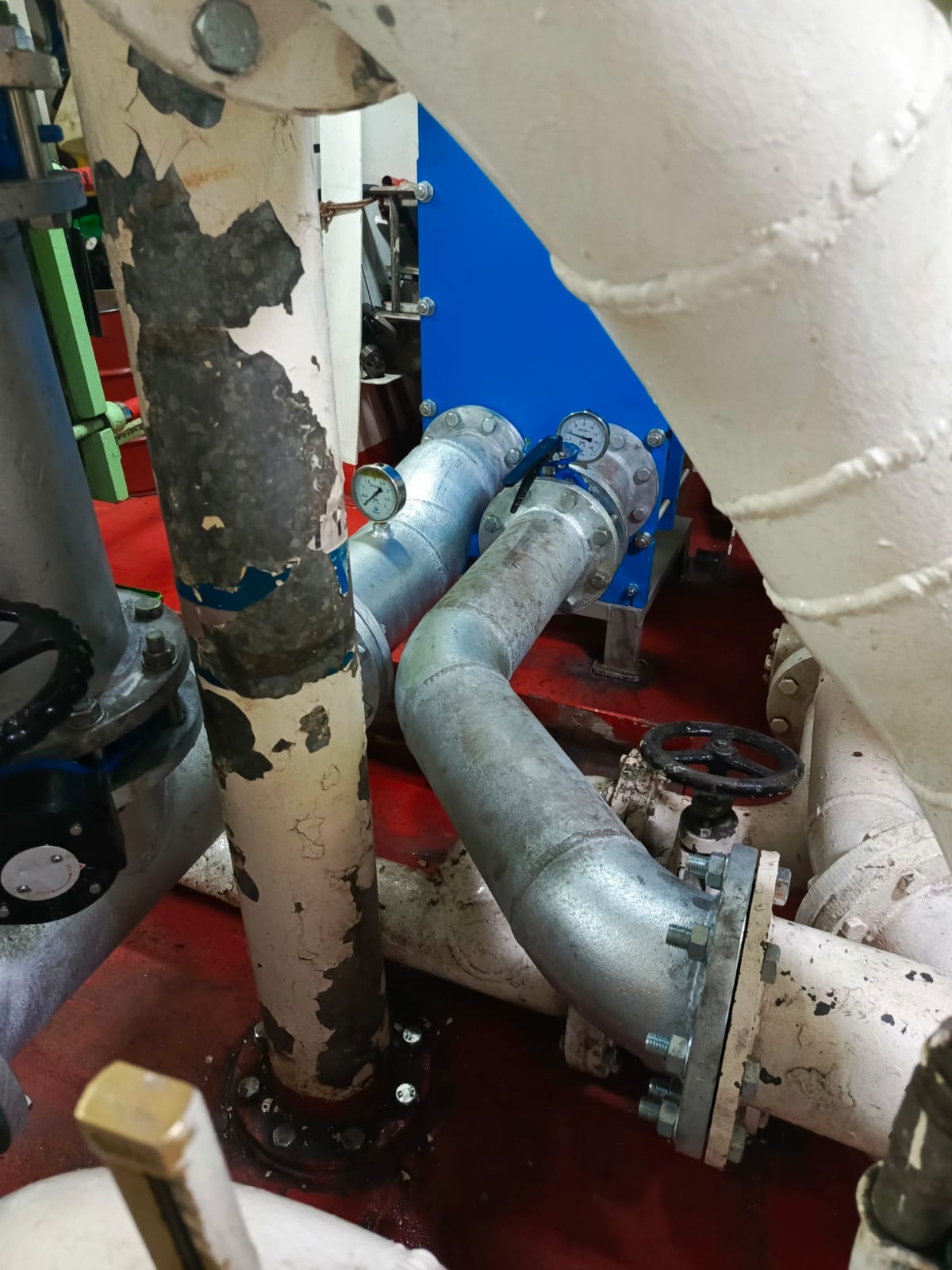
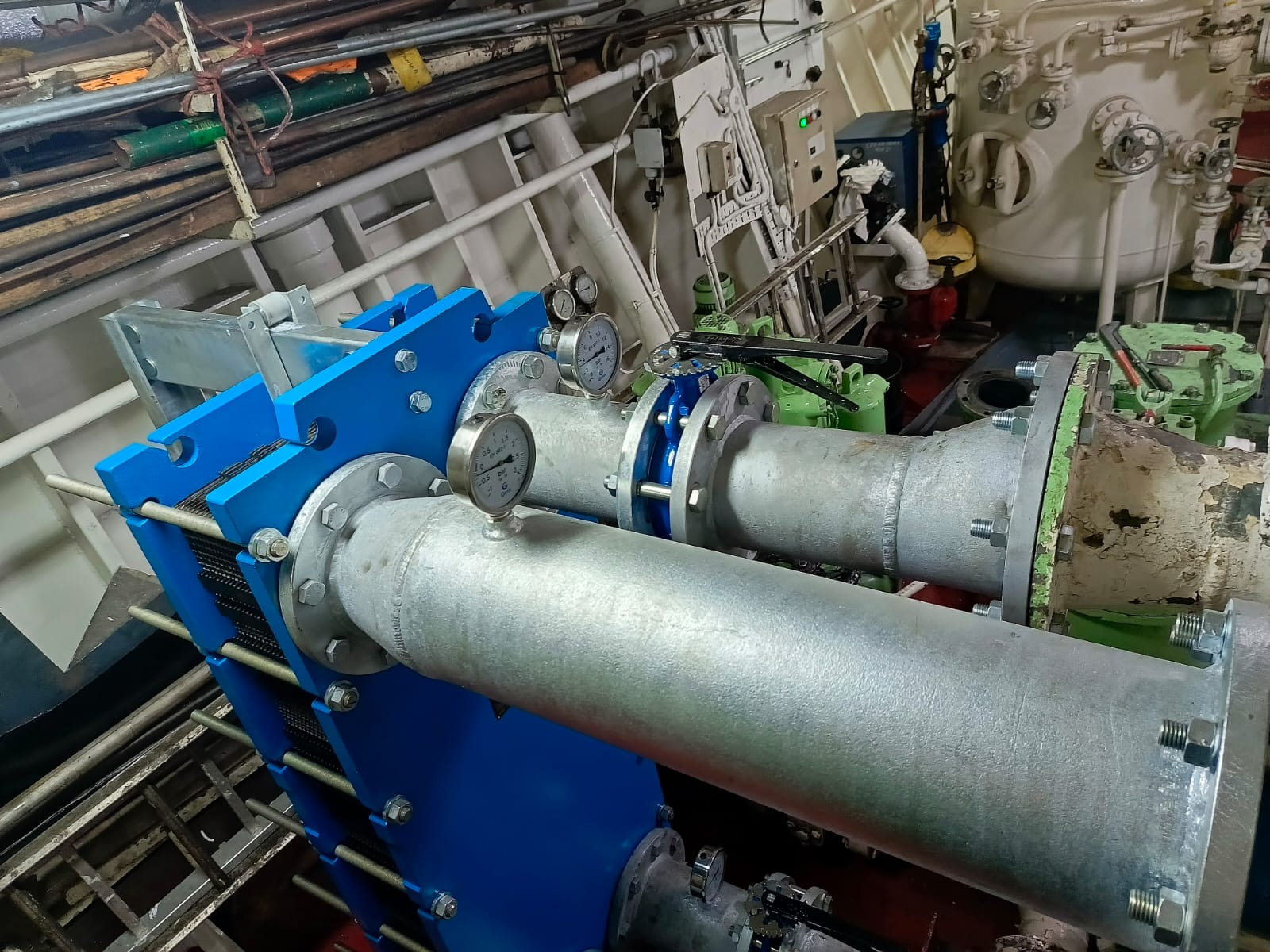
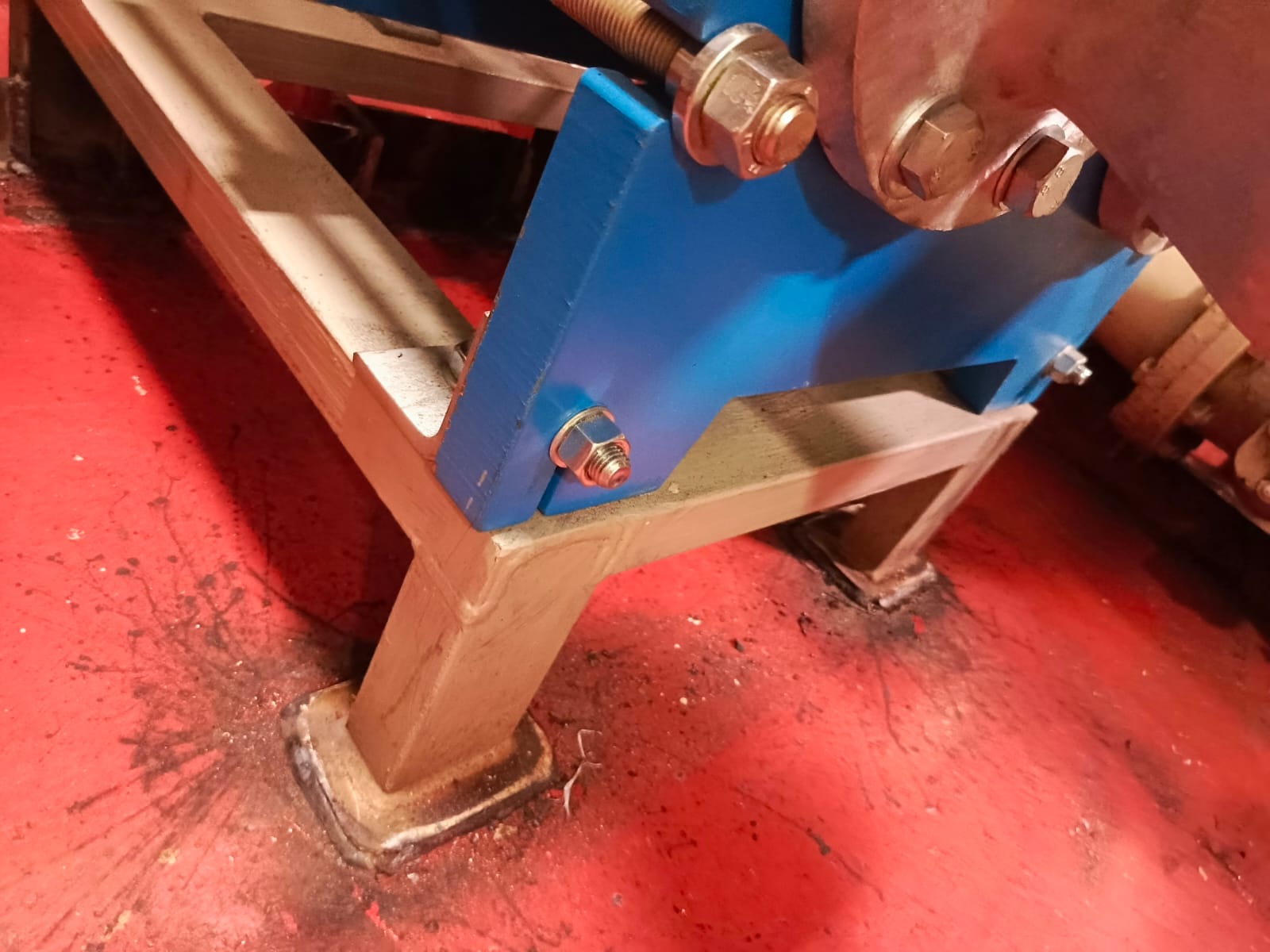
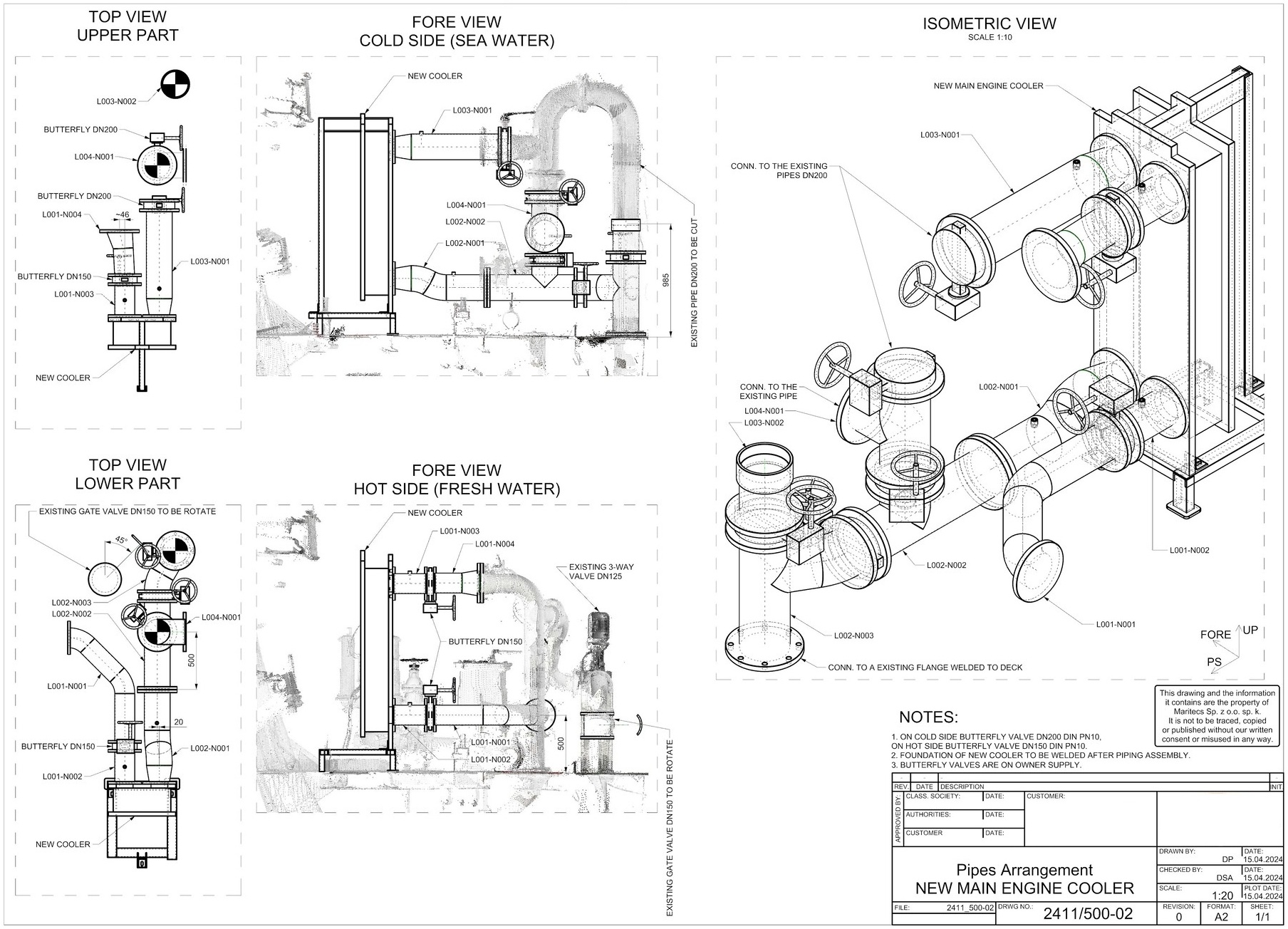