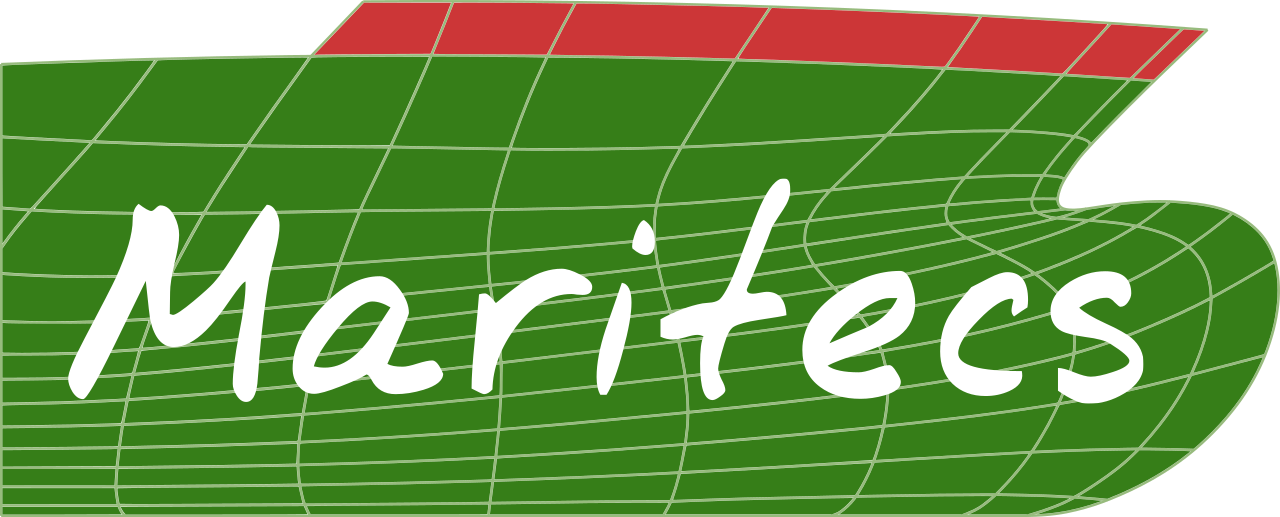
MARINE TECHNOLOGY AND SOLUTIONS
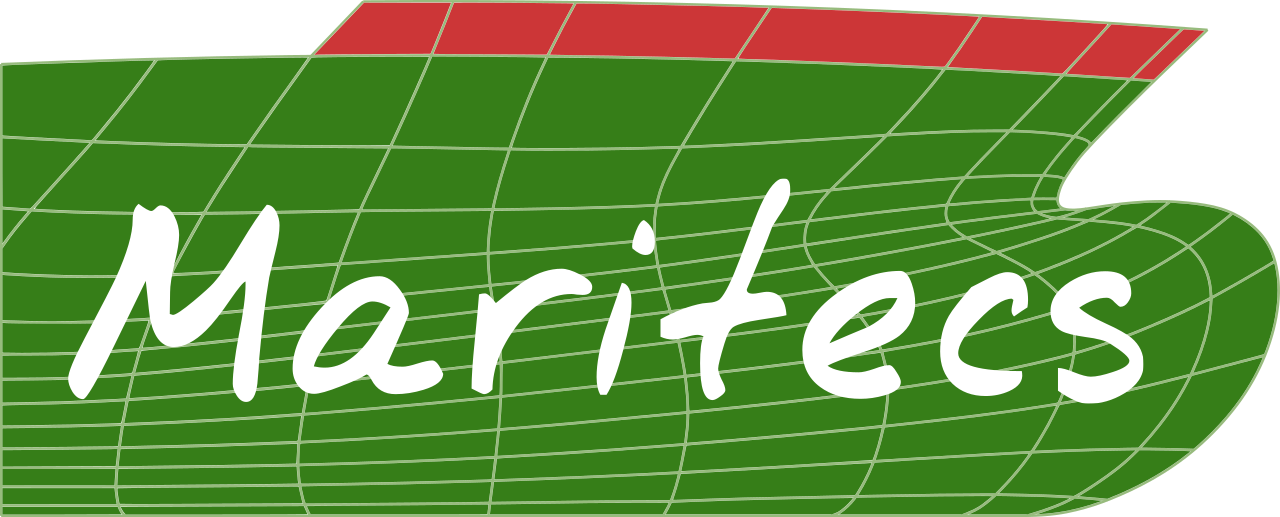
MARINE TECHNOLOGY AND SOLUTIONS
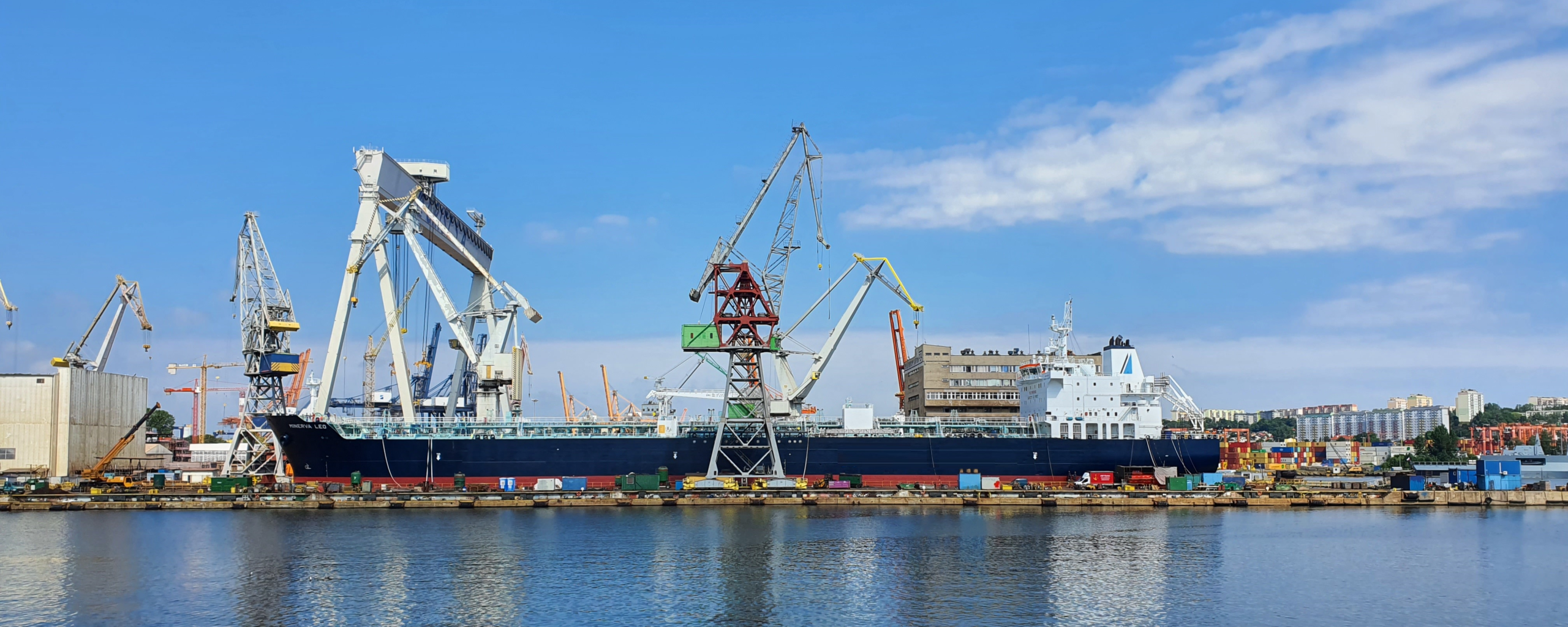

Maritime Expertise Beyond Competition
• hull and steel structures • outfiting • piping systems • HVAC • automation and electrical engineering •
Maritime Expertise Beyond Competition
• hull and steel structures • outfiting •
• piping systems • HVAC •
• automation and electrical engineering •
The owner and key figure behind the company brings over 25 years of experience in the maritime industry. MARITECS was founded at the end of 2019, following the reorganization of a self-employed business that had been established in 2004, originally known as MTE-DESIGN. This transformation marked a new chapter in the company’s evolution, building on a solid foundation of industry experience and a commitment to innovation in maritime solutions. Today, MARITECS is a team of highly skilled and experienced engineers, committed to delivering innovative and reliable solutions.
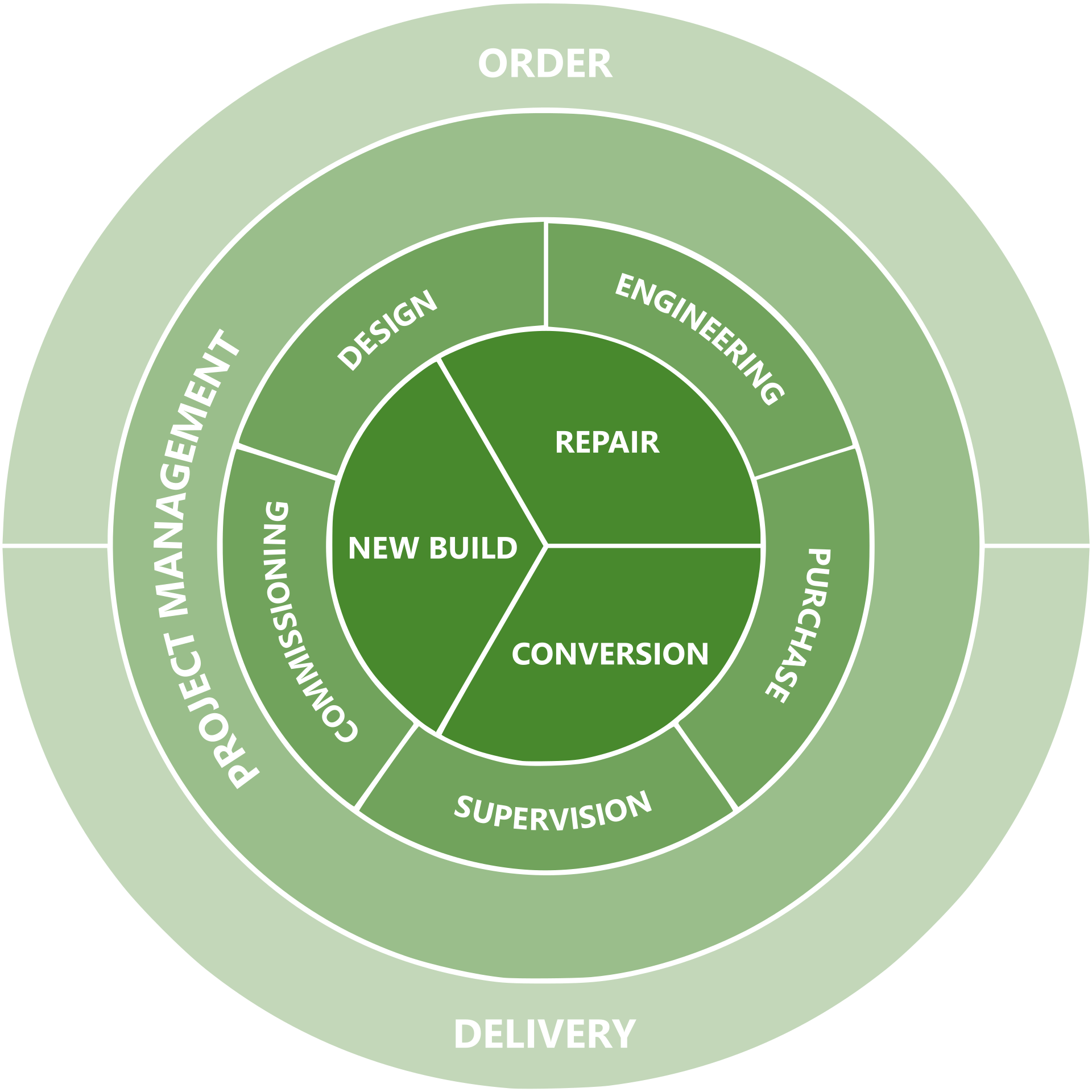
The owner and key figure behind the company brings over 25 years of experience in the maritime industry. MARITECS was founded at the end of 2019, following the reorganization of a self-employed business that had been established in 2004, originally known as MTE-DESIGN. This transformation marked a new chapter in the company’s evolution, building on a solid foundation of industry experience and a commitment to innovation in maritime solutions. Today, MARITECS is a team of highly skilled and experienced engineers, committed to delivering innovative and reliable solutions.
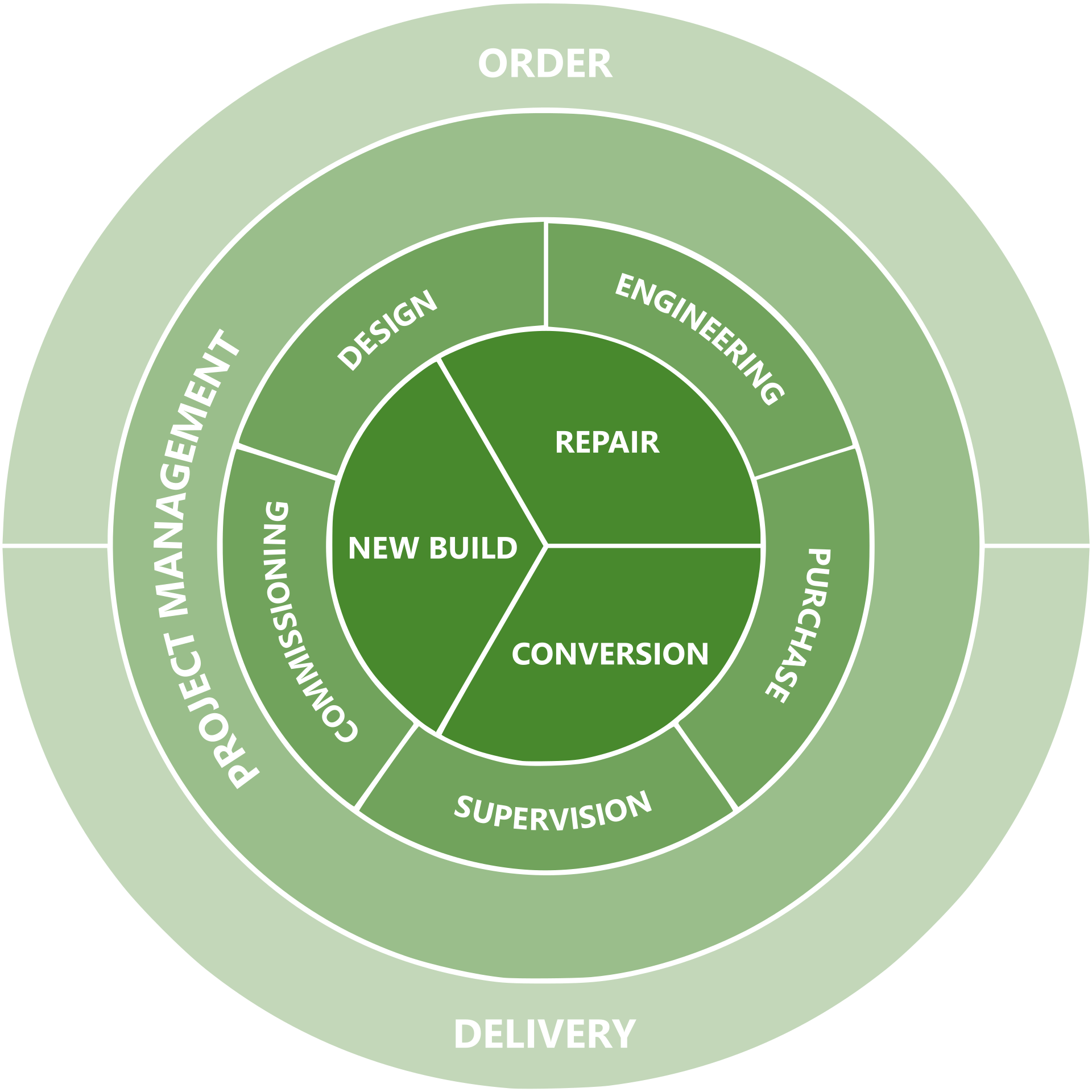
New Build
From Concept to Completion
We provide end-to-end support for new vessel construction, ensuring efficiency, compliance, and top performance. From concept design and structural analysis to material procurement and modular assembly, we streamline the process for cost-effective production. Our on-site supervision guarantees quality, while final commissioning, including sea trials and certification, ensures full operational readiness.
Repair
Restoring Operational Integrity
Ship repair involves maintaining, restoring, and repairing vessel components to ensure seaworthiness and operational efficiency. This includes addressing structural integrity, worn-out systems, and necessary refurbishments. We focus on restoring vessel functionality by ensuring all repairs align with safety and regulatory standards, extending the ship’s operational lifespan.
Conversion
Enhancing Vessel Capabilities
Ship conversion modifies an existing vessel to enhance capabilities, improve efficiency, or comply with new operational and regulatory requirements. It often involves structural changes, equipment upgrades, and system adaptations. Conversions allow vessels to meet evolving industry demands, optimize performance, and integrate new technologies while ensuring full compliance with maritime regulations.
Key Maritime Stages Execution
Inspection
Ensuring Safety & Compliance
Comprehensive inspections verify vessel integrity, safety, and regulatory compliance at every stage of operation. Our inspection services include:
- Pre-repair inspections: Assessment of a vessel’s technical condition before planned repairs to identify areas requiring intervention and ensure the effectiveness of the repair process.
- Pre-conversion inspections: Detailed structural and system analysis before planned modifications to evaluate feasibility and the scope of required work.
- Hull integrity assessments: Use of non-destructive testing (NDT) to assess hull integrity and identify potential damage or corrosion.
- Machinery and system evaluations: Examination of onboard machinery and systems to prevent failures and ensure operational reliability.
- Regulatory compliance audits: Conducting compliance audits with classification society requirements and flag state administration to ensure full adherence to regulations.
Design
From Draft to Class Compliance
We deliver innovative and efficient ship designs, integrating performance optimization, regulatory compliance, and cost-effective construction methods:
- Conceptual and feasibility studies
- Hydrodynamic and structural analysis
- Digital prototyping with CAD and simulation tools
- 3D scanning and reverse engineering
- Compliance with IMO, SOLAS, and classification society requirements
Supervision
Ensuring Quality at Every Stage
We provide expert supervision throughout the shipbuilding, repair, and conversion processes, ensuring adherence to specifications, safety standards, and project timelines:
- Worksite inspections and quality assurance
- Structural and system installation oversight
- Coordination between shipyards, vendors, and regulatory bodies
- Safety compliance verification to meet class society and flag state requirements
- Problem-solving and risk mitigation during execution
Engineering
Structural and System Integration
Our engineering expertise ensures vessels operate safely, efficiently, and in compliance with global standards:
- Structural engineering for hull integrity and weight optimization
- Mechanical and piping systems design
- Electrical and automation systems integration
- Vibration and noise analysis for comfort and efficiency
- Environmental engineering (emission control, ballast water treatment)
Commissioning
Delivering Operational Readiness
Thorough testing and verification ensure vessels are fully operational and ready for deployment:
- Pre-commissioning inspections of all onboard systems
- Calibration and optimization of propulsion, HVAC, and automation
- Full-scale operational and sea trials
- Crew training on new systems and operational procedures
- Final certification and client handover
Purchase
Reliable Supply Chain Management
A strong procurement strategy ensures on-time delivery of high-quality components and materials for shipbuilding and repairs:
- Supplier evaluation and selection based on quality and reliability
- Contract negotiation for optimal cost and delivery terms
- Inventory control to prevent project delays
- Logistics coordination for efficient material flow
- Supplier quality audits to ensure compliance with specifications
Project Management
Seamless Execution from Start to Finish
Effective coordination and control are essential for delivering shipbuilding and repair projects on time and within budget. We ensure:
- Strategic planning and milestone tracking
- Resource allocation for personnel, equipment, and materials
- Risk identification and mitigation strategies
- Progress monitoring and adaptive project adjustments
- Transparent reporting and stakeholder communication
New Build
From Concept to Completion
We provide end-to-end support for new vessel construction, ensuring efficiency, compliance, and top performance. From concept design and structural analysis to material procurement and modular assembly, we streamline the process for cost-effective production. Our on-site supervision guarantees quality, while final commissioning, including sea trials and certification, ensures full operational readiness.
Repair
Restoring Operational Integrity
Ship repair involves maintaining, restoring, and repairing vessel components to ensure seaworthiness and operational efficiency. This includes addressing structural integrity, worn-out systems, and necessary refurbishments. We focus on restoring vessel functionality by ensuring all repairs align with safety and regulatory standards, extending the ship’s operational lifespan.
Conversion
Enhancing Vessel Capabilities
Ship conversion modifies an existing vessel to enhance capabilities, improve efficiency, or comply with new operational and regulatory requirements. It often involves structural changes, equipment upgrades, and system adaptations. Conversions allow vessels to meet evolving industry demands, optimize performance, and integrate new technologies while ensuring full compliance with maritime regulations.
Key Maritime Stages Execution
Inspection
Ensuring Safety & Compliance
Comprehensive inspections verify vessel integrity, safety, and regulatory compliance at every stage of operation. Our inspection services include:
- Pre-repair inspections: Assessment of a vessel’s technical condition before planned repairs to identify areas requiring intervention and ensure the effectiveness of the repair process.
- Pre-conversion inspections: Detailed structural and system analysis before planned modifications to evaluate feasibility and the scope of required work.
- Hull integrity assessments: Use of non-destructive testing (NDT) to assess hull integrity and identify potential damage or corrosion.
- Machinery and system evaluations: Examination of onboard machinery and systems to prevent failures and ensure operational reliability.
- Regulatory compliance audits: Conducting compliance audits with classification society requirements and flag state administration to ensure full adherence to regulations.
Design
From Draft to Class Compliance
We deliver innovative and efficient ship designs, integrating performance optimization, regulatory compliance, and cost-effective construction methods:
- Conceptual and feasibility studies
- Hydrodynamic and structural analysis
- Digital prototyping with CAD and simulation tools
- 3D scanning and reverse engineering
- Compliance with IMO, SOLAS, and classification society requirements
Supervision
Ensuring Quality at Every Stage
We provide expert supervision throughout the shipbuilding, repair, and conversion processes, ensuring adherence to specifications, safety standards, and project timelines:
- Worksite inspections and quality assurance
- Structural and system installation oversight
- Coordination between shipyards, vendors, and regulatory bodies
- Safety compliance verification to meet class society and flag state requirements
- Problem-solving and risk mitigation during execution
Engineering
Structural and System Integration
Our engineering expertise ensures vessels operate safely, efficiently, and in compliance with global standards:
- Structural engineering for hull integrity and weight optimization
- Mechanical and piping systems design
- Electrical and automation systems integration
- Vibration and noise analysis for comfort and efficiency
- Environmental engineering (emission control, ballast water treatment)
Commissioning
Delivering Operational Readiness
Thorough testing and verification ensure vessels are fully operational and ready for deployment:
- Pre-commissioning inspections of all onboard systems
- Calibration and optimization of propulsion, HVAC, and automation
- Full-scale operational and sea trials
- Crew training on new systems and operational procedures
- Final certification and client handover
Purchase
Reliable Supply Chain Management
A strong procurement strategy ensures on-time delivery of high-quality components and materials for shipbuilding and repairs:
- Supplier evaluation and selection based on quality and reliability
- Contract negotiation for optimal cost and delivery terms
- Inventory control to prevent project delays
- Logistics coordination for efficient material flow
- Supplier quality audits to ensure compliance with specifications
Project Management
Seamless Execution from Start to Finish
Effective coordination and control are essential for delivering shipbuilding and repair projects on time and within budget. We ensure:
- Strategic planning and milestone tracking
- Resource allocation for personnel, equipment, and materials
- Risk identification and mitigation strategies
- Progress monitoring and adaptive project adjustments
- Transparent reporting and stakeholder communication

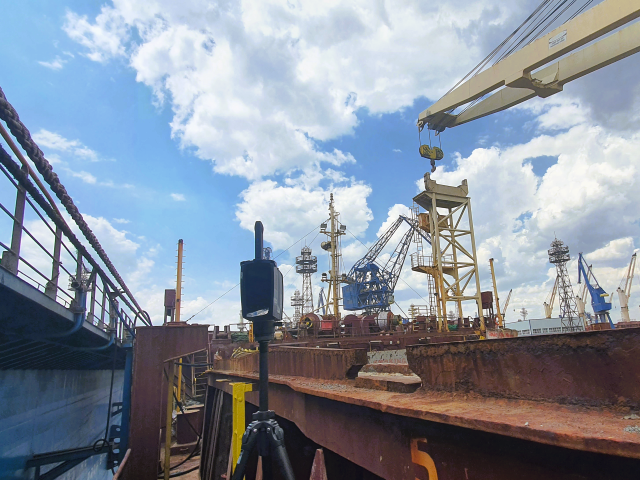
We are located in the historic city of Gdańsk, Poland, a place with over a thousand years of rich history shaped by various cultures over the centuries. Gdańsk is a key industrial hub, particularly known for its shipbuilding heritage. It is also home to the Gdańsk University of Technology, where aspiring engineers receive the education needed to pursue careers in the maritime industry. The region boasts numerous local private companies that, for decades, have been providing professional services to Baltic shipyards and the owners of boats, yachts, merchant ships, ferries, and cruise liners.
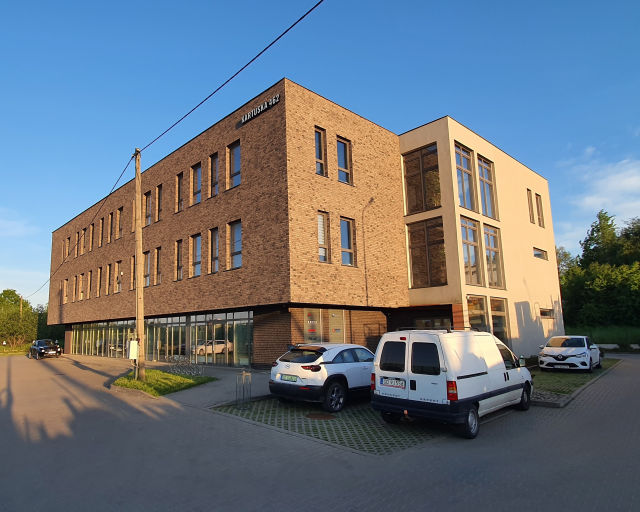
We are located in the historic city of Gdańsk, Poland, a place with over a thousand years of rich history shaped by various cultures over the centuries. Gdańsk is a key industrial hub, particularly known for its shipbuilding heritage. It is also home to the Gdańsk University of Technology, where aspiring engineers receive the education needed to pursue careers in the maritime industry. The region boasts numerous local private companies that, for decades, have been providing professional services to Baltic shipyards and the owners of boats, yachts, merchant ships, ferries, and cruise liners.
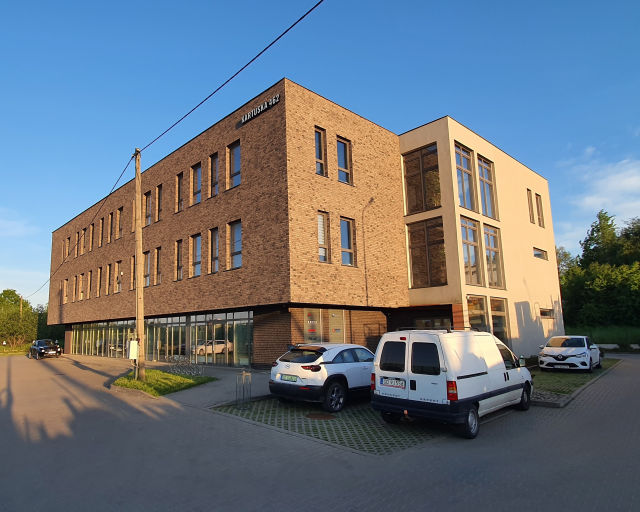
To complete your project professionally we use spacious industrial hall covering 430 square meters. Situate in Gdynia in close proximity to the well-known Tri-City shipyards. This strategic location not only provides us with the necessary space and infrastructure but also places us close to key maritime and industrial hubs, facilitating smoother logistics, collaboration, and access to essential resources for our operations.
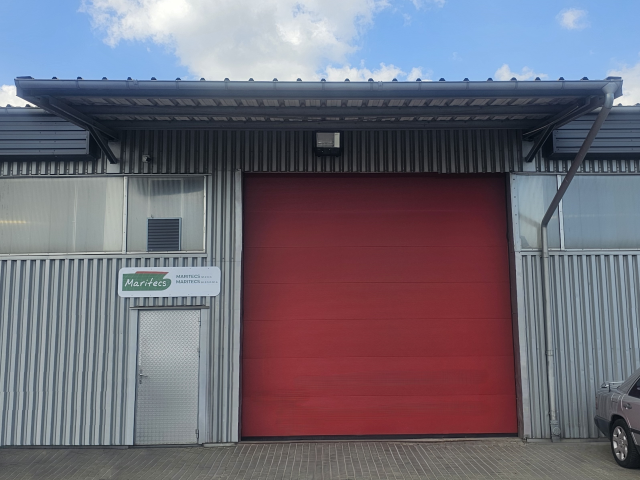
To complete your project professionally we use spacious industrial hall covering 430 square meters. Situate in Gdynia in close proximity to the well-known Tri-City shipyards. This strategic location not only provides us with the necessary space and infrastructure but also places us close to key maritime and industrial hubs, facilitating smoother logistics, collaboration, and access to essential resources for our operations.
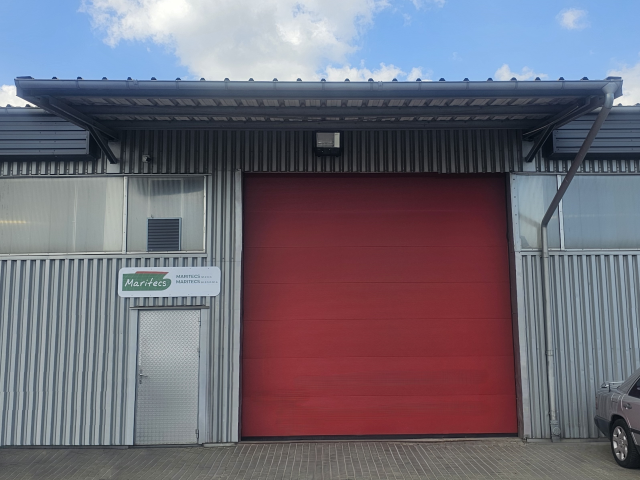
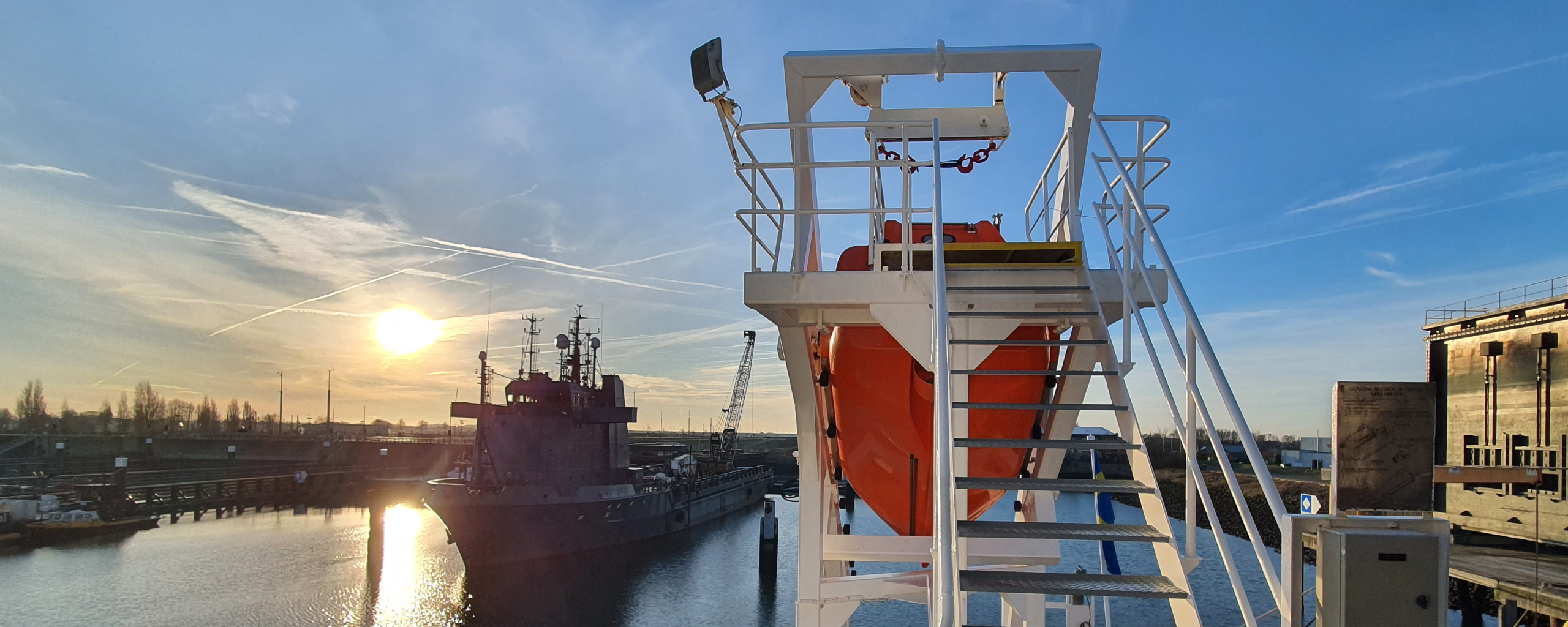
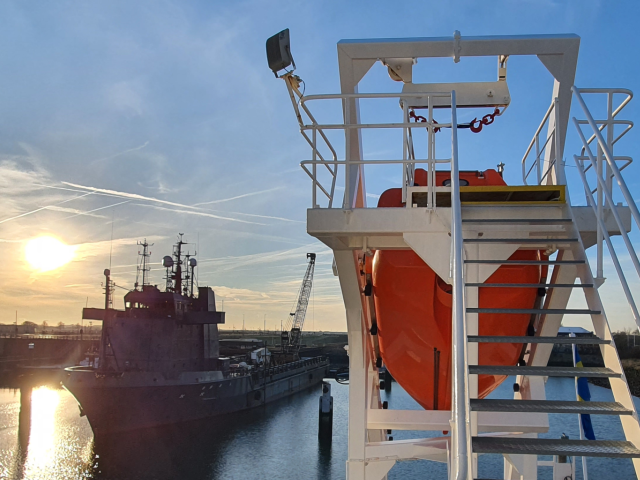